年保証
0
注文
0
+
Machine Models
0
+
AccTek ファイバーレーザー切断機
ファイバーレーザー切断機は、高品質、高速、高精度、高効率の全自動CNCレーザー金属切断システムです。ファイバーレーザー切断機は、さまざまな金属を処理するように特別に設計されており、金属切断プロセスを完了するための優れたパートナーです。ファイバーレーザー切断機には、さまざまな厚さの金属を切断できるさまざまなレーザー出力 (1000W から 50000W) があります。
AccTek は、レーザー切断機の製造において 10 年の経験があり、世界中のお客様にプロフェッショナルなレーザー ソリューションを提供することに取り組んでいます。厳密な構造解析により最適化された機械設計技術を基に、高精度なファイバーレーザー切断機を製造しています。ファイバーレーザー切断機の専門メーカーとして、さまざまな顧客のニーズを満たすために、さまざまな出力とモデルのファイバーレーザー切断機を設計しました。 AccTek は、厳格な組み立てプロセスと世界クラスのブランド部品を実行して、高い切断精度と強力な切断能力を確保し、板金加工業者の生産性と収益性を最大化します。

についてのビデオを再生 ファイバーレーザー切断機
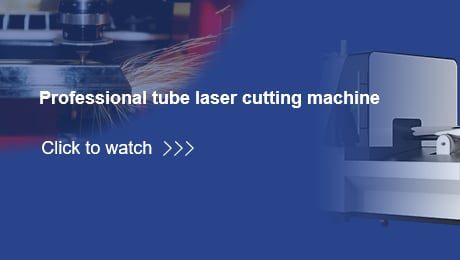
についてのビデオを再生 チューブレーザー切断機
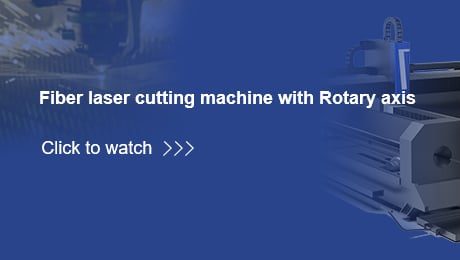
についてのビデオを再生 チューブとシートのレーザー切断機
シートファイバーレーザー切断機は、ファイバーレーザージェネレーターを動力として使用する、板金用に特別に設計されたレーザー切断機です。新開発のファイバーレーザー発生装置を採用し、ワーク表面に高エネルギー密度のレーザー光を出力し、レーザー照射部を溶融・気化させ、高速・高精度な完全自動切断を実現。
Sheet fiber laser cutting machines can cut all types of metals, from mild steel to stainless steel as well as some non-ferrous metals. However, it may be difficult to cut some highly reflective metal materials, such as copper and aluminum. In addition, the thick plate cutting ability of the plate fiber laser cutting machine is improved with the increase of the power of the fiber laser generator, and the cutting speed will also be significantly improved. Fiber laser cutting machines for sheet metal offer a good compromise in terms of cut quality, cutting speed, operating costs, and profitability.
チューブファイバーレーザー切断機は、金属管を切断するために特別に設計されたレーザー切断機で、金属管の切断プロセスを効率的に完了できます。チューブ、パイプ、および構造用鋼の切断と加工に関しては、AccTek はあらゆる製造ニーズに対応するソリューションを備えています。チューブファイバーレーザー切断機は、優れたレーザー切断技術を提供するだけでなく、多くの追加処理機能を統合して、メーカーに付加価値の利点をもたらします。
チューブファイバーレーザー切断機は、すべての金属チューブを高速かつ正確に切断できます。チューブ レーザー切断システムは、インテリジェントな監視、設定、切断機能など、多くのインテリジェントな機械機能を統合しています。これらの自動化機能により、操作の利便性と機械の切断効率が向上します。チューブファイバーレーザー切断機の幅広い機能により、これらの機械は多くの産業やさまざまな用途に最適です。
チューブとシートのファイバーレーザー切断機は、金属チューブとシートの高効率切断に使用できるデュアルパーパスファイバーレーザー切断機です。頑丈なスチールベッド、ラックドライブシステム、およびファイバーレーザー切断機の優れた切断精度と効率を保証するプロのチューブおよびシートレーザー切断CNCシステムを採用しています。チューブとシートのファイバーレーザー切断機は、金属看板、室内装飾、板金加工などの金属製造業界で徐々に役割を果たしています。
The tube and sheet fiber laser cutting machine integrates sheet cutting and tube cutting into one laser cutting machine. You can reap the benefits of laser cutting with minimal investment and space while achieving excellent cutting performance. According to actual production needs, it can be equipped with fiber laser generators of various powers (1000-50000W), and of course, you can also choose to add an exchange worktable and a fully enclosed protective case.
