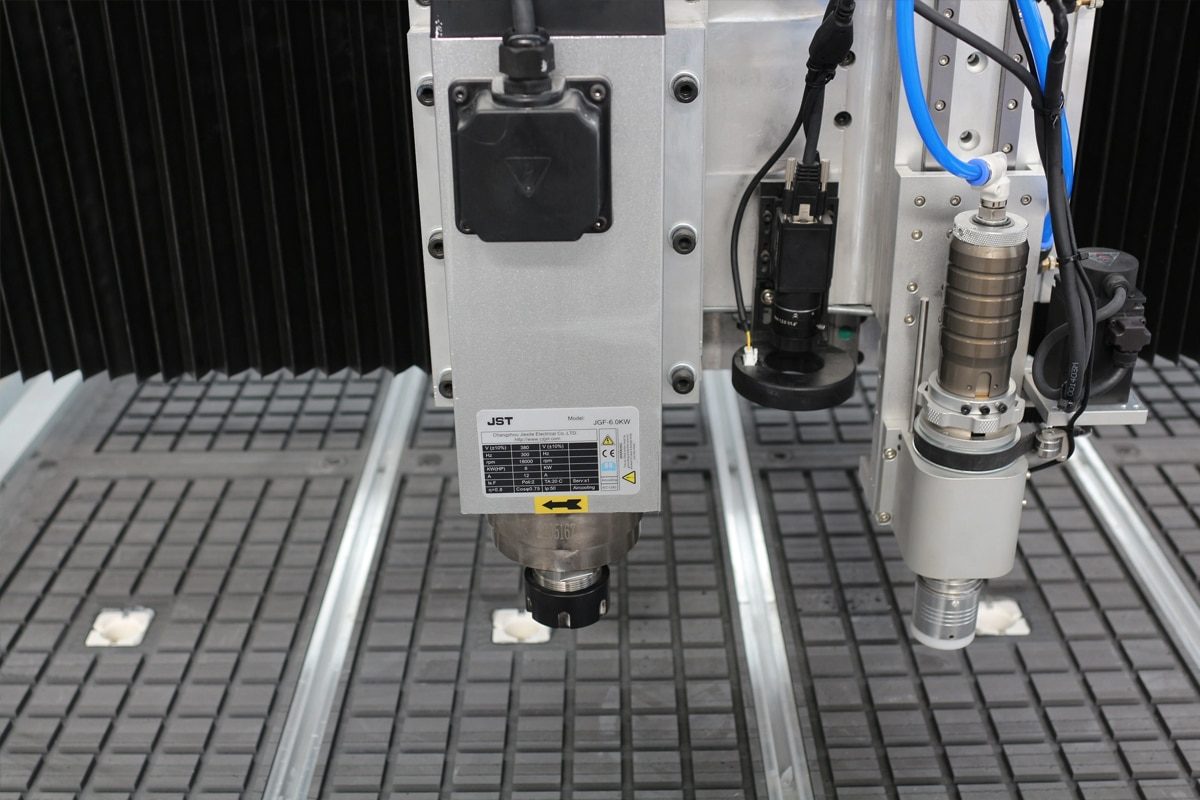
Brief History of Cutting Technologies
Early Cutting Tools
Industrial Revolution and Mechanization
Modern Cutting Techniques
Emergence of Oscillating Knife Cutting
Working Principle of Oscillating Knife Cutting
The Oscillatory Motion
Contact-Based Cutting
Role of the CNC and Vacuum Bed
Knife Tip Orientation
Core Components and Mechanics of Oscillating Knife Cutting
CNC Controller
Cutting Head
Vacuum Bed
Conveyor System (Optional)
Vision or Registration Systems
Software
Advantages and Disadvantages
Advantages
- Cold-Cutting Process: Oscillating knife cutting is a cold-cutting technology, meaning it does not generate heat during the cutting process. Unlike laser or plasma cutting, which can cause burn marks, warping, or material distortion, an oscillating knife cuts cleanly without thermal damage. This makes it ideal for cutting heat-sensitive materials such as foam, rubber, and textiles.
- High Precision and Clean Edges: Thanks to its high-frequency blade movement, oscillating knife cutting provides sharp, clean, and burr-free edges. It can handle intricate designs and complex patterns with exceptional accuracy, making it ideal for applications such as packaging, signage, furniture, and textiles.
