รับประกันปี
0
คำสั่งซื้อ
0
+
Machine Models
0
+
เครื่องทำความสะอาดเลเซอร์ AccTek
The laser cleaning machine is a powerful tool to remove various surface impurities using laser cleaning technology. It uses a powerful laser beam pointed at the surface of the cleaning material, the laser beam rapidly heats and evaporates the unwanted material, which is then removed by a suction system. The laser beam can be adjusted to different intensities and wavelengths depending on the material being cleaned and the degree of contamination. The laser cleaning process is a non-contact cleaning method that does not require any chemicals or abrasive materials, making it a safe and environmentally friendly option for surface cleaning. It is also an exact process that can remove the smallest particles or residues without damaging the surface or leaving any residue.
When selecting a laser cleaning machine, it is important to consider the specific needs of your application, such as the size and type of surface to be cleaned, the degree of contamination, and the precision required. If you are ready to buy a laser cleaning machine, you can contact us anytime. AccTek is a professional manufacturer of laser cleaning machines, we can provide and customize laser cleaning machines for you according to your needs and will provide you with competitive prices. The laser cleaning machine is an efficient and versatile solution for removing impurities from a variety of surfaces. They offer many advantages over traditional cleaning methods, including precision, speed, efficiency, and safety. With their ability to clean surfaces without harsh chemicals or abrasive materials, laser cleaners are also an environmentally friendly and cost-effective solution for businesses looking to maintain their equipment and facilities.
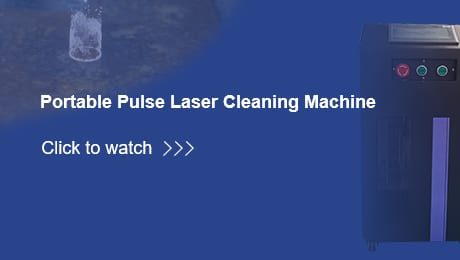
เล่นวิดีโอเกี่ยวกับ เครื่องทำความสะอาดเลเซอร์พัลส์ 100W
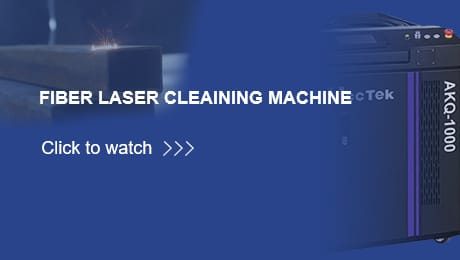
เล่นวิดีโอเกี่ยวกับ เครื่องทำความสะอาดไฟเบอร์เลเซอร์
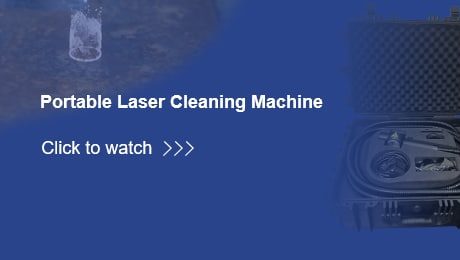
เล่นวิดีโอเกี่ยวกับ เครื่องทำความสะอาดเลเซอร์แบบพกพา
เครื่องทำความสะอาดเลเซอร์แบบมือถือ
เครื่องทำความสะอาดเลเซอร์แบบพกพาเป็นอุปกรณ์แบบพกพาที่ใช้เทคโนโลยีเลเซอร์เพื่อขจัดสิ่งปนเปื้อน สนิม สี และสารที่ไม่พึงประสงค์อื่นๆ ออกจากพื้นผิว ลำแสงเลเซอร์ถูกสร้างขึ้นโดยเครื่องกำเนิดเลเซอร์และส่งผ่านสายเคเบิลในสายไปยังอุปกรณ์พกพาที่โฟกัสลำแสงไปยังพื้นผิวที่จะทำความสะอาด
เครื่องทำความสะอาดเลเซอร์แบบใช้มือถือถูกใช้ในหลากหลายอุตสาหกรรม รวมถึงยานยนต์ การบินและอวกาศ และการผลิต ในอุตสาหกรรมเหล่านี้ ความสะอาดของเครื่องจักรและอุปกรณ์มีความสำคัญต่อการรักษาประสิทธิภาพและป้องกันความเสียหาย นอกจากนี้ยังใช้ในโครงการบูรณะ เช่น การทำความสะอาดอาคารประวัติศาสตร์และอนุสรณ์สถาน
ข้อดีของเครื่องตัดเลเซอร์
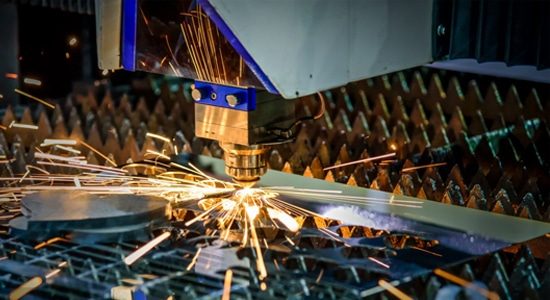
Non-contact Cleaning
Non-contact Cleaning
Safely removes contaminants without physical contact, preventing surface damage.
