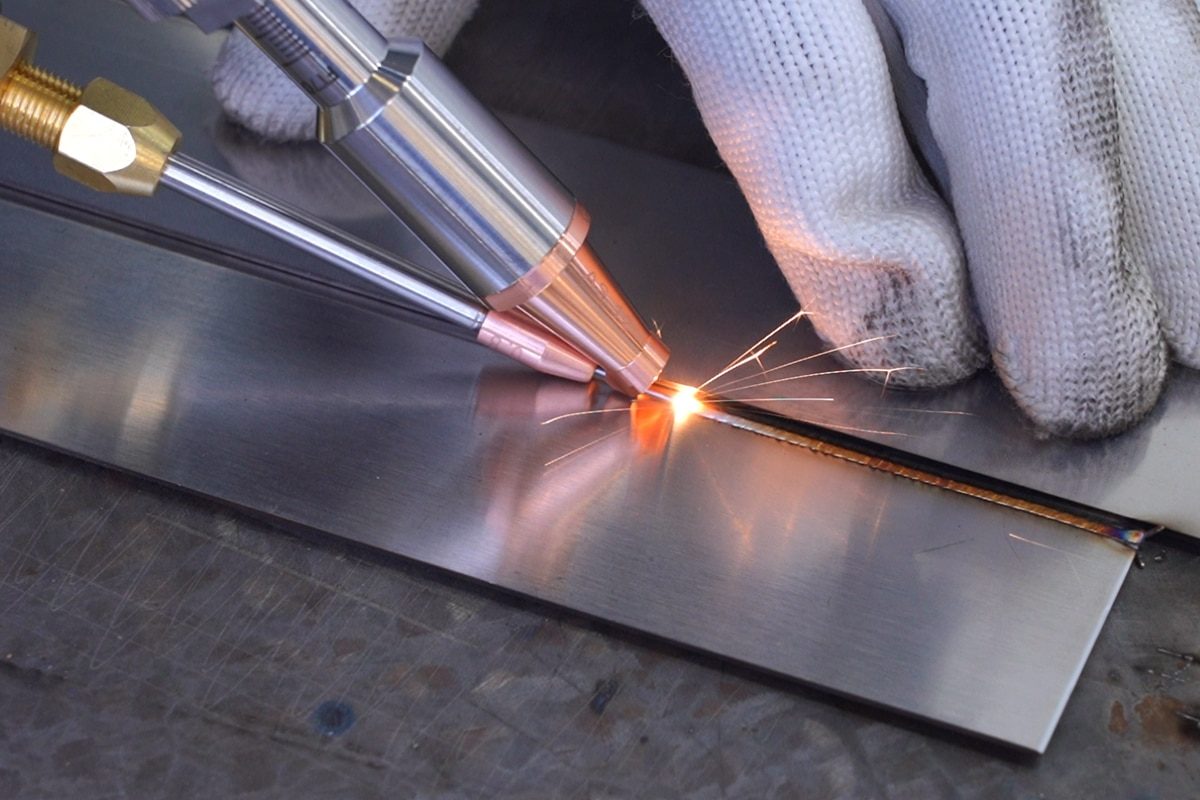
Historical Overview of Laser Welding
Early Laser Inventions
Initial Experiments in Laser Welding
Modern-Day Progress
Fundamentals of Laser Welding
What is a Laser?
A laser (Light Amplification by Stimulated Emission of Radiation) is a device that generates a highly focused and intense beam of light through the process of stimulated emission. Unlike ordinary light, laser beams are:
- Monochromatic: Consisting of a single wavelength.
- Coherent: Light waves move in phase, maintaining focus over long distances.
- Directional: The beam remains highly concentrated, allowing precise energy delivery.
Different types of lasers are used in welding applications, including:
- CO2 Lasers: High-power gas lasers used for industrial welding of metals and non-metals.
- Nd: YAG (Neodymium-doped Yttrium Aluminum Garnet) Lasers: Suitable for precision welding, commonly used in aerospace and medical industries.
- Fiber Lasers: Energy-efficient and highly reliable, fiber lasers provide excellent beam quality and are widely used in modern industrial applications.
- Diode Lasers: Compact and efficient, used for lower-power welding applications.