レーザー切断機の利点

高精度
高精度
Achieves intricate cuts with tight tolerances, ensuring accuracy in complex geometries.

汎用性
汎用性
Cuts a wide range of materials, from metals to non-metallics, facilitating diverse applications.
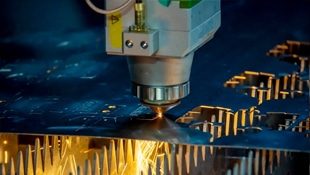
High Speed
High Speed
Rapid cutting rates lead to increased productivity and shorter lead times.

Minimal Maintenance
Minimal Maintenance
Requires little upkeep due to solid-state design, reducing downtime and costs.

Energy Efficiency
Energy Efficiency
Consumes less power, lowering operating costs and environmental impact.
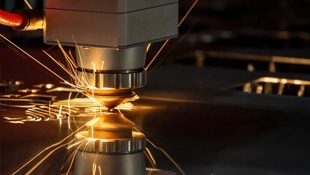
Narrow Kerf Width
Narrow Kerf Width
Produces a narrow cut, minimizing material waste and maximizing utilization.
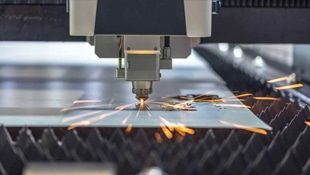
非接触切断
非接触切断
Avoids physical contact, preventing material distortion or damage, especially for delicate materials.

Automation Compatibility
Automation Compatibility
Easily integrates with automation systems for unmanned operation and enhanced efficiency.
よくある質問
What Is A Fiber Laser Cutting Machine?
The fiber laser cutting machine is a type of industrial tool used for cutting a variety of materials, primarily metals. It utilizes a high-powered fiber laser generator to create intense heat, which melts or vaporizes the material being cut. The machine directs the laser beam through a series of mirrors and lenses, focusing it onto the surface of the material with extreme precision.
One of the key components of a fiber laser cutting machine is the fiber laser generator itself. Unlike traditional CO2 laser generators, which use gases to generate the laser beam, fiber laser generators use optical fibers doped with rare-earth elements like erbium, ytterbium, or neodymium. This design allows for higher efficiency, greater reliability, and lower maintenance requirements.
Fiber laser cutting machines are highly versatile and can cut through a wide range of materials, including steel, stainless steel, aluminum, copper, brass, and various alloys. They are commonly used in industries such as manufacturing, aerospace, automotive, electronics, and construction for tasks like cutting sheet metal, pipes, tubes, and structural components.
These machines offer several advantages over other cutting methods, including faster cutting speeds, higher precision, cleaner cuts, reduced energy consumption, and lower operating costs. Additionally, they can be easily automated and integrated into production lines, making them ideal for high-volume manufacturing environments.
How Much Does A Fiber Laser Cutting Machine Cost?
The cost of a fiber laser cutting machine can vary widely depending on several factors such as the machine’s power output, cutting area size, brand, features, and additional accessories. Generally, smaller machines with lower power output and cutting area size will be less expensive than larger, more powerful models.
The price range for fiber laser cutting machines typically starts at around $12,500 to $34,000 for entry-level models with lower power outputs and smaller cutting areas. Mid-range machines with more features and higher power outputs may range from $50,000 to $100,000. High-end industrial-grade machines with larger cutting areas, higher power outputs, advanced features, and automation can cost hundreds of thousands of dollars.
It’s important to note that in addition to the initial purchase price, there may be additional costs associated with installation, training, maintenance, and ongoing operational expenses such as electricity and consumables like laser cutting gases and replacement parts. If you would like to obtain the most accurate pricing information you can contact AccTek Laser at any time. We can provide quotes based on specific requirements and custom options.
What Is The Working Principle Of A Fiber Laser Cutting Machine?
The working principle of a fiber laser cutting machine involves several key components working together to deliver precise and efficient cutting of materials. Here’s a simplified overview of the process:
- Generation of Laser Beam: The process begins with the generation of a high-powered laser beam within the fiber laser resonator. This resonator contains an optical fiber doped with rare-earth elements such as erbium, ytterbium, or neodymium. When stimulated by an external energy source (often diode lasers), these elements emit photons, creating the laser beam.