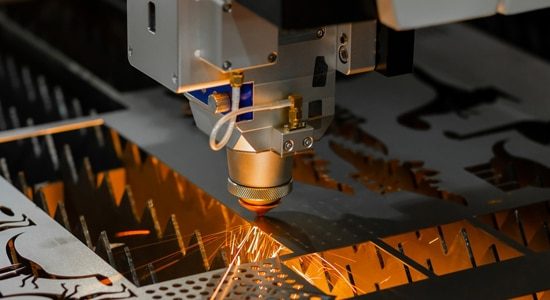
ประสิทธิภาพสูง
ประสิทธิภาพสูง
Rapidly cleans surfaces, reducing downtime and increasing productivity.
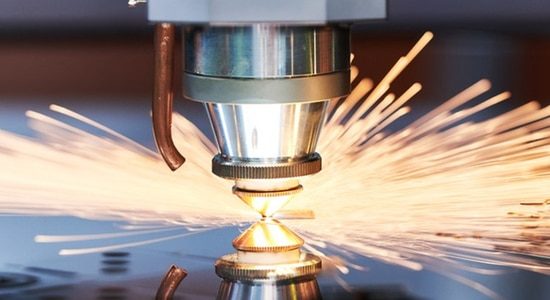
ความเก่งกาจ
ความเก่งกาจ
Works on various materials and contaminants, adaptable to diverse applications.
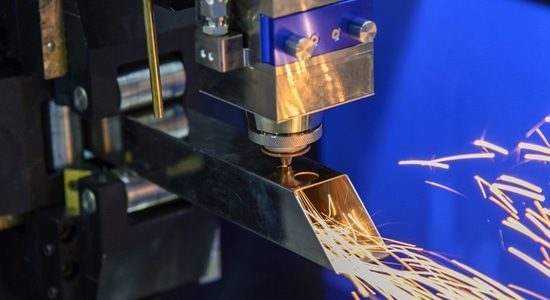
Precision and Control
Precision and Control
Targets specific areas with accuracy, preserving delicate surfaces.
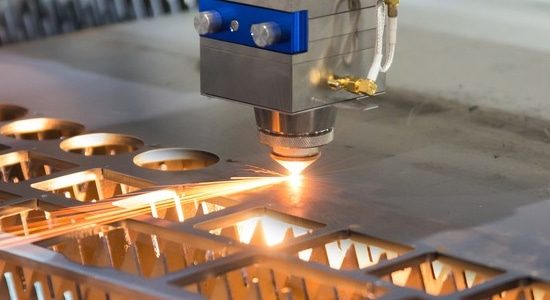
No Consumables Required
No Consumables Required
Eliminates the need for chemicals or abrasive materials, reducing operational costs.
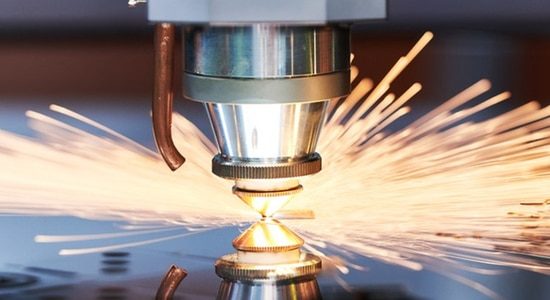
Environmentally Friendly
Environmentally Friendly
Dry process without chemicals, minimizing environmental impact and health risks.
