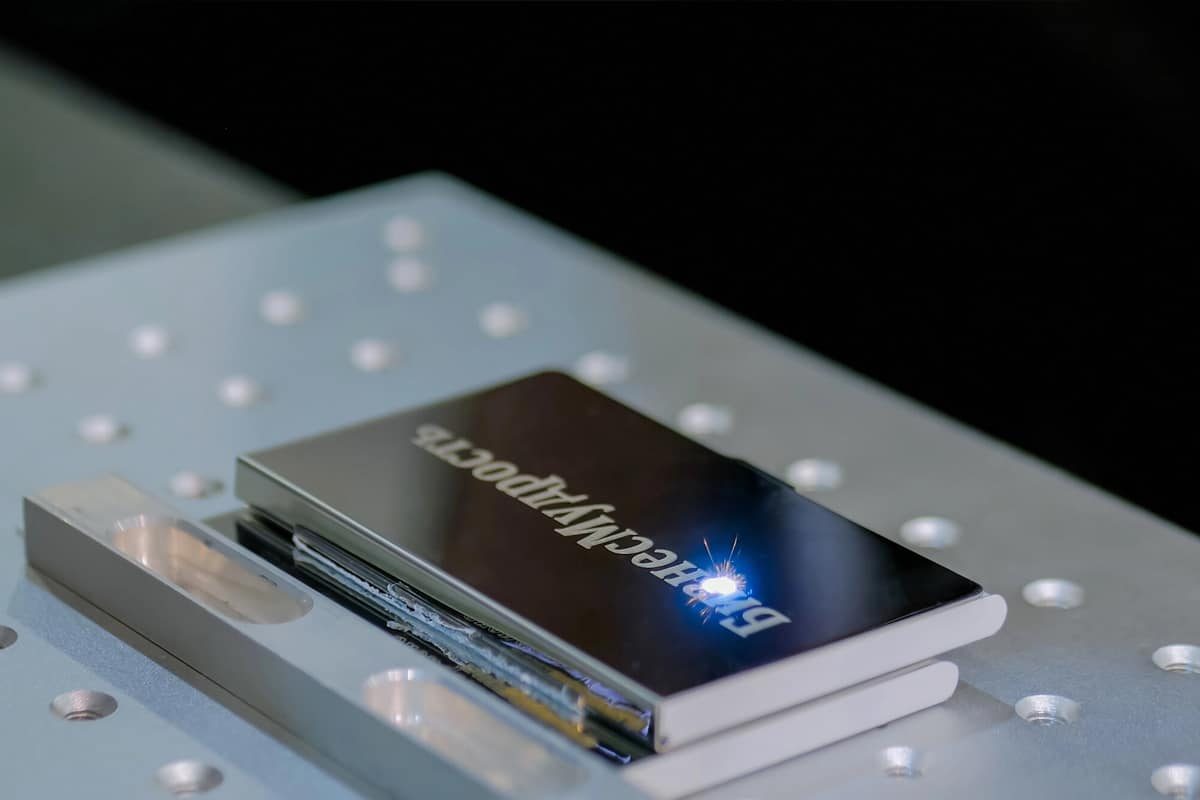
Historical Context of Laser Marking
The Fundamentals of Laser Technology
Basic Principles
Key Laser Parameters
Several factors influence the effectiveness and quality of laser marking:
- Wavelength: Different laser wavelengths interact differently with materials. For example, fiber lasers (1064 nm) are ideal for metals, while CO2 lasers (10.6 μm) work well with organic materials.
- Power Output: Determines the depth and speed of marking. Higher power allows for deeper engraving but may generate excess heat.
- Pulse Duration: Affects the precision and material interaction. Shorter pulses (picosecond and femtosecond lasers) provide ultra-fine marking without excessive heat.
- Repetition Rate: The number of laser pulses per second, impacting the speed and resolution of the marking.
- Beam Quality (M2 Factor): A measure of the laser beam’s focusability, influencing marking precision and efficiency.
Major Laser Types Used in Marking
- Uses a fiber-optic cable to amplify laser energy.