- Beam Delivery System: The laser beam is then guided through a series of mirrors and lenses within the machine’s beam delivery system. This system directs and focuses the laser beam onto the surface of the material to be cut.
- Material Interaction: When the focused laser beam strikes the material, it delivers a high concentration of energy to a small area, causing localized heating. Depending on the material and laser parameters, this heat can either melt or vaporize the material.
- Cutting Process: As the material absorbs the laser energy, it undergoes physical changes. For example, metals may melt or vaporize, while non-metallic materials may simply burn or evaporate. The motion system of the machine (comprising motors, drive systems, and CNC controls) precisely guides the laser beam along the desired cutting path, allowing for intricate shapes and contours to be cut with high accuracy.
- Assist Gas: In many cases, an assist gas, such as oxygen, nitrogen, or air, is used during the cutting process. This gas helps to remove molten material from the kerf (the cut path) and prevents the formation of slag, resulting in cleaner cuts.
- Cooling and Exhaust: The process generates heat, so cooling systems are employed to prevent overheating of critical components like the laser source and optics. Additionally, exhaust systems remove fumes and particles generated during cutting to maintain a safe working environment.
- Control and Monitoring: Throughout the cutting process, the machine’s control system continuously monitors various parameters, such as laser power, cutting speed, and gas pressure, to ensure optimal performance and quality.
ファイバーレーザー切断機はどのくらいの厚さまで切断できますか?
Fiber laser cutting machines are indeed primarily used for cutting metal, and their cutting thickness capability for metal materials varies depending on factors like laser power, material type, and machine specifications. Here are some approximate thickness ranges for common metals cut with fiber laser machines:
- Mild Steel: Fiber laser cutting machines can typically cut mild steel up to several inches thick, depending on the machine’s power. For example, machines with higher power outputs can cut thicker mild steel sections more efficiently.
- Stainless Steel: Similar to mild steel, fiber laser machines can cut stainless steel up to several inches thick, again depending on the laser power and specific material properties.
- Aluminum: Aluminum is also commonly cut with fiber laser machines. The thickness capability for aluminum is generally similar to mild steel and stainless steel, with machines capable of cutting aluminum sections several inches thick.
- Other Metals: Fiber lasers can also cut other metals such as copper, brass, titanium, and various alloys. The cutting thickness for these metals can vary depending on their properties, but fiber laser machines can typically handle a wide range of thicknesses for these materials as well.
What Are The Disadvantages Of Fiber Laser Cutting?
While laser cutting offers many advantages, such as high precision, speed, and versatility, it also has some disadvantages. Here are a few common drawbacks associated with laser cutting:
- High Initial Cost: Laser-cutting machines can be expensive to purchase and install, especially high-power fiber lasers. Additionally, the cost of maintenance, replacement parts, and consumables can add to the overall investment.
- Material Limitations: While laser cutting is highly effective for cutting metals and some non-metallic materials, it may not be suitable for all materials. Certain materials, such as reflective metals like copper and aluminum, can be challenging to cut with conventional laser systems due to their high reflectivity.
- Heat Affected Zone (HAZ): Laser cutting generates heat, which can result in a heat-affected zone (HAZ) along the edges of the cut. In some applications, this heat-affected zone may affect the material properties, such as hardness or microstructure, especially in heat-sensitive materials.
- Thickness Limitations: While fiber lasers can cut through relatively thick materials, there are practical limitations to the thickness of the material that can be cut efficiently. Thicker materials may require multiple passes or slower cutting speeds, which can reduce productivity and increase processing time.
- Operating Costs: Laser-cutting machines consume electricity, assist gases (such as oxygen, nitrogen, or air), and require regular maintenance to ensure optimal performance. These operating costs can add up over time, particularly in high-volume production environments.
- Safety Concerns: Laser cutting involves the use of high-powered lasers, which can pose safety risks if not operated correctly. Proper safety measures, including training, protective equipment, and machine guarding, can minimize the risk of accident or injury.
- Environmental Impact: The process of laser cutting may produce fumes, particulates, and potentially hazardous emissions, depending on the material being cut. Proper ventilation and filtration systems are necessary to mitigate environmental impact and ensure a safe working environment.
Do You Need Ventilation When Using A Fiber Laser Cutting Machine?