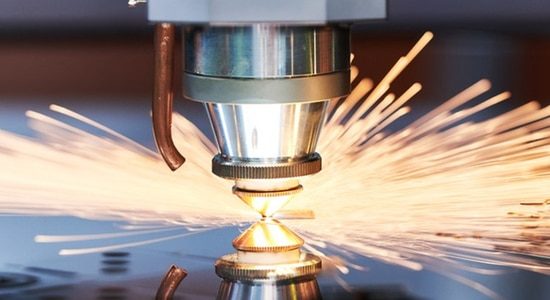
คุ้มค่า
คุ้มค่า
Saves on labor, materials, and disposal, offering long-term cost savings.
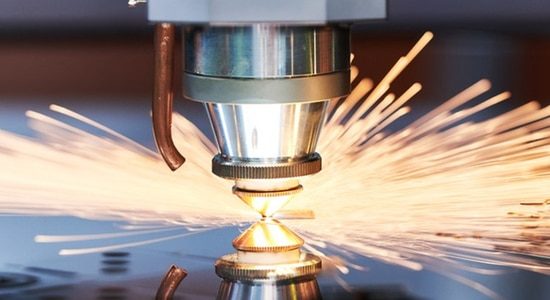
Conservation of Original Surface
Conservation of Original Surface
Gently cleans without altering the substrate, preserving its integrity and appearance.
คำถามที่พบบ่อย
Do Laser Cleaning Machines Work?
Yes, laser cleaning machines do work and have proven to be effective in various applications. Laser cleaning uses high-powered lasers to remove contaminants, such as rust, paint, or coatings, from surfaces without damaging the underlying material.
These machines work by delivering short bursts of laser energy to the surface, which vaporize or ablate the unwanted material. The process is highly precise, allowing for selective removal of contaminants while leaving the substrate intact.
Laser cleaning machines are used in industries like automotive, aerospace, electronics, cultural heritage preservation, and more. They offer advantages such as non-contact cleaning, minimal waste generation, and reduced need for chemical solvents, making them environmentally friendly and cost-effective solutions for many cleaning tasks.
เครื่องทำความสะอาดเลเซอร์ราคาเท่าไหร่?
The price of a laser cleaning machine can vary greatly depending on several factors including:
- Power and Capabilities: Higher-powered machines capable of removing tougher contaminants or covering larger surface areas will generally be more expensive.
- Size and Type: Standalone handheld units are typically less expensive than larger, automated systems designed for industrial use.
- Brand and Quality: Well-known brands with a reputation for quality and reliability may command higher prices.
- Additional Features: Machines with advanced features such as automation, multiple laser heads, or specialized optics may cost more.
- Market Demand: Prices may vary based on factors such as supply and demand dynamics, as well as fluctuations in the manufacturing and technology sectors.
What Are The Ongoing Operating Costs of A Laser Cleaning Machine?
The operating costs of a laser cleaning machine can include several factors:
- Electricity: Laser cleaning machines require electricity to power the laser source, cooling systems, and other components. The exact electricity consumption will depend on the power of the laser, the duration of use, and any additional systems such as ventilation or cooling.
- Consumables: While laser cleaning itself doesn’t typically require consumables like chemicals or abrasive materials, there may be ancillary consumables needed for maintenance purposes. This could include items such as protective lenses, filters, or gases used in the laser system.
- Maintenance: Regular maintenance is necessary to ensure the continued performance and reliability of the laser cleaning machine. This may involve tasks such as cleaning optical components, replacing worn parts, calibrating the system, and servicing the laser source. Maintenance costs can vary depending on the complexity of the machine and the frequency of use.
- Operator Training: Proper operator training helps ensure the safe and efficient operation of laser cleaning machines. Training costs may include initial training sessions as well as ongoing education to stay updated on best practices and safety procedures.
- Safety Equipment: Depending on the application and local regulations, additional safety equipment such as personal protective gear or safety interlocks may be required. These items incur additional costs.
- Downtime: In the event of equipment failure or maintenance requirements, there may be associated costs related to downtime, including lost productivity and potential delays in production schedules.