- Ideal for marking metals, plastics, and some ceramics.
- Known for high-speed processing, durability, and energy efficiency.
- Common in industries like aerospace, automotive, and medical device manufacturing.
- Utilizes a gas mixture (carbon dioxide) as the laser medium.
- Best for organic materials like wood, leather, glass, paper, and certain plastics.
- Frequently used in packaging, engraving, and artistic applications.
- Operates at a short wavelength (355 nm) for ultra-precise marking.
- Suitable for delicate materials such as glass, plastics, and circuit boards.
- Produces minimal heat, reducing damage to sensitive components.
Green Laser Marking:
- Works at a wavelength of 532 nm, ideal for reflective materials.
- Used for marking metals, plastics, and semiconductors with high contrast.
- Preferred for applications requiring minimal heat-affected zones.
Laser Marking System Components
Laser Source:
- The core of the marking system generates the laser beam.
- The type of laser (fiber, CO2, UV, or green) determines marking suitability.
Scan Head (Galvanometer):
- Uses high-speed mirrors to direct and control the laser beam’s movement.
- Enables precise and rapid marking over the workpiece.
F-Theta Lens:
- A specialized lens that ensures uniform marking over a flat field.
- Determines the marking area size and affects beam focus.
Control Electronics and Software:
- Manages the laser settings, marking patterns, and automation features.
- Provides user interfaces for design input, marking parameters, and job execution.
Work Area or Fixture:
- The platform where the material to be marked is placed.
- Fixtures ensure accurate positioning and repeatability for mass production.
Cooling System:
- Regulates the temperature of the laser source to prevent overheating.
- Some systems use air cooling, while high-power lasers may require water cooling.
Enclosure and Safety Features:
- Protects operators from laser radiation, ensuring compliance with safety standards.
- Often includes protective shields, fume extractors, and emergency stop mechanisms.
How Laser Marking Works
Surface Interaction
The effectiveness of laser marking depends on how the laser beam interacts with the surface of the material. The interaction is influenced by factors such as the material’s composition, the laser’s wavelength, and the energy intensity. There are several ways in which a laser beam modifies a surface:
- Thermal Effect: The laser heats the material, causing oxidation or a chemical reaction that alters its color without removing the material (annealing).
- Ablation: The laser removes a thin layer of the material, creating high-contrast, deep engravings (common in metal and plastic markings).
- Foaming: The laser modifies the structure of certain plastics, producing a raised, lighter-colored mark.
- Carbonization: The laser extracts oxygen and hydrogen from organic materials, leaving behind a dark-colored mark (used in leather, wood, and polymers).
- Coloration: The laser changes the molecular structure of a material, producing color variations without surface damage (used in anodized aluminum and some plastics).
Automation and Control
Computer-Aided Design (CAD) and Software Integration:
- Laser marking systems are controlled using specialized software that allows users to design and input text, logos, barcodes, and serial numbers.
- Software integration enables automation in industrial applications, allowing machines to work in a continuous production line.
CNC and Robotic Control:
- In large-scale production, laser marking machines are integrated with computer numerical control (CNC) systems or robotic arms for high-speed, repeatable, and precise marking.
- Automation reduces human error and increases productivity.
Vision Systems and Quality Control:
- Some laser marking systems incorporate vision systems that inspect and verify markings for accuracy.
- This is especially useful in industries requiring serial number marking and traceability, such as electronics and medical device manufacturing.
Pulse Modulation
Continuous Wave (CW) vs. Pulsed Lasers:
- Continuous Wave Lasers: Emit a constant beam of laser energy, suitable for applications requiring deep engraving or cutting.
- Pulsed Lasers: Deliver energy in short bursts, reducing heat accumulation and enabling fine, high-contrast markings without damaging the material.
Nanosecond, Picosecond, and Femtosecond Pulsing:
- Nanosecond Pulses: Common in industrial laser marking, balancing speed and quality.
- Picosecond and Femtosecond Pulses: Used for ultra-precise marking, especially in electronics and medical applications, where minimal heat damage is required.
Adjustable Pulse Frequency:
- Allows users to control the density of the marking, improving readability and customization for different materials.