Yes, ventilation is typically required when using a fiber laser cutting machine. Laser-cutting processes, including those with fiber lasers, can produce fumes, gases, and particulates, especially when cutting certain materials such as metals and plastics. Proper ventilation eliminates these emissions from the cutting area, ensuring a safe and healthy working environment for operators and maintaining the integrity of the equipment.
Here are a few reasons why ventilation is necessary when using a fiber laser cutting machine:
- Fume Extraction: Laser cutting can produce fumes and smoke as the material is heated and vaporized by the laser beam. These fumes may contain hazardous substances, such as metal oxides or volatile organic compounds (VOCs), depending on the material being cut. Ventilation systems help capture and remove these fumes, preventing them from accumulating in the workspace and potentially posing health risks to operators.
- Particulate Removal: Laser cutting can also generate fine particulates or dust, especially when cutting materials like metals or composites. These particulates can pose respiratory hazards and may accumulate on surfaces, machinery, and equipment if not properly ventilated. Ventilation systems with appropriate filtration can help remove these particulates from the air, maintaining a cleaner and safer working environment.
- Temperature Regulation: In addition to removing fumes and particulates, ventilation systems can help regulate temperature and humidity levels in the cutting area. Effective ventilation can prevent overheating and ensure comfortable working conditions for operators, which is particularly important in enclosed or confined spaces.
- Equipment Protection: Proper ventilation can also help protect sensitive components of the laser cutting machine, such as optics, electronics, and cooling systems, from exposure to airborne contaminants. By reducing the accumulation of dust and debris within the machine, ventilation systems can help maintain optimal performance and prolong the lifespan of critical components.
ファイバーレーザー切断機はどのガスを使用していますか?
The gas used in fiber laser cutting machines depends on the material being cut and the specific cutting process. The most common gases used in laser cutting are:
- Oxygen (O2): Oxygen is commonly used when cutting ferrous metals such as mild steel and stainless steel. When the laser beam interacts with the metal surface in the presence of oxygen, it oxidizes the material, resulting in an exothermic reaction that helps facilitate the cutting process. Oxygen also helps to blow away molten metal and assist in the combustion process, improving cutting efficiency and edge quality.
- Nitrogen (N2): Nitrogen is often used as an assist gas when cutting non-ferrous metals such as aluminum, copper, brass, and titanium. Unlike oxygen, nitrogen does not react chemically with these metals. Instead, it serves primarily as a coolant and helps to prevent oxidation and discoloration of the cut edges. Nitrogen is also used for cutting materials where a clean, oxide-free surface is desired, such as in electronics or medical device manufacturing.
- Air: Compressed air can also be used as an assist gas in laser cutting. It can also be used as a low-cost alternative to nitrogen when cutting non-ferrous metals, although it may not provide the same level of edge quality or protection against oxidation.
How Long Is The Service Life Of a Fiber Laser Generator?
The service life of a fiber laser generator, like any other machine component, can vary depending on several factors, including:
- Quality of Components: The quality of the laser generator and its components significantly influences its service life. Higher-quality components, such as laser diodes, optical fibers, and resonator modules, tend to have longer lifespans and better reliability.
- Operating Conditions: The operating conditions in which the fiber laser generator is used can impact its service life. Factors such as temperature, humidity, vibration, and dust levels can affect the performance and longevity of the generator. Proper maintenance, including regular cleaning and inspection, can help prolong its service life.
- Maintenance Practices: Regular maintenance and upkeep help ensure optimal performance and longevity of your fiber laser generator. This includes cleaning optical components, checking for alignment issues, replacing worn parts, and monitoring key parameters such as laser power and beam quality.
- Duty Cycle: The duty cycle, or the ratio of the laser’s operating time to its cooldown time, can affect the generator’s service life. Operating the laser within its specified duty cycle limits helps prevent overheating and premature wear of components.
- Usage Patterns: The frequency and intensity of use also play a role in determining the service life of a fiber laser generator. Continuous operation at high power levels may lead to faster degradation of components compared to intermittent or lower-power usage.
レーザー ソリューションを入手する
お客様の要件に応じてデザインをカスタマイズできます。お客様の要件をお知らせいただくだけで、当社のエンジニアが最短時間でターンキー ソリューションを提供します。当社のレーザー機器の価格は非常に競争力があります。無料の見積もりについては、お問い合わせください。その他のレーザー機器関連のサービスが必要な場合は、お問い合わせください。