Laser Welding Basics
Laser welding works by focusing a high-energy laser beam onto the workpiece, generating intense heat that melts and fuses materials. This process can be performed in two primary modes:
- Conduction Mode Welding: The laser energy is absorbed by the surface, generating heat that spreads through conduction. This mode is ideal for shallow welds and thin materials.
- Keyhole Welding: A high-powered laser beam creates a deep, narrow hole (keyhole) by vaporizing material, allowing for deeper penetration welds. This method is used for thick materials and high-strength applications.
Laser welding can also be performed using pulsed or continuous-wave (CW) lasers:
- Pulsed Laser Welding: Uses controlled pulses of laser energy to weld thin and delicate components with minimal heat input.
- Continuous Wave (CW) Laser Welding: Maintains a constant laser beam, enabling deep penetration and high-speed welding in industrial applications.
Key Laser Welding Parameters
Several critical parameters influence the quality and efficiency of laser welding:
- Laser Power: Determines the amount of energy delivered to the material. Higher power enables deeper welds and faster processing speeds.
- Beam Focus and Spot Size: A tightly focused beam provides precise energy delivery, while a larger spot size distributes heat over a wider area.
- Welding Speed: Affects penetration depth and weld quality. Faster speeds reduce heat input but may lead to incomplete fusion.
- Pulse Duration (for pulsed lasers): Controls how long the laser energy is applied, affecting weld penetration and heat distribution.
- Shielding Gas: Gases like argon, helium, or nitrogen protect the weld area from oxidation and contamination.
- Material Properties: The thermal conductivity, reflectivity, and composition of the material determine how it absorbs laser energy and melts.
Major Components of Laser Welding Machines
Laser Source
The laser source is the core component of the welding machine, generating a highly focused beam of light that is used for welding. Different types of laser sources are used depending on the application and material being welded:
- Fiber Laser Sources: Highly efficient, energy-saving, and widely used in industrial welding due to their excellent beam quality and low maintenance requirements.
- CO2 Laser Sources: Gas lasers provide high power and are commonly used for welding thick materials, though they are less common in modern applications.
- Nd: YAG Laser Sources: Solid-state lasers that provide high precision, commonly used in aerospace, medical, and fine metalworking applications.
- Diode Laser Sources: Compact and cost-effective lasers used for lower-power welding applications.
Beam Delivery Optics
The beam delivery optics direct and shape the laser beam from the source to the welding area. These optics ensure that the laser energy is efficiently transmitted while maintaining beam quality. Key components include:
- Fiber Optic Cables: Used in fiber laser systems to deliver the beam with minimal energy loss.
- Mirrors and Lenses: Used in CO2 laser welding systems to reflect and focus the laser beam onto the workpiece.
- Collimators and Beam Expanders: Ensure proper beam alignment and focus before reaching the welding head.
Workstation/Manipulator
The workstation or manipulator holds and positions the workpiece during the welding process. Depending on the complexity and automation level of the welding system, this component may include:
- Fixed Worktables: Used for manual or semi-automated welding setups.
- CNC (Computer Numerical Control) Systems: Provide programmable control over the movement of the workpiece or laser head for high-precision welding.
- Robotic Arms: Used in industrial and automated production lines for flexible and high-speed welding of complex geometries.
Welding Head
The welding head is responsible for focusing and directing the laser beam onto the workpiece. It consists of several key components:
- Focusing Lenses: Concentrate the laser beam to achieve precise weld penetration.
- Protective Glass: Shields the internal optics from spatter and debris during welding.
- Wire Feed Mechanism (if applicable): Used in applications where filler material is required to strengthen the weld.
Cooling System
Since laser welding generates intense heat, an efficient cooling system is essential to maintain the stable operation of the laser source and other components. Cooling systems typically include:
- Water Cooling Units: Circulate coolant through the laser source and optics to prevent overheating.
- Air Cooling Systems: Used in lower-power welding applications for simpler heat dissipation.
Shielding Gas Delivery
Shielding gas is used in laser welding to protect the weld pool from oxidation and contamination, ensuring clean and high-quality welds. Common shielding gases include:
- Argon: Provides excellent shielding for most metals and is widely used in laser welding.
- Helium: Used for deeper penetration welding, especially in high-strength applications.