Cooling Systems
Air Cooling:
- Common in low- to mid-power laser marking machines (e.g., fiber and UV lasers).
- Uses fans and heat sinks to dissipate heat, making it compact and maintenance-friendly.
Water Cooling:
- Used in high-power laser marking systems, such as CO2 lasers and industrial fiber lasers.
- Circulates water to remove excess heat, providing better thermal stability for prolonged operation.
Thermal Management Sensors:
- Advanced laser systems include sensors to monitor and regulate temperature, ensuring optimal performance and preventing system failures.
Types of Laser Marking
Laser Annealing
Materials:
- Stainless steel
- Titanium
- Certain metal alloys
Applications:
- Medical instruments and surgical tools
- Automotive and aerospace components
- Industrial part identification requiring corrosion resistance
Advantages:
- No material removal, preserving surface integrity
- High-contrast and wear-resistant marks
- Ideal for industries requiring strict hygiene and durability
Laser Etching
Materials:
- Metals (stainless steel, aluminum, brass)
- Coated metals (anodized aluminum)
- Plastics
Applications:
- Serial numbers, barcodes, and QR codes
- Industrial tools and electronic components
- Aerospace and medical device identification
Advantages:
- Faster than engraving, requiring less energy
- Produces high-contrast, readable marks
- Suitable for applications with minimal depth requirements
Laser Engraving
Materials:
- Metals (steel, aluminum, gold, silver)
- Wood
- Plastics
- Glass
Applications:
- Branding and logo engraving
- Jewelry personalization
- Industrial and aerospace parts requiring durable markings
Advantages:
- Highly durable and wear-resistant marks
- Suitable for deep marking and serialization
- Works on a variety of materials
Laser Ablation
Materials:
- Coated metals
- Painted surfaces
- Anodized aluminum
- Films and foils
Applications:
- Automotive and aerospace part identification
- Printed circuit board (PCB) marking
- Paint and coating removal for selective marking
Advantages:
- High precision for detailed applications
- No damage to the base material
- Environmentally friendly, eliminating chemical-based processes
Laser Foaming
Materials:
- Thermoplastics (ABS, polyethylene, polypropylene)
- Rubber
Applications:
- Marking medical and electronic devices
- Branding on consumer products
- Automotive plastic component labeling
Advantages:
- High-contrast markings without material removal
- Ideal for permanent, tamper-resistant markings
- Suitable for industries requiring strict traceability
Color Laser Marking
Materials:
- Stainless steel
- Titanium
- Certain plastics and coated metals
Applications:
- High-end branding and decorative applications
- Watch and jewelry customization
- Electronic and medical device marking
Advantages:
- Wide range of color options
- High-precision aesthetic customization
- Permanent and fade-resistant markings
Materials Commonly Used in Laser Marking
Metals
Common Metals Used in Laser Marking:
- Stainless Steel: Ideal for medical, aerospace, and industrial applications due to its resistance to corrosion and oxidation-based annealing marks.
- Aluminum: Often used in the aerospace and electronics industries, allowing for high-contrast markings, especially on anodized aluminum.
- Brass and Copper: Common in electrical components and decorative applications; requires high-power lasers due to reflectivity.
- Gold and Silver: Used for engraving jewelry, watches, and premium branding applications.
- Titanium: Marked for aerospace, medical implants, and high-performance engineering applications, often with color laser marking.
Plastics
Common Plastics Used in Laser Marking:
- ABS (Acrylonitrile Butadiene Styrene): Used in electronics and automotive parts; offers sharp, high-contrast markings.
- Polycarbonate: Ideal for durable industrial and medical applications.
- Polyethylene & Polypropylene: Used in packaging, labels, and containers.
- Nylon: Common in manufacturing tools and machine components, allowing precise marking.
Ceramics and Glass
Common Ceramics & Glass Used in Laser Marking:
- Industrial Ceramics: Used in electronics, aerospace, and medical applications; provides permanent and precise markings.
- Glassware and Optical Components: Marking for branding, security, and traceability, such as serial numbers on bottles or barcodes on optical lenses.
