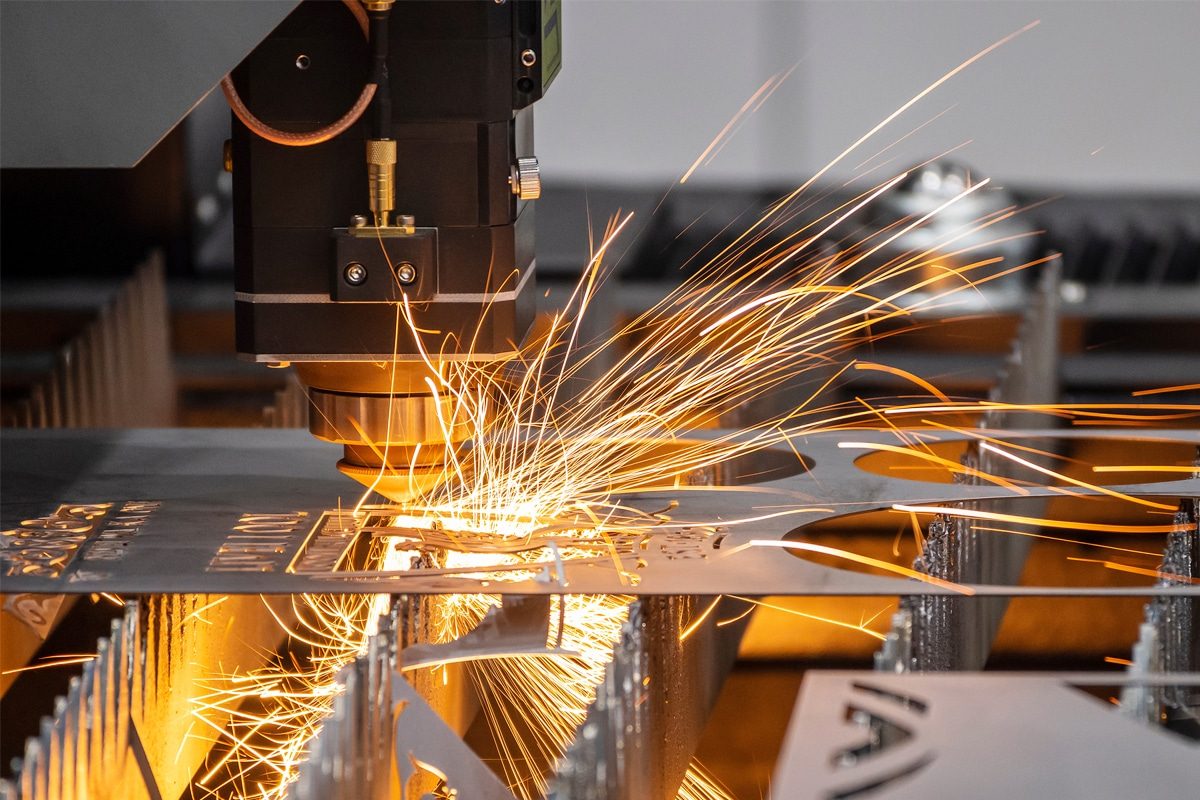
Introduction to Laser Cleaning Machines
Fundamentals of Laser Cutting
The Nature of Laser Light
How Lasers Are Generated
Laser Beam Delivery and Focusing
Thermal Processes in Laser Cutting
The cutting process relies on the intense heat generated by the laser beam, which interacts with the material in one of the following ways:
- Vaporization Cutting: The laser heats the material to its boiling point, causing it to vaporize. This is common for thin materials and high-precision cutting.
- Fusion Cutting: The material is melted, and an assist gas (such as nitrogen or argon) is used to blow away the molten material, producing clean cuts.
- Oxidation Cutting (Flame Cutting): Oxygen is used as an assist gas to react with the heated material, generating additional heat and enabling faster cutting, particularly for carbon steel.
- Thermal Stress Cracking: Used for brittle materials like glass, where thermal expansion causes controlled fracturing along the desired cut line.
Types of Laser Cutting Machines
CO2 Laser Cutting Machines
Key Features:
- High cutting precision: Produces smooth and polished edges, reducing the need for post-processing.
- Versatile material compatibility: Excellent for cutting, engraving, and marking non-metals.
- Affordable operation: Lower cost compared to high-power fiber lasers.
- Large working area availability: Suitable for cutting large sheets of materials.
- Moderate power options: Available in different power levels (e.g., 60W–600W) for various applications.
Advantages:
- Excellent for engraving and intricate designs.
- Produces minimal material wastage.
- Highly efficient for sign-making and artistic applications.
- More cost-effective for cutting non-metals compared to fiber lasers.
- Well-established and reliable technology with a broad range of machine models.
Limitations:
- Not suitable for cutting reflective metals like copper or aluminum.
- Requires regular maintenance, such as mirror alignment and gas refilling.
- Slower cutting speeds compared to fiber lasers for metals.
Fiber Laser Cutting Machines
Key Features:
- High power efficiency: Fiber lasers convert over 30–40% of electrical energy into laser energy, making them more efficient than CO2
- Faster cutting speeds: Especially for thin and medium-thickness metals.
- Minimal maintenance: No moving mirrors or gas tubes, resulting in lower maintenance costs.
- Compact design: Requires less space compared to CO2 laser cutting systems.
- Long lifespan: Fiber laser diodes last significantly longer (50,000+ hours) than CO2 laser tubes.
- Low operational costs: No consumable gases or costly components.
Advantages:
- Highly efficient for cutting metals with high precision.
- Superior energy efficiency, reducing power consumption.
- Can cut highly reflective metals (aluminum, brass, copper) without damage.
- Requires minimal maintenance compared to CO2
- Ideal for industrial and high-production environments.
Limitations:
- Higher initial cost than CO2
- Less effective for non-metals like acrylic, wood, or leather.
- Cutting very thick materials (>20mm) may require high power, increasing costs.
Nd: YAG Laser Cutting Machines
Key Features:
- High peak power: Capable of deep penetration cutting and welding.
- Works well with both pulsed and continuous-wave modes.
- Best suited for applications requiring fine-detail work.
- Used for marking, engraving, and micro-machining applications.
Advantages:
- Effective for deep engraving and micro-machining.
- Good for laser welding and spot welding.
- Works well on metals and some ceramics.
- Pulsed laser capability reduces heat damage on delicate materials.
Limitations:
- Shorter lifespan due to wear on the crystal medium.
- Lower efficiency compared to fiber lasers.
- High maintenance costs due to crystal degradation.
Other Laser Cutting Machine Types
Excimer Lasers (Ultraviolet Lasers):
- Operate in the UV spectrum, making them suitable for delicate and heat-sensitive materials.
- Used in semiconductor manufacturing, medical applications, and surface treatments.
Green Lasers:
- Operate at a 532 nm wavelength, making them ideal for cutting highly reflective materials like copper and gold.
- Used in solar panel manufacturing, precision electronics, