년 보증
0
명령
0
+
Machine Models
0
+
AccTek 혼합 레이저 절단기
One of the standout features of a mixed laser cutting machine is its ability to cut a wide variety of materials, including metal, wood, acrylic, and more. This is achieved by combining two different types of laser technology (CO2 and fiber), which work in tandem to provide precise and efficient cuts.
The mixed laser cutting machine is designed with dual heads, the CO2 laser is very suitable for cutting materials such as wood and acrylic, while the fiber laser is more suitable for cutting metal. By using two lasers in one machine, hybrid laser cutters can process a wider range of materials than many other machines on the market. With its advanced laser technology and cutting-edge software, it delivers accurate, efficient cuts every time, while minimizing waste and increasing productivity.
Whether you’re cutting intricate designs for jewelry, furniture, or signage, or making precision cuts for automotive parts, aerospace components, or medical devices, a mixed laser cutting machine can do the job. With its powerful laser source, it handles both thick and thin materials with ease and provides clean, precise cuts without warping, burning, or charring.
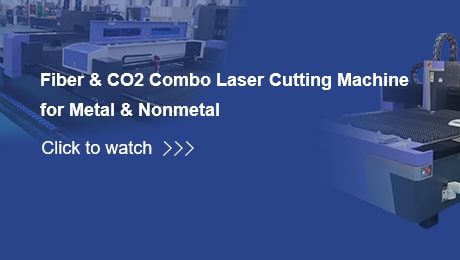
동영상 재생 정보 섬유 및 CO2 레이저 절단기
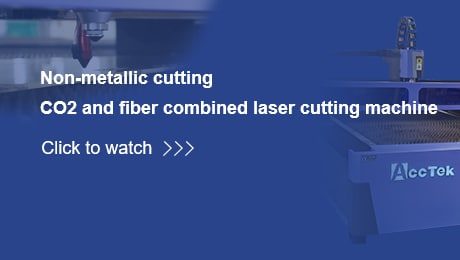
동영상 재생 정보 CO2 및 파이버 레이저 절단기
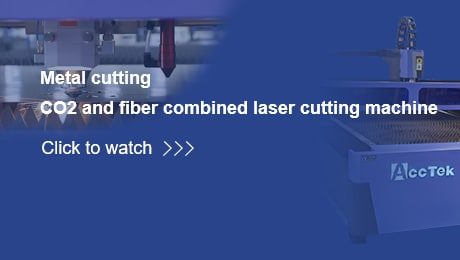
동영상 재생 정보 섬유 및 CO2 레이저 절단기
혼합 레이저 절단기의 장점

다재
다재
Cuts metals and non-metals with precision, expanding application range.
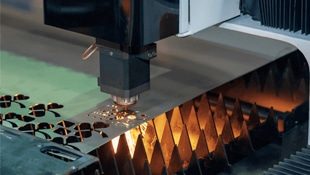
비용 효율성
비용 효율성
Saves on machine costs, energy consumption, and maintenance.
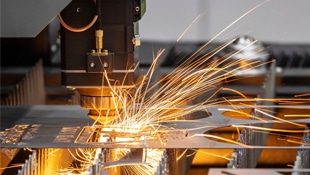
Increased productivity
Increased productivity
Seamless switching between lasers reduces downtime, enhancing overall output.

높은 정밀도
높은 정밀도
Achieves intricate cuts with minimal tolerances for superior quality.
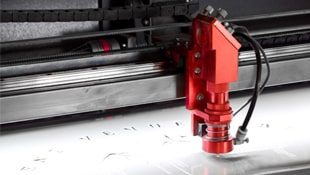
Reduced Waste
Reduced Waste
Minimizes material waste, leading to cost and environmental savings.

Reduced setup time
Reduced setup time
Streamlines setup process, saving valuable production time.
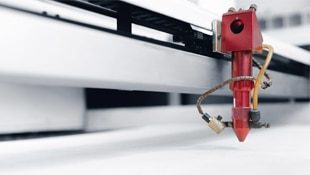
유연성
유연성
Adaptable for diverse material cutting needs, optimizing production flexibility.
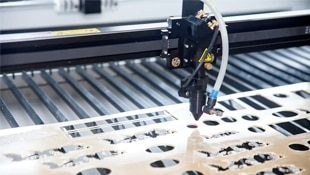
Enhanced automation
Enhanced automation
Advanced features automate tasks, reducing labor requirements and improving efficiency.
자주 묻는 질문
What Is A Mixed Laser Cutting Machine?
혼합 레이저 절단기는 파장이 다른 여러 레이저 발생기를 사용하여 다양한 재료를 절단할 수 있는 레이저 절단 장비입니다. 산업용 절단 응용 분야에서 일반적으로 사용되는 CO2 및 파이버 레이저의 이점을 제공하도록 설계되었습니다.
The mixed laser cutting machine can use different laser sources to cut a range of materials including metals, non-metals, plastics, fabrics, and composites. Each laser source has its unique wavelength, which makes it suitable for cutting different materials at different thicknesses and with different levels of precision.
혼합 레이저 절단기는 아크릴, 목재, 가죽 등 비금속 재료 절단을 위한 CO2 레이저 소스와 강철, 알루미늄 등 금속 절단을 위한 파이버 레이저 소스를 포함한다. 하나의 기계에서 여러 레이저 소스를 사용하면 혼합 레이저 절단 기계가 다재다능하고 효율적이 되어 생산 시간이 단축되고 절단 기능이 더 넓어집니다.
혼합 레이저 절단기는 얼마입니까?
The price of a mixed laser cutting machine can vary widely, depending on several factors such as the size, power, software, quality, and features of the machine. In addition, prices may also be affected by manufacturers, locations, and other factors such as taxes and shipping. Generally speaking, the price of a mixed laser cutting machine is more expensive than a single-type laser cutting machine, because it needs to purchase both CO2 and fiber laser generators.
Prices for mixed laser cutting machines range from $20,000 to $400,000. Most models range in price from $30,000 to $150,000. If you plan to buy a mixed laser cutting machine, you can contact us. AccTek’s engineers can provide you with competitive prices according to your needs and budget.
혼합 레이저 절단기의 수명은 얼마나 됩니까?
The lifespan of a mixed laser cutting machine can vary depending on several factors, including machine quality, level of maintenance, intensity of use, and operating environment. Generally speaking, the service life of a well-maintained mixed laser cutting machine can reach about 8-10 years. Note, however, that this is an estimate only, and the actual lifespan may vary.
To ensure that your mixed laser cutting machine lasts as long as possible, it is essential to follow the manufacturer’s recommended maintenance schedule. Use the machine correctly avoid overuse, and place the machine in a dry environment. Additionally, regular inspections and repairs by a qualified technician can help identify and fix any problems before they cause significant damage to the machine.
How Much Does A Mixed Laser Cutting Machine Cost To Operate?
The cost of operating a mixed laser cutting machine can vary significantly based on several factors such as the type and power of the laser, the materials being cut, the frequency of use, maintenance requirements, electricity costs, and labor costs. Here are some key cost components to consider:
- Energy Consumption: Laser-cutting machines consume electricity to power the laser source, the machine itself, and any associated cooling systems. The energy consumption depends on the power of the laser and the duration of operation.
- Maintenance: Regular maintenance is necessary to keep the machine running smoothly and efficiently. This includes cleaning optics, replacing consumable parts like nozzles and lenses, and servicing mechanical components. Maintenance costs can vary based on the machine’s design and usage.
- Material Costs: The cost of materials being cut is a significant factor. Different materials have different cutting characteristics and may require adjustments to the laser settings or additional processing steps, affecting operating costs.
- Labor Costs: Labor costs include operator wages and any additional personnel required for setup, programming, and maintenance of the machine.
- Downtime Costs: Downtime due to machine breakdowns or maintenance can impact productivity and increase costs. Downtime can be minimized through preventive maintenance and timely repairs.
- Ventilation and Safety: Laser-cutting machines require proper ventilation and safety measures to protect operators and comply with regulations. Costs associated with ventilation systems, protective gear, and safety training should be considered.
- Depreciation and Financing: If the machine is purchased outright or financed, depreciation and financing costs should be factored into the overall operating expenses.
혼합 레이저 절단기는 무엇을 절단할 수 있습니까?
The mixed laser cutting machine is a versatile tool that can precisely cut a variety of materials. The types of materials that a mixed laser cutting machine can cut depend on the power, configuration, and capabilities of the specific machine. Typically, a mixed laser cutting machine can cut the following materials:
- Metal: It can cut various metals, including steel, aluminum, copper, brass, and titanium. It produces a high-powered laser beam that easily melts and vaporizes metal for clean, precise cuts.
- 플라스틱 : 아크릴, 폴리카보네이트, PVC, ABS, PET 등 다양한 종류의 플라스틱을 절단할 수 있습니다.
- 목재: 목재 및 MDF, 합판, 원목 등의 목재 기반 재료를 절단할 수 있습니다.
- 가죽: 천연 가죽과 인조 가죽을 포함하여 다양한 종류의 가죽 및 기타 유사한 재료를 절단할 수 있습니다.
- 원단 : 면, 실크, 폴리에스터, 나일론 등 다양한 종류의 원단을 재단할 수 있습니다.
- 유리: 강화 유리 및 붕규산 유리를 포함한 유리를 절단할 수 있습니다.
- 폼: 폴리우레탄 폼, 발포 폴리스티렌(EPS) 폼, 압출 폴리스티렌(XPS) 폼 등 다양한 유형의 폼을 절단할 수 있습니다.
- 고무 : 네오프렌, 실리콘, 천연고무 등 다양한 종류의 고무를 절단할 수 있습니다.
혼합 레이저 절단기의 단점은 무엇입니까?
While mixed laser cutting machines offer numerous advantages, they also have some disadvantages to consider:
- Complexity: Mixed laser cutting machines are more complex than single-purpose machines. They typically require additional setup time, calibration, and programming due to the integration of multiple laser types or cutting processes. This complexity can lead to higher initial investment costs and may require more extensive operator training.
- Maintenance: Maintaining a mixed laser cutting machine can be more challenging due to the presence of multiple laser sources and cutting technologies. Each component may have unique maintenance requirements, leading to increased downtime and maintenance costs compared to single-purpose machines.
- Limited Compatibility: Mixed laser cutting machines may not be compatible with all materials and thicknesses. Certain materials or combinations of materials may require specific laser wavelengths or cutting methods that the machine cannot accommodate. This limitation can restrict the range of applications and materials that can be processed.
- Cost: Mixed laser cutting machines tend to have higher upfront costs compared to single-purpose machines due to their advanced capabilities and integrated technologies. Additionally, operating costs, including energy consumption, maintenance, and consumables, may be higher due to the complexity of the equipment.
- Performance Trade-offs: While mixed laser cutting machines offer versatility, they may not excel in every cutting application compared to dedicated laser cutting systems. For example, a mixed laser cutting machine that combines CO2 and fiber lasers may not achieve the same cutting quality or speed as a dedicated CO2 or fiber laser cutter for certain materials or thicknesses.
- Space Requirements: Mixed laser cutting machines often require more space than single-purpose machines due to the integration of multiple laser sources and additional equipment, such as chiller units and exhaust systems. This can be a consideration for facilities with limited space or layout constraints.
- Complexity in Programming: Programming a mixed laser cutting machine to perform various cutting tasks with different laser sources and parameters can be more complex than programming a single-purpose machine. Operators may need advanced programming skills and specialized software to optimize cutting processes and achieve desired results.
어떤 산업에서 혼합 레이저 절단기가 가장 일반적으로 사용됩니까?
Mixed laser cutting machines find applications across various industries where versatile cutting capabilities are required. Some industries where mixed laser cutting machines are commonly used include:
- Automotive: Mixed laser cutting machines are employed in the automotive industry for cutting a wide range of materials used in vehicle manufacturing, such as steel, aluminum, and composites. They are used for cutting components like body panels, chassis parts, exhaust systems, and interior trim with high precision and efficiency.
- Aerospace: In the aerospace industry, mixed laser cutting machines are utilized for cutting lightweight materials like aluminum, titanium, and composites to fabricate aircraft components such as fuselage panels, wing sections, and engine parts. The ability to switch between different laser types enables manufacturers to handle a variety of materials and thicknesses.