Organic Materials
Common Organic Materials Used in Laser Marking:
- Wood: Used for artistic engravings, signage, and furniture customization.
- Leather: Common in fashion, luxury branding, and personalization of wallets, belts, and handbags.
- Paper and Cardboard: Marking for product packaging, barcodes, and security printing.
- Textiles and Fabrics: Used in clothing labels, patterns, and high-end customization.
Coated or Painted Surfaces
Common Coated or Painted Surfaces Used in Laser Marking:
- Anodized Aluminum: Used in electronic casings and aerospace parts, offering sharp and durable markings.
- Painted Metals: Common in automotive parts, signage, and industrial tools, where precise laser removal of paint creates high-contrast marks.
- Powder-Coated Materials: Marked in industries requiring durable, tamper-proof identification.
Advantages and Disadvantages of Laser Marking
Advantages of Laser Marking
- High Precision and Quality: Laser marking provides extremely precise and detailed markings, making it ideal for intricate designs, fine text, and high-resolution images. The controlled laser beam ensures uniform marking quality, even on small components such as microchips and medical devices.
- Durability and Permanence: Laser markings are permanent and resistant to wear, corrosion, and fading. Unlike printed or painted markings, laser-etched engravings withstand extreme conditions such as high temperatures, chemicals, and abrasion, making them ideal for industrial, automotive, and aerospace applications.
- Non-Contact Process: Unlike traditional engraving or mechanical marking, laser marking is a non-contact process, meaning the laser does not physically touch the material. This minimizes mechanical stress and reduces the risk of damage, especially for delicate components.
- Versatility: Laser marking is compatible with a wide range of materials, including metals, plastics, glass, ceramics, wood, leather, and coated surfaces. Different types of lasers (fiber, CO2, UV, and green lasers) allow for customization depending on material properties and application requirements.
- Cost-Effectiveness and Efficiency: Laser marking systems have low operating costs after the initial investment. Since there are no consumables like ink or chemicals, businesses save on material costs. Additionally, laser marking is a fast process, allowing for high-speed production with minimal downtime.
- Eco-Friendliness: Laser marking is an environmentally friendly technology because it does not use inks, solvents, or chemicals that generate waste. It also reduces the need for disposable labels and printed stickers, making it a sustainable marking solution.
- Easy Integration and Automation: Modern laser marking systems can be easily integrated into production lines using CNC machines, robotics, and automated assembly systems. Many systems come with user-friendly software for efficient operation and compatibility with barcode scanning and tracking systems.
- Mass Customization: With computer-controlled laser systems, businesses can easily adjust designs, serial numbers, QR codes, and barcodes without the need for physical tools or templates. This makes laser marking ideal for personalized and mass-production applications.
Disadvantages of Laser Marking
- Higher Initial Investment: One of the biggest drawbacks of laser marking is the higher upfront cost compared to traditional marking methods such as inkjet printing or mechanical engraving. High-quality laser marking machines require significant investment, though they offer long-term savings in maintenance and consumables.
- Material Limitations: While laser marking is versatile, some materials are challenging to mark. Certain transparent materials (e.g., clear plastics and glass) and highly reflective metals require specific laser types (e.g., UV lasers, green lasers) to achieve effective results.
- Laser Safety: Laser marking machines emit high-energy laser beams, which can pose safety risks such as eye damage and skin burns if proper precautions are not taken. Laser systems must comply with safety standards, and operators need protective eyewear and enclosures to minimize exposure risks.
- Fume Extraction and Ventilation: During laser marking, especially on plastics and coated materials, fumes and particulates may be released. Proper ventilation and fume extraction systems are necessary to maintain a safe working environment and comply with occupational health regulations.
- Heat-Affected Zones (HAZ): Some materials, particularly thin metals, and plastics, may experience heat-affected zones (HAZ), where excessive laser energy causes discoloration, warping, or structural weakening. This issue can be minimized with optimized laser parameters.
- Complex Parameter Setup: Achieving optimal marking quality requires fine-tuning various laser parameters such as power, speed, frequency, and pulse duration. Different materials and marking depths require adjustments, making the initial setup more complex compared to traditional marking methods.