- Nitrogen: Suitable for welding stainless steel and other specific materials that require controlled atmospheric conditions.
Control System
The control system is responsible for managing all aspects of the laser welding process, ensuring precision and repeatability. It includes:
- Software Interface: Allows operators to set welding parameters such as laser power, welding speed, and pulse duration.
- Real-Time Monitoring Sensors: Provide feedback on weld quality, temperature, and beam stability.
- Automation Integration: Enables robotic and CNC-controlled welding for high-precision and high-speed production.
Materials Commonly Welded with Lasers
Carbon Steels
Carbon steels are widely used in manufacturing due to their strength, durability, and affordability. Laser welding is highly effective for carbon steels, offering advantages such as:
- Deep penetration welds with minimal heat-affected zones (HAZ).
- High welding speeds, improving productivity.
- Reduced distortion and warping, compared to traditional welding methods.
Stainless Steels
Stainless steels are essential in industries that require corrosion resistance, strength, and aesthetics, such as medical, food processing, and aerospace. Laser welding offers key benefits for stainless steel, including:
- Strong, corrosion-resistant welds that maintain material integrity.
- Minimal heat input, reducing the risk of warping.
- Precise, clean welds with little to no post-processing required.
Aluminum and Aluminum Alloys
Aluminum and its alloys pose some challenges in laser welding due to their high reflectivity and thermal conductivity, which can result in inconsistent energy absorption. However, fiber lasers and pulsed laser welding have significantly improved the process. Key benefits include:
- Fast and deep penetration welding with minimal distortion.
- High mechanical strength of welded joints.
- Better control of porosity and cracking, which can occur due to aluminum’s low melting point.
Titanium and Titanium Alloys
Titanium is widely used in aerospace, medical implants, and high-performance engineering due to its high strength-to-weight ratio, corrosion resistance, and biocompatibility. Laser welding provides several advantages, such as:
- Strong, lightweight welds with high fatigue resistance.
- Minimal contamination due to precise shielding gas control.
- No need for filler materials in many cases.
Nickel Alloys
Nickel-based alloys, such as Inconel, Hastelloy, and Monel, are known for their high strength, corrosion resistance, and ability to withstand extreme temperatures. These properties make them essential in industries such as power generation, chemical processing, and aerospace. Laser welding offers key benefits, including:
- Precise heat control, reducing distortion and cracking.
- High-strength, durable welds for demanding applications.
- Resistance to carbide precipitation, ensuring long-term performance.
Precious Metals (Gold, Silver, Platinum)
Laser welding is extensively used in the jewelry, electronics, and medical industries for welding gold, silver, platinum, and palladium. These metals are challenging to weld using traditional methods due to their high thermal conductivity and sensitivity to heat. Laser welding provides:
- Precise, clean welds with minimal heat impact.
- Minimal material loss, which is crucial for expensive metals.
- Strong and aesthetically pleasing joints with no need for additional finishing.
Advantages and Disadvantages of Laser Welding
Advantages of Laser Welding
Precision and Control
Laser welding delivers exceptional accuracy, making it ideal for applications requiring fine, intricate welds.
- The laser beam can be precisely controlled, ensuring minimal heat impact on surrounding areas.
- It is capable of welding delicate, small components in electronics and medical devices.
- Ensures high repeatability with consistent, defect-free welds.
Speed
Laser welding is significantly faster than conventional welding techniques, leading to:
- Increased production efficiency with reduced processing time.
- Higher throughput in industrial settings, improving overall productivity.
- Minimal need for post-processing, such as grinding or polishing, due to clean welds.
Deep Penetration
With its high energy density, laser welding can achieve:
- Deep, strong welds with minimal material distortion.
- The ability to weld thick materials in a single pass improves efficiency.
- Narrow and concentrated heat-affected zones, maintaining material integrity.
Automation
Laser welding can be fully automated, making it ideal for mass production.
- Can be integrated with CNC machines and robotic systems for precision manufacturing.
- Consistent, high-quality welds reduce human error and defects.
- Reduces the reliance on skilled welders, lowering labor costs.
Low Distortion
Unlike traditional welding methods that introduce significant heat into the material, laser welding:
- Produces minimal heat-affected zones (HAZ), reducing warping and stress.
- Is suitable for thin materials and delicate components.