- Material Versatility: Oscillating knife cutting is highly versatile and can handle a wide variety of materials, including foam, rubber, leather, fabrics, textiles, cardboard, paperboard, plastic sheets, and composite materials. This adaptability makes it a preferred cutting solution for industries such as automotive, furniture, footwear, apparel, and packaging.
- Reduced Waste and Cost Efficiency: The precision of oscillating knife cutting minimizes material waste, helping manufacturers reduce production costs. Additionally, the lack of heat damage eliminates the need for post-processing, further improving cost efficiency by reducing additional labor and material usage.
- User-Friendly and Safe: Unlike laser or plasma cutters, which generate fumes and require protective measures, oscillating knife-cutting machines are safe and easy to operate. They do not produce harmful emissions, making them an environmentally friendly and workplace-friendly option. The CNC automation in modern machines also simplifies operation, allowing users to input digital designs and let the machine handle the rest.
- Faster Prototyping and Changeovers: For businesses involved in rapid prototyping or frequent design modifications, oscillating knife cutting is a time-saving solution. The ability to quickly switch materials or modify cutting parameters without extensive reconfiguration allows manufacturers to accelerate production and adapt to changing demands effortlessly.
- Environmentally Friendly: Oscillating knife cutting is an eco-friendly cutting method because it does not involve burning, melting, or producing harmful byproducts. Additionally, its efficient material use reduces waste, contributing to sustainable manufacturing practices.
Disadvantages
- Blade Wear and Consumable Costs: Since the oscillating knife physically cuts through materials, blades experience wear over time and require frequent replacement. This can add to operational costs, especially when cutting abrasive or dense materials that dull the blade faster.
- Limited to Certain Thicknesses and Material Hardness: Oscillating knife cutting is best suited for soft to semi-rigid materials. It may struggle with very thick, dense, or hard materials such as metals, ceramics, or thick plastic sheets. For such applications, manufacturers may need to opt for laser, waterjet, or plasma cutting methods.
- Slower Speeds for Complex Shapes or Tough Materials: While oscillating knife cutting is efficient for straight and simple cuts, it can be slower for intricate patterns or when cutting through denser materials. The machine needs to adjust blade orientation frequently, which can reduce cutting speed compared to laser or waterjet cutting.
- Potential for Material Movement: Although vacuum beds help secure materials in place, lightweight or highly flexible materials (such as thin textiles) may still shift during cutting. This can result in misalignment and require manual adjustments, affecting precision.
- Noise and Vibration: The rapid oscillation of the knife creates vibration and noise, especially when cutting dense or thick materials. While modern machines are designed to reduce noise levels, it remains a factor to consider in industrial settings.
- Less Suitable for Some Edge Finishes: While oscillating knife cutting delivers clean edges, it may not be ideal for applications requiring sealed or polished edges, such as acrylic or glass. For these materials, laser cutting or polishing may be necessary to achieve the desired finish.
- Initial Investment Costs: High-quality CNC oscillating knife-cutting machines require a significant initial investment, particularly for advanced models with automated features. However, this cost is often offset by increased efficiency, reduced waste, and long-term operational savings.
Materials Suitable for Oscillating Knife Cutting
Foam and Sponge
Foam and sponge materials are commonly used in packaging, insulation, furniture, and automotive applications. Oscillating knife cutting ensures clean, precise cuts without compressing or distorting the material. Suitable foam types include:
- Polyurethane (PU) foam
- Polyethylene (PE) foam
- EVA (ethylene-vinyl acetate) foam
- Memory foam
- Acoustic and insulation foam
- Sponge rubber
Textiles and Leather
Industries such as fashion, automotive, upholstery, and footwear rely on oscillating knife cutting for its clean and precise ability to cut textiles and leather without fraying or distortion. It is suitable for:
- Natural fabrics (cotton, wool, linen)
- Synthetic fabrics (polyester, nylon, spandex)
- Technical textiles (Kevlar, carbon fiber fabrics)
- Leather and synthetic leather
- Non-woven fabrics
Rubber and Gaskets
Oscillating knife cutting is widely used in the automotive, industrial, and sealing industries for processing rubber-based materials and gaskets. It can accurately cut:
- Natural rubber
- Neoprene
- Silicone rubber
- EPDM rubber
- Cork-rubber composites
- Foam rubber sheets
Cardboard and Corrugated Board
The packaging and signage industries benefit significantly from oscillating knife cutting, especially for materials such as:
- Corrugated cardboard
- Solid fiberboard
- Honeycomb board
- Recycled paperboard
Plastics and Vinyl
Thin plastic sheets and vinyl materials can be effectively cut using an oscillating knife without melting or burning. It is ideal for:
- PVC (polyvinyl chloride)
- Polypropylene (PP) sheets
- Polycarbonate (PC)
- Acrylic sheets (thin variants)
- Vinyl films and decals
Paper and Card Stock
For printing, stationery, and craft industries, oscillating knife cutting provides detailed and intricate cuts on paper-based materials, including:
- Thick cardstock
- Paperboard and duplex board
- Stencil materials
Composites
Industries such as aerospace, automotive, and construction use oscillating knife cutting for lightweight composite materials that require non-thermal processing. Suitable composites include:
- Fiberglass sheets
- Carbon fiber fabrics
- Kevlar and aramid fiber composites
Other Materials
Oscillating knife cutting is also effective for a variety of other materials, including:
- Cork sheets (used in flooring and insulation)
- Felt and soft padding materials
- Rubber-backed carpets
- Insulation materials (acoustic and thermal insulation sheets)
Comparison with Other Cutting Methods
Oscillating Knife Cutting VS. Laser Cutting
Oscillating Knife Cutting VS. Waterjet Cutting
Oscillating Knife Cutting VS. Die Cutting
Oscillating Knife Cutting VS. CNC Routing
Each cutting method has unique advantages and ideal applications based on material type, precision requirements, and production scale.
- Oscillating knife cutting is ideal for soft, flexible materials and is favored in industries like packaging, textiles, and rubber manufacturing.
- Laser cutting is better for hard materials such as metal, acrylic, and wood, offering extreme precision but with heat-related limitations.
- Waterjet cutting is the best choice for thick, hard materials like glass, metal, and ceramics, though it is slower and more expensive to operate.
- Die cutting is highly efficient for high-volume production but lacks the flexibility of oscillating knife cutting for custom designs and prototyping.
- CNC routing is the go-to solution for wood, plastic, and aluminum, especially when 3D shaping or edge detailing is required.
Industries and Applications of Oscillating Knife Cutting
Packaging Industry
The packaging industry relies on oscillating knife cutting for custom packaging solutions, protective inserts, and display materials. It is widely used for:
- Corrugated cardboard and paperboard packaging for shipping and retail products
- Foam inserts for protective packaging in electronics and industrial goods
- Honeycomb board structures for lightweight and sustainable packaging
- Prototype packaging before large-scale production
Textiles and Apparel Industry
Oscillating knife cutting plays a crucial role in the textile and apparel industry, providing precise fabric cutting with minimal fraying or distortion. It is used for:
- Cutting patterns for clothing and accessories
- Automated cutting of fabric rolls for mass production
- Precision cutting of technical textiles like fire-resistant fabrics, carbon fiber textiles, and medical textiles
- Custom designs for embroidery and applique work
Leather Goods Industry
Leather is an expensive and delicate material, requiring precision cutting to maximize yield and maintain high-quality finishes. Oscillating knife cutting is used for:
- Handbags, wallets, and luxury accessories
- Footwear production, including leather soles and uppers
- Leather upholstery for furniture and automotive applications
- Customized leather engraving and pattern cutting
Signage and Graphics Industry
The advertising and signage industry depends on oscillating knife cutting for high-quality, custom designs in:
- Foam board, PVC, and acrylic signage
- Vinyl lettering and decals for vehicle wraps and branding
- Large-format promotional displays
- Custom-shaped stickers, labels, and point-of-sale materials
Automotive and Aerospace Industry
Oscillating knife cutting is widely used in the automotive and aerospace industries due to its ability to process flexible and composite materials with high precision. It is essential for:
- Cutting insulation materials for thermal and soundproofing applications
- Producing foam and rubber gaskets and seals
- Cutting leather and fabric upholstery for car and aircraft interiors
- Processing lightweight composite materials for high-performance vehicle components
Furniture and Upholstery Industry
The furniture industry uses oscillating knife cutting for precision cutting of upholstery materials, cushioning, and decorative elements. Key applications include:
- Foam cutting for mattresses, sofas, and chairs
- Leather and fabric upholstery for custom furniture
- Cutting decorative panels and patterns for modern furniture designs
- Processing insulation materials for ergonomic furniture production
Medical and Healthcare Industry
In the medical field, oscillating knife cutting plays a vital role in producing specialized materials for patient care, medical devices, and protective equipment. Applications include:
- Cutting foam for orthopedic supports, prosthetics, and braces
- Manufacturing precision-cut medical gaskets and seals
- Producing disposable face masks and protective clothing
- Creating sterile, custom-cut medical textiles for hospitals and surgical environments
Arts, Crafts, and Prototyping Industry
For artists, designers, and prototype developers, oscillating knife cutting provides precision and flexibility for creative projects. It is widely used for:
- Paper and cardboard cutting for artistic designs and sculpture
- Foam modeling for architecture and product design prototypes
- Custom stencil and template creation
- Crafting leather, textiles, and rubber-based decorative elements
Setting Up and Operating Oscillating Knife Cutting Machines
Pre-Installation Considerations
Before setting up an oscillating knife-cutting machine, it is essential to prepare the workspace, check power and air supply requirements, and ensure material handling efficiency. Key factors to consider include:
- Workspace Setup: The machine should be installed in a stable, vibration-free environment with sufficient space for loading and unloading materials. A clean, dust-free area ensures smooth operation.
- Power Supply: Verify the electrical requirements of the machine (e.g., voltage and phase) and ensure a stable power connection to prevent fluctuations that could affect performance.
- Air Supply (If Required): Some machines use compressed air for vacuum beds or tool actuation, so an appropriate air supply system should be installed.
- Material Handling: If using large sheets or rolls, plan for proper storage and handling equipment. A conveyor system or vacuum bed can help secure materials during cutting.
- Safety Measures: Ensure emergency stop switches, protective guards, and operator safety protocols are in place before operating the machine.
Software Integration
Oscillating knife-cutting machines operate using CNC (Computer Numerical Control) systems that require compatible software for design input and machine control. The software integration process includes:
- Installing the Control Software: Most machines come with proprietary CNC software that must be installed on a connected computer.
- Importing Design Files: The machine typically supports file formats such as DXF, AI, PLT, and SVG, allowing seamless import of CAD and vector-based designs.
- Configuring Cutting Parameters: Operators need to adjust cutting depth, oscillation frequency, feed rate, and blade pressure based on the material type and thickness.
- Nesting and Optimization: Advanced software includes automatic nesting features that arrange cut patterns to maximize material usage and reduce waste.
- Simulation and Preview: Some software solutions provide cut path previews and simulations to help detect potential errors before actual cutting.
Tooling and Blade Selection
Selecting the right blade and tooling setup is critical to achieving clean cuts and prolonging blade life. Factors to consider include:
- Material Type:
- Soft materials (foam, textiles) require high-speed oscillating blades.
- Dense materials (rubber, thick plastics) require reinforced carbide blades for durability.
- Blade Shape and Type:
- Straight blades: Ideal for general-purpose cutting.
- Rotary blades: Best for fabric, leather, and textiles to avoid pulling fibers.
- V-cut blades: Used for angled cuts in corrugated materials.
- Blade Maintenance:
- Regular blade replacement is required to maintain cutting precision.
- Using the correct blade reduces material fraying and tool wear, improving efficiency.
Machine Operation Workflow
Once the machine is set up and software parameters are configured, the actual cutting process follows a structured workflow:
- Material Preparation and Loading: Secure the material onto the vacuum bed or conveyor system to prevent shifting during cutting.
- File Selection and Import: Load the digital cutting file into the software, ensuring proper alignment and orientation.
- Calibration and Test Cut: Perform a test run on scrap material to verify the cutting depth, blade pressure, and speed settings.
- Start the Cutting Process: Initiate the cutting operation while monitoring for any blade inconsistencies or material movement.
- Quality Inspection: Check the final cut for precision, edge smoothness, and alignment. Adjust settings if needed.
- Material Removal and Cleaning: Carefully remove the finished pieces and clean the machine bed to prepare for the next operation.
Operator Skills and Training
Even with automation, skilled operators are essential for maintaining machine performance and troubleshooting potential issues. Operators should be trained in:
- Basic Machine Setup and Maintenance: Understanding machine calibration, cleaning, and routine maintenance to extend machine life.
- Software Navigation: Training on importing files, setting parameters, and using nesting features for optimized cutting.
- Blade Handling and Replacement: Learning how to select, install, and replace blades safely and efficiently.
- Material Selection and Handling: Understanding different materials and their cutting behaviors to adjust machine settings accordingly.
- Safety Procedures: Following safety guidelines, emergency stop functions, and protective equipment requirements.
Maintenance and Troubleshooting
Regular Inspection
Blade Condition
- Inspect for dullness, chipping, or excessive wear. A worn-out blade can lead to poor cut quality, frayed edges, and increased strain on the machine.
- Replace blades at the first sign of reduced sharpness to maintain high-quality cuts.
Vacuum Bed and Material Hold-Down System
- Ensure adequate suction to prevent material shifting during cutting.
- Clean the vacuum bed and air channels to avoid clogs that could reduce suction efficiency.
CNC Software and Control System
- Check if the software is running smoothly and update it as necessary.
- Ensure machine calibration settings are correct for maintaining precise cuts.
Blade Holder and Cutting Mechanism
- Inspect for loose screws or misalignment in the blade holder and tool assembly.
- Ensure the blade is securely fastened to avoid excessive vibration.
Dust and Debris Removal
- Regularly clean cutting debris, foam particles, and dust from the machine bed and tool area.
- A clean machine ensures smooth operation and prevents mechanical wear.
Common Troubleshooting Scenarios
Inconsistent Cutting Depth
Possible Causes:
- Dull or improperly installed blade.
- Incorrect cutting pressure or depth settings.
- Material not held down securely.
Solutions:
- Replace or re-sharpen the blade if it is dull.
- Adjust cutting pressure and oscillation frequency in the CNC software.
- Verify vacuum suction strength and apply weights or adhesives if needed.
Frayed or Rough Cut Edges
Possible Causes:
- The blade is dull or unsuitable for the material.
- Cutting speed is too high, leading to tearing instead of clean cuts.
- Material shifting during cutting.
Solutions:
- Select a proper blade type for the material.
- Reduce cutting speed and oscillation frequency.
- Ensure proper material stabilization using vacuum or clamping methods.
Machine Not Responding to Commands
Possible Causes:
- Connection issue between CNC software and the machine.
- Loose or disconnected power cables.
- Overheated motor or electrical failure.
Solutions:
- Restart the CNC software and check communication settings.
- Inspect cable connections and ensure the power supply is stable.
- Allow the machine to cool down before restarting if overheating occurs.
Excessive Blade Vibration or Noise
Possible Causes:
- The blade holder is loose or not properly aligned.
- The blade is damaged or incorrectly installed.
- The cutting bed or machine surface is not level.
Solutions:
- Tighten the blade holder and all mounting screws.
- Replace any damaged or misaligned blades.
- Ensure the cutting bed is level and properly secured.
Material Slipping or Misalignment
Possible Causes:
- Vacuum suction is weak or air channels are clogged.
- The material is too lightweight and moves with airflow.
Solutions:
- Clean the vacuum bed and air channels for better suction.
- Use adhesive backing or weights to secure lightweight materials.
Preventive Maintenance Schedule
Daily Maintenance
- Inspect the blade for wear and replace if necessary.
- Check for material buildup or dust in the blade housing and machine bed.
- Verify the vacuum bed and suction system for proper material hold-down.
- Ensure software settings are correctly calibrated before production.
Weekly Maintenance
- Lubricate moving parts such as guide rails and bearings, if required.
- Inspect the blade holder and tool assembly for any loose components.
- Clean and check air filters, suction nozzles, and dust extraction systems.
- Perform a test cut on different materials to verify machine accuracy.
Monthly Maintenance
- Check for loose electrical connections and power fluctuations.
- Inspect motor belts, drive gears, and transmission parts for signs of wear.
- Update CNC software and firmware if updates are available.
- Clean the control panel and display screen to ensure proper touch response.
Quarterly or Biannual Maintenance
- Conduct a full deep cleaning of the entire machine.
- Inspect the main drive system, bearings, and motor alignment.
- Perform a detailed precision test to check cutting accuracy.
- Replace any worn-out belts, screws, or major components if needed.