ข้อเสียของการทำความสะอาดด้วยเลเซอร์คืออะไร?
While laser cleaning offers many advantages, there are also some potential disadvantages to consider:
- Initial Cost: Laser cleaning machines can be expensive to purchase compared to traditional cleaning methods. The initial investment may be prohibitive for some businesses or applications.
- Safety Concerns: Laser cleaning involves the use of high-intensity laser beams, which can pose safety risks if not used properly. Operators need to be trained in laser safety protocols, and appropriate safety measures must be in place to protect against hazards such as eye damage or fires.
- Limited Materials: While laser cleaning is effective for many materials, some surfaces may be difficult or impossible to clean with lasers. Certain materials, such as transparent plastics or materials with highly reflective surfaces, may not respond well to laser cleaning.
- Surface Damage: While laser cleaning is generally gentle on surfaces, there is still a risk of damaging delicate materials or substrates if the laser parameters are not carefully controlled. For example, excessive heat or power levels could cause thermal damage or changes in material properties.
- Environmental Considerations: While laser cleaning itself is a clean process that doesn’t involve the use of chemicals or produce hazardous waste, the energy consumption of the laser system and associated equipment can have environmental impacts. Additionally, some laser systems may require cooling systems that consume water or other resources.
- Limited Reach and Accessibility: Laser cleaning requires line-of-sight access to the surface being cleaned. This means that it may not be suitable for cleaning complex or hard-to-reach areas where direct access is limited.
- Complexity: Laser cleaning machines can be complex pieces of equipment that require specialized knowledge to operate and maintain. This complexity can lead to higher training and maintenance costs.
- Regulatory Compliance: Depending on local regulations and industry standards, there may be specific requirements or restrictions regarding the use of laser cleaning equipment. Compliance with these regulations may add complexity or cost to the implementation of laser cleaning processes.
Will Laser Cleaning Damage Material?
Laser cleaning is generally considered a non-destructive cleaning method when used properly. However, there is still a risk of damaging certain materials or substrates if the laser parameters are not carefully controlled or if inappropriate settings are used. Here are some factors to consider regarding the potential for material damage:
- Material Sensitivity: Some materials are more sensitive to heat and energy than others. For example, certain plastics, composite materials, or heat-sensitive coatings may be more prone to damage from laser cleaning. Understanding the characteristics of the material being cleaned can help adjust laser parameters accordingly.
- Laser Settings: The power, pulse duration, and other laser parameters must be optimized for the specific material and contaminants being cleaned. Using too much power or applying the laser for too long can result in excessive heating and potential damage to the surface.
- Surface Characteristics: The condition and characteristics of the surface being cleaned can also affect the likelihood of damage. Rough or uneven surfaces may absorb laser energy differently, leading to localized heating and potential damage.
- Surface Coatings: Laser cleaning can remove surface coatings such as paint or rust, but it’s important to consider the compatibility of these coatings with the laser process. Some coatings may be more difficult to remove or may require specific laser parameters to avoid damaging the underlying substrate.
- Quality of Equipment and Operator Skill: The quality of the laser cleaning equipment and the skill level of the operator play important roles in preventing material damage. Proper training and experience enable safe and effective operation of equipment.
What Types of Contaminants Are Laser Cleaning Machines Suitable For?
Laser cleaning machines are versatile tools capable of removing a wide range of contaminants from various surfaces. Some common types of contaminants that laser cleaning machines are suitable for include:
- Rust: Laser cleaning is highly effective for removing rust from metal surfaces. The laser energy can vaporize the rust layer, leaving behind a clean surface without damaging the underlying metal.
- Paint: Laser cleaning can efficiently remove paint from surfaces without the need for harsh chemicals or abrasive methods. It’s particularly useful for removing paint from metal, wood, or stone surfaces.
- Oxides and Scale: Laser cleaning is effective for removing oxide layers and scale buildup from metal surfaces, such as those found in welding applications or industrial equipment.
- Oil and Grease: Laser cleaning can remove oil, grease, and other organic contaminants from surfaces, making it useful for cleaning automotive parts, machinery, and industrial equipment.
- Corrosion and Surface Coatings: Laser cleaning can remove corrosion and surface coatings from a variety of materials, including metals, ceramics, and composites.