- Limited Depth for Some Applications: While laser engraving can achieve deep marks, it may not be suitable for applications requiring very deep etching. Some industries, such as mold-making or deep relief engraving, might require mechanical engraving methods for greater depth.
Laser Marking VS. Other Marking Methods
Inkjet Printing VS. Laser Marking
Dot Peen Marking VS. Laser Marking
Chemical Etching VS. Laser Marking
Stamping and Embossing VS. Laser Marking
Typical Industrial Applications of Laser Marking
Automotive and Aerospace
Common laser-marked components include:
- Engine parts and metal casings
- Chassis and frame markings
- Aircraft turbine blades and engine components
- Vehicle identification numbers (VINs)
- Brake systems and fuel injection components
Electronics and Semiconductors
Applications in this sector include:
- Marking PCBs (Printed Circuit Boards) with part numbers and traceability codes
- Serial numbering and branding on microchips, transistors, and capacitors
- QR codes and barcodes on smartphones, tablets, and laptops
- High-contrast markings on plastic connectors and casings
Medical Devices
Common laser-marked medical devices include:
- Surgical instruments and scalpels
- Orthopedic implants (titanium, stainless steel, ceramics)
- Medical tubing and catheters
- Dental tools and implants
Jewelry and Luxury Goods
Applications in this sector include:
- Engraving serial numbers on luxury watches
- Personalizing gold, silver, and platinum jewelry with custom designs
- Brand logos on high-end accessories such as leather wallets and handbags
- Security markings on high-value items to prevent counterfeiting
Packaging and Consumer Goods
Common applications include:
- Expiration dates, batch codes, and barcodes on food and beverage packaging
- Laser-etched logos and branding on cosmetic bottles and containers
- Marking pharmaceutical packaging for traceability
- Anti-counterfeit measures for luxury goods and high-end packaging
Promotional and Custom Products
Popular laser-marked promotional products include:
- Engraved pens, keychains, and USB drives
- Custom wooden plaques and trophies
- Leather wallets and phone cases with monograms
- Glass and acrylic awards with personalized inscriptions
Industrial Manufacturing
Examples of industrial applications include:
- Serial numbers and barcodes on machinery components
- Tracking labels on tools and hardware
- Part identification for supply chain management
- Deep engraving for mold-making and industrial dies
Considerations Before Purchasing Laser Marking Machines
Material Compatibility
Different laser marking technologies are suited for different materials, so it’s essential to choose a machine that can effectively mark your products.
- Fiber lasers are ideal for metals, including stainless steel, aluminum, brass, and titanium, as well as some plastics.
- CO2 lasers are best suited for organic materials, such as wood, leather, glass, and plastics.
- UV lasers and green lasers are used for delicate or heat-sensitive materials, including circuit boards, glass, and soft plastics.
Required Mark Depth and Speed
The depth and speed of laser marking vary based on the application.
- Shallow marking (etching, annealing) is ideal for electronics, medical devices, and branding applications, where precision and surface integrity are important.
- Deep engraving is needed for automotive, aerospace, and heavy-duty industrial parts, requiring higher laser power.
- High-speed marking is crucial for mass production, such as packaging and consumer goods, where efficiency is a priority.
Laser Power and Wavelength
The power and wavelength of a laser determine its effectiveness on different materials and marking types.
- Low-power lasers (10W – 30W) are suitable for fine, high-precision markings on plastics, jewelry, and medical instruments.
- Medium-power lasers (50W – 100W) provide deeper marking and are ideal for industrial parts, electronics, and automotive applications.
- High-power lasers (over 100W) are used for deep engraving, cutting, and heavy-duty metal marking.
- Wavelength considerations:
- 1064 nm (Fiber Laser): Best for metals and some plastics.
- 6 µm (CO2 Laser): Ideal for organic materials like wood, glass, and acrylic.
- 355 nm (UV Laser): Used for delicate materials, such as circuit boards and medical devices.
Automation and Integration
For businesses involved in high-volume production, it is crucial to consider how well a laser marking machine integrates with existing production lines and automation systems.