- Preserve the mechanical and aesthetic properties of the material.
Cleaner Process
Laser welding is a non-contact process, eliminating the need for consumables like electrodes or filler materials.
- Minimal spatter and contamination, ensuring high-quality welds.
- Environmentally friendly, as it produces fewer emissions and waste.
- Reduces the need for chemical cleaning and extensive finishing work.
Versatility
Laser welding is suitable for a wide range of materials, including:
- Metals like steel, aluminum, titanium, and nickel alloys.
- Dissimilar materials, such as metal-to-plastic welding in specialized applications.
- Thin or thick sections, making it useful for both precision micro-welding and heavy-duty industrial welding.
Disadvantages of Laser Welding
High Initial Investment
One of the main barriers to adopting laser welding is the high cost of equipment.
- Laser welding machines are more expensive than traditional welding systems.
- Maintenance and spare parts can be costly.
- Small businesses may find capital investment challenging, especially for high-power laser systems.
Reflective Materials
Certain metals, such as aluminum, copper, and gold, have high reflectivity, making them more difficult to weld.
- A significant amount of laser energy is reflected instead of being absorbed.
- Specialized high-power lasers and beam modulation techniques are required to improve welding efficiency.
Joint Fit-Up
Laser welding requires precise joint alignment for optimal results.
- Poor joint preparation can lead to incomplete fusion or porosity.
- Gaps between materials can reduce weld strength and may require filler material.
- Additional clamping or pre-weld preparation is often necessary to ensure a proper fit.
Safety Requirements
Due to the high-energy laser beams used in welding, strict safety precautions must be followed.
- Operators must wear protective eyewear to prevent laser-related eye injuries.
- Safety enclosures and interlocks are needed to protect workers from laser exposure.
- Training is required to handle high-power laser equipment safely.
Metallurgical Issues
Certain materials can experience undesirable metallurgical effects due to the high-energy input of laser welding.
- Cracking or porosity can occur in metals with high thermal expansion.
- Heat-affected zones (HAZ) may alter the mechanical properties of the material.
- Some alloys require preheating or post-weld heat treatment to maintain weld integrity.
Health and Safety Considerations in Laser Welding
Laser Enclosure
A laser enclosure is one of the most critical safety features in laser welding systems. It serves as a protective barrier to prevent accidental exposure to laser radiation.
- Enclosures are designed to fully contain the laser beam, ensuring that no stray radiation escapes.
- They protect operators and other personnel from direct or reflected laser beams, which can cause severe injuries.
- Many automated laser welding systems come with fully enclosed workstations, making them safer for industrial applications.
Protective Eyewear
Since laser beams can cause severe eye damage, including permanent vision loss, wearing laser-specific protective eyewear is mandatory.
- Laser safety glasses or goggles are designed to filter out the specific wavelength of the laser being used.
- The eyewear must be rated according to the Optical Density (OD) level required for the laser’s power and wavelength.
- Even when using an enclosed laser system, operators and nearby workers should wear appropriate eye protection to prevent exposure to reflected beams.
Ventilation
Laser welding can generate harmful fumes, gases, and particulates, especially when welding metals with coatings, alloys, or hazardous elements.
- Proper ventilation systems are required to remove toxic fumes and maintain clean air in the workspace.
- Fume extraction systems (fume hoods, exhaust fans, or HEPA filters) should be installed near the welding area.
- In industrial environments, dedicated ventilation ducts help prevent the accumulation of hazardous airborne contaminants.
Personnel Training
To ensure safe and efficient operation, all personnel working with laser welding machines must undergo proper training.
- Operators should be educated on laser safety procedures, emergency shutdown protocols, and personal protective equipment (PPE) requirements.
- Training programs should include safe handling of laser equipment, hazard identification, and risk assessment.
- Certified laser safety officers (LSOs) should oversee operations in workplaces with high-power laser systems.
Interlocks and Sensors
Laser welding machines are equipped with safety interlocks and sensors to prevent accidental exposure to the laser beam.
- Interlocks disable the laser beam if the enclosure or workstation door is opened.
- Sensors monitor beam alignment, temperature, and power levels, ensuring stable and safe operation.
- Emergency stop buttons should be easily accessible, allowing for immediate shutdown in case of malfunction.
Applications of Laser Welding
Automotive Industry
Laser welding is widely used in the automotive sector due to its speed, precision, and ability to join various metals with minimal heat impact.
- Body-in-white (BIW) assembly: Used to weld car body structures, improving strength while reducing weight.
- Battery welding for electric vehicles (EVs): Essential for connecting battery cells, terminals, and busbars in EV manufacturing.
- Exhaust systems, transmission components, and fuel injectors: Ensures durable, corrosion-resistant welds in complex parts.
- Weight reduction: Helps manufacturers use thinner and lighter materials without compromising strength.
Aerospace and Defense
In aerospace and military applications, laser welding is valued for its precision and ability to join high-strength materials used in extreme environments.
- Turbine components: Used to join nickel-based alloys and titanium parts in jet engines.
- Aircraft structures: Enables the welding of lightweight aluminum and titanium alloys, reducing aircraft weight.
- Fuel tanks and hydraulic systems: Ensures leak-proof and high-strength joints.
- Military equipment and weaponry: Provides robust and durable welds for defense-grade materials.
Medical Devices
The medical industry relies on laser welding to create highly precise and sterile components for life-saving devices and implants.
- Surgical instruments: Stainless steel and titanium components are welded with extreme precision.
- Implants (pacemakers, orthopedic implants, dental devices): Laser welding provides seamless, biocompatible joints.
- Catheters and guidewires: Ensures clean, non-contaminated welds required for medical applications.
- Endoscopic and laparoscopic instruments: Enables the production of miniature, high-strength medical tools.
Electronics and Microelectronics
Laser welding is essential in electronics manufacturing, where small, delicate components require low-heat, high-precision welding.
- Circuit boards and connectors: Laser welding creates precise and reliable micro-welds for electronic assemblies.
- Semiconductors and sensors: Provides durable, high-purity connections in miniature electronic devices.
- Battery and power storage devices: Used in lithium-ion battery manufacturing for high-performance electronics and EVs.
- Smartphone and wearable technology components: Allows for compact, high-quality joints in consumer electronics.
Jewelry and Watchmaking
The luxury industry benefits from laser welding’s ability to join precious metals with high accuracy and minimal material loss.
- Gold, silver, and platinum welding: Ensures seamless, high-quality joints with minimal heat damage.
- Watch components: Used for precision welding of tiny, intricate parts in high-end watches.
- Jewelry repair and resizing: Enables damage-free repairs, maintaining the integrity of valuable pieces.
- Custom jewelry design: Allows for fine, decorative welding without affecting surrounding areas.
General Manufacturing
Laser welding is widely used in industrial and general manufacturing, offering high-speed, automated solutions for large-scale production.
- Steel and aluminum fabrications: Used in construction, industrial machinery, and heavy equipment.
- Pipelines and pressure vessels: Ensures strong, corrosion-resistant welds for oil, gas, and chemical processing industries.
- Household appliances: Welds stainless steel components in refrigerators, ovens, and washing machines.
- Precision tools and molds: Helps in repairing and fabricating intricate mold parts.
Choosing the Right Laser Welding System
Material and Thickness
The type and thickness of the material being welded determine the laser power, wavelength, and welding mode required.
- Thin materials (e.g., stainless steel, titanium, aluminum sheets) require low to medium-power lasers to avoid excessive heat input and warping.
- Thick materials (e.g., carbon steel, and nickel alloys) need high-power lasers to achieve deep penetration.
- Reflective materials (e.g., aluminum, copper, gold) require specialized fiber lasers or high-power pulse settings to enhance energy absorption.
Production Volume
The expected welding output influences whether a manual, semi-automated, or fully automated system is required.
- Low-volume, custom welding: A handheld or semi-automatic laser welding machine is suitable for prototyping and specialized applications.
- High-volume manufacturing: A fully automated CNC or robotic laser welding system is ideal for mass production, ensuring consistency, speed, and minimal human intervention.
- Batch vs. continuous production: Systems with integrated conveyors, multi-axis workstations, or robotic arms can enhance productivity in continuous manufacturing environments.
Budget and ROI (Return on Investment)
While laser welding machines require a higher initial investment than traditional welding equipment, they offer long-term cost savings through:
- Lower operational costs (no consumables like electrodes or filler materials).
- Reduced labor costs due to automation and faster welding speeds.
- Minimal rework and finishing, improving production efficiency.
Machine Footprint
The available workspace and factory layout should align with the chosen laser welding machine’s size and configuration.
- Compact desktop laser welding machines: Suitable for jewelry, medical devices, and small components where space is limited.
- Standalone or benchtop models: Ideal for medium-sized operations that require flexibility.
- Industrial robotic laser welding systems: Require dedicated space, suitable for automotive and aerospace production lines.
Versatility and Upgradability
As production demands evolve, businesses should consider scalability and compatibility with future requirements.
- Multi-purpose welding systems: Machines that support multiple welding modes (conduction, keyhole, hybrid welding) offer greater flexibility.
- Software and automation integration: Choosing a system with programmable controls, AI-assisted welding, and CNC/robotic compatibility ensures future upgradability.
- Modular upgrades: Some machines allow power upgrades, additional axis controls, or enhanced optics, making them adaptable for expanding production needs.
Process Optimization and Quality Control in Laser Welding
Parameter Trials
Before starting full-scale production, conducting parameter trials is essential to determine the optimal laser settings for specific materials and applications. The most critical parameters include:
- Laser Power: Adjusting power levels ensures the correct penetration depth and heat input.
- Welding Speed: Faster speeds minimize heat-affected zones (HAZ), while slower speeds enhance fusion.
- Focus Position and Beam Spot Size: Proper focusing improves energy efficiency and weld precision.
- Shielding Gas Type and Flow Rate: Prevents oxidation, improves weld bead quality, and enhances joint strength.
Real-Time Monitoring
Real-time monitoring technologies help detect inconsistencies and defects during the welding process, reducing waste and improving production efficiency.
- Optical Sensors and Cameras: Capture high-speed images to track weld pool stability and detect undercuts, cracks, or gaps.
- Thermal Sensors and Infrared Imaging: Monitor heat distribution and prevent overheating or excessive thermal expansion.
- Back-Reflection Monitoring: Helps detect misalignment, material inconsistencies, and power fluctuations.
Nondestructive Testing (NDT)
To ensure structural integrity without damaging the weld, Nondestructive Testing (NDT) methods are used to inspect and verify weld quality. Common NDT techniques include:
- Ultrasonic Testing (UT): Uses sound waves to detect internal defects such as voids and cracks.
- X-ray and Radiographic Inspection: Identifies hidden flaws, porosity, or incomplete fusion in welded joints.
- Laser Profilometry: Scans the weld bead geometry for inconsistencies or surface irregularities.
- Eddy Current Testing (ECT): Detects subsurface cracks and inclusions in conductive materials.
Metallurgical Analysis
A metallurgical examination of the welded joint provides insights into microstructure, hardness, and chemical composition, ensuring that the weld meets performance expectations.
- Microstructure Analysis (SEM or Optical Microscopy): Identifies grain structure and phase transformations in the weld and heat-affected zone (HAZ).
- Hardness Testing (Vickers, Rockwell, or Brinell): Confirms weld strength and resistance to wear and fatigue.
- Chemical Composition Analysis: Verifies that the material properties remain unchanged after welding, ensuring corrosion resistance and mechanical performance.
Closed-Loop Control
Closed-loop control systems continuously monitor and adjust welding parameters in real-time, ensuring consistent weld quality.
- Automated Sensors and Feedback Mechanisms: Measure weld depth, power levels, and thermal input.
- AI and Machine Learning Integration: Predict potential weld defects and adjust settings accordingly.
- Self-Correcting Laser Systems: Modify beam intensity, focus, and speed based on real-time data to maintain precision.
Comparing Laser Welding to Other Welding Methods
Laser Welding VS. TIG Welding
Laser Welding VS. MIG/MAG Welding
Laser Welding VS. Electron Beam Welding
Laser Welding VS. Plasma Arc Welding
Each welding method has its strengths and is suited for specific applications. However, laser welding stands out as the most advanced option, offering:
- Faster processing speeds compared to TIG, MIG, EBW, and PAW.
- Higher precision with minimal spatter and post-processing.
- Lower heat input, reducing distortion and material damage.
- Seamless automation integration makes it ideal for modern manufacturing.