- Adhesive Residues: Laser cleaning can effectively remove adhesive residues from surfaces without damaging the underlying material. This makes it useful for cleaning adhesive bonds, labels, and decals.
- Carbon Deposits: Laser cleaning can remove carbon deposits from surfaces, such as those found in engine components, exhaust systems, or industrial equipment.
- Mold and Mildew: Laser cleaning can be used to remove mold and mildew from surfaces, particularly in applications where traditional cleaning methods may be impractical or ineffective.
What Is The Maximum Cleaning Area That A Laser Cleaning Machine Can Handle?
The maximum cleaning area that a laser cleaning machine can handle depends on several factors, including the type of laser source, the power of the laser, and the specific model of the machine. Here’s a breakdown based on the information provided:
Continuous Fiber Laser Cleaning Machines
- Standard cleaning width: 270mm
- Machines Below 2kW: Maximum cleaning width of 450mm
- Machines Above 2kW: Maximum cleaning width of 600mm
- เครื่องทำความสะอาดเลเซอร์พัลส์ 100W
- Standard Cleaning Area: 100x100mm
- Optional Cleaning Areas: 130x130mm, 150x150mm
- 200W Pulse Laser Cleaning Machine
- Standard Cleaning Area: 130x130mm
- Optional Cleaning Areas: 130x130mm, 150x150mm
- 300-1000W Pulse Laser Cleaning Machines
- Standard Cleaning Area: 150x150mm
- Optional Cleaning Areas: 180x180mm, 290x290mm
How To Maintain A Laser Cleaning Machine?
Maintaining your laser cleaning machine ensures its optimal performance, longevity, and safety. Here are some general maintenance practices for laser cleaning machines:
- Regular Cleaning: Keep the exterior of the machine clean and free from dust, debris, and any other contaminants that could interfere with its operation.
- Optical Component Inspection and Cleaning: Periodically inspect and clean the optical components, including lenses, mirrors, and windows, to ensure they are free from dirt, smudges, or damage that could affect the laser beam quality. Use appropriate cleaning materials and techniques to avoid scratching or damaging the optical surfaces.
- Check Cooling Systems: If the laser cleaning machine has cooling systems, such as water cooling or air cooling, regularly check them for proper functioning. Monitor coolant levels, clean filters, and perform any required maintenance according to the manufacturer’s recommendations.
- Inspect and Replace Consumable Parts: Some components of the laser cleaning machine, such as protective windows or filters, may need periodic inspection and replacement as they wear out over time. Follow the manufacturer’s guidelines for the replacement of consumable parts.
- Monitor Laser Parameters: Regularly check and calibrate laser parameters such as power output, pulse duration, and beam quality to ensure they are within the specified range for optimal cleaning performance. Adjust as necessary to maintain consistent cleaning results.
- Software Updates: Keep the machine’s control software up to date by installing any available updates or patches provided by the manufacturer. Updated software can improve performance, add new features, and address potential security vulnerabilities.
- Operator Training: Ensure that operators are properly trained in the safe and effective operation of the laser cleaning machine. Provide refresher training as needed to keep operators up to date on best practices and safety procedures.
- Documentation and Records: Maintain detailed records of maintenance activities, including inspections, repairs, and part replacements. This documentation can help track the machine’s maintenance history and identify any recurring issues that may need attention.
- Safety Checks: Regularly inspect safety features such as interlocks, emergency stop buttons, and warning indicators to ensure they are functioning correctly. Address any issues promptly to maintain a safe working environment.
รับโซลูชันเลเซอร์
เราสามารถปรับแต่งการออกแบบตามความต้องการของคุณ คุณเพียงแจ้งความต้องการของคุณให้เราทราบ แล้ววิศวกรของเราจะจัดหาโซลูชันแบบเบ็ดเสร็จให้คุณโดยเร็วที่สุด ราคาอุปกรณ์เลเซอร์ของเรามีการแข่งขันสูงมาก โปรดติดต่อเราเพื่อขอใบเสนอราคาฟรี หากคุณต้องการบริการเกี่ยวกับอุปกรณ์เลเซอร์อื่นๆ คุณสามารถติดต่อเราได้เช่นกัน