- Metal Fabrication: Mixed laser cutting machines are widely used in metal fabrication shops for cutting metal sheets, tubes, and profiles for various applications. They offer the flexibility to cut different metals like steel, stainless steel, and aluminum, as well as non-metal materials like plastics and ceramics, catering to diverse customer requirements.
- Electronics: Mixed laser cutting machines are employed in the electronics industry for the precision cutting of circuit boards, semiconductor materials, and electronic components. They enable manufacturers to achieve intricate designs and precise dimensions critical for electronic devices and microelectronics production.
- Medical Devices: In the medical device manufacturing sector, mixed laser cutting machines are utilized for cutting medical-grade metals, polymers, and biocompatible materials to fabricate components for surgical instruments, implants, prosthetics, and medical devices. The ability to switch between laser types allows for processing a wide range of materials used in medical applications.
- Architectural and Interior Design: Mixed laser cutting machines are used in architectural and interior design industries for cutting decorative panels, signage, and intricate patterns in materials like wood, acrylic, glass, and metal. They enable designers to create custom designs with precision and detail, enhancing the aesthetic appeal of architectural spaces and interior environments.
- Packaging and Labeling: Mixed laser cutting machines find applications in the packaging and labeling industry for cutting flexible and rigid packaging materials, such as paperboard, cardboard, plastics, and foils. They are used for producing packaging prototypes, custom packaging designs, and intricate labels with high accuracy and speed.
How To Maintain A Mixed Laser Cutting Machine?
Maintaining your hybrid laser cutter helps ensure optimal performance, minimize downtime, and extend the life of your equipment. Here are some maintenance tips:
- Regular Cleaning: Keep the machine clean by regularly removing dust, debris, and residues from the cutting area, optics, and surrounding components. Use appropriate cleaning materials and methods recommended by the manufacturer to avoid damaging sensitive parts.
- Optics Inspection and Cleaning: Periodically inspect the optics, including lenses, mirrors, and windows, for signs of contamination, scratches, or damage. Clean the optics using a lint-free cloth and a gentle cleaning solution to remove dirt, oils, and residues that can affect laser beam quality and cutting accuracy.
- Check Gas Supply: Ensure a consistent and sufficient supply of assist gases, such as oxygen, nitrogen, or air, depending on the cutting requirements and materials being processed. Monitor gas pressure and purity levels to maintain optimal cutting performance and quality.
- Monitor Cooling Systems: Regularly inspect and maintain the cooling systems, including chiller units and water circulation systems, to prevent overheating and ensure proper temperature control of laser components. Clean filters, check coolant levels, and perform routine maintenance according to the manufacturer’s guidelines.
- Calibration and Alignment: Periodically calibrate and align the laser beam delivery system, including mirrors, lenses, and beam delivery optics, to ensure accurate beam positioning and focus. Misalignment or degradation of optical components can affect cutting quality and consistency.
- Software Updates and Calibration: Keep the machine’s control software up to date with the latest updates and patches provided by the manufacturer. Perform regular software calibration and parameter adjustments to optimize cutting parameters and maintain consistent cutting results.
- Inspect and Replace Consumables: Regularly inspect and replace consumable parts such as nozzles, lenses, and cutting tips as needed. Worn or damaged consumables can affect cutting quality, efficiency, and safety. Follow the manufacturer’s recommendations for replacement intervals and compatible parts.
- Lubrication and Maintenance of Mechanical Components: Lubricate and maintain mechanical components, such as guide rails, bearings, and drive systems, to ensure smooth and precise motion of the cutting head and other moving parts. Clean and grease components according to the manufacturer’s guidelines to prevent wear and prolong component life.
- Safety Checks and Training: Conduct regular safety checks of the machine and its surroundings to identify potential hazards and ensure compliance with safety regulations. Provide comprehensive training for operators on safe machine operation, maintenance procedures, and emergency protocols.
레이저 솔루션 받기
우리는 귀하의 요구 사항에 따라 디자인을 사용자 정의할 수 있습니다. 요구사항만 알려주시면 당사 엔지니어가 최단 시간 내에 턴키 솔루션을 제공할 것입니다. 우리의 레이저 장비 가격은 매우 경쟁력이 있습니다. 무료 견적을 받으려면 저희에게 연락하십시오. 다른 레이저 장비 관련 서비스가 필요한 경우 당사에 문의할 수도 있습니다.