- Standalone machines are great for low to mid-volume marking and require manual operation.
- Fully automated systems with robotic arms, conveyors, or CNC control improve efficiency and reduce labor costs.
- Software compatibility is important for seamless integration with barcode systems, databases, and ERP software for traceability.
Safety Considerations
Laser marking machines use high-energy laser beams, requiring strict safety measures to protect operators and the workplace. Consider the following:
- Laser class certification: Machines are classified from Class 1 (safe for enclosed systems) to Class 4 (high-risk exposure).
- Protective enclosures: Ensure that the system includes shielding, interlocks, and fume extraction systems.
- Operator training: Proper training on laser safety guidelines is essential to prevent accidents.
- Ventilation and fume extraction: Some materials, such as plastics and coated metals, produce harmful fumes during marking, requiring an effective extraction system.
Budget and Return on Investment (ROI)
The cost of a laser marking machine varies depending on its power, speed, features, and level of automation. While the initial investment may be higher than traditional marking methods, laser marking provides long-term cost savings due to:
- No consumables: Unlike inkjet printing, laser marking requires no ink or chemicals.
- Low maintenance: Laser machines have fewer moving parts and require minimal servicing.
- High-speed production: Faster marking times lead to increased throughput and efficiency.
To assess the ROI, consider:
- Projected production volume and efficiency gains
- Cost savings on consumables and maintenance
- Product lifespan and marking durability benefits
After-Sales Support and Training
Reliable after-sales support is crucial for keeping your laser marking system operational and efficient. Before purchasing, evaluate the following:
- Warranty period and coverage for repairs and parts replacement.
- Technical support availability: 24/7 online or on-site support is beneficial for minimizing downtime.
- Software updates: Ensure that the manufacturer provides regular software upgrades to keep the machine optimized.
- Operator training programs: A well-trained workforce ensures efficient operation and maintenance of the laser system.
Safety in Laser Marking Operations
Laser Classification
Laser marking machines are classified based on their potential hazard levels as defined by international safety standards (such as IEC 60825-1). Understanding these classifications helps businesses implement appropriate safety measures for different types of laser systems:
- Class 1: Completely safe for human exposure, as the laser is fully enclosed within a protective housing. Most industrial laser marking systems designed for automated production are Class 1.
- Class 2: Emits visible laser radiation and is safe under normal operation, as the human blink reflex provides protection.
- Class 3: Can cause eye injuries if directly exposed to the beam. Requires protective eyewear and controlled operation.
- Class 4: The most hazardous laser classification, with risks of eye injury, skin burns, and fire hazards. These lasers require strict safety protocols, enclosures, and operator protection.
Protective Eyewear
Exposure to laser radiation can cause serious eye injuries, including retinal damage and vision impairment. It is essential to use laser safety goggles specifically designed for the wavelength of the laser being used.
- Fiber lasers (1064 nm): Require near-infrared protective goggles.
- CO2 lasers (10.6 µm): Need far-infrared protective lenses.
- UV lasers (355 nm) and green lasers (532 nm): Require specialized protective eyewear for shorter wavelengths.
Enclosures and Interlocks
For maximum safety, laser marking systems should be enclosed to prevent accidental exposure to the laser beam. Laser safety enclosures offer multiple benefits, including:
- Preventing laser radiation from escaping the workspace
- Protecting operators from direct or scattered laser beams
- Minimizing the risk of accidental reflections from shiny surfaces
Fume Extraction
To ensure a safe and clean workspace, fume extraction systems should be installed to:
- Remove hazardous airborne particles generated during laser marking.
- Filter out toxic gases and chemical vapors to protect operator health.
- Improve air quality and maintain compliance with environmental regulations.
Training and Certification
Proper training is essential to ensure that operators understand the risks of laser marking and follow safe operating procedures. Employers should provide comprehensive training programs that cover:
- Laser classification and associated hazards
- Correct usage of protective equipment (eyewear, enclosures, fume extractors)
- Emergency shutdown procedures and safety protocols
- Proper machine operation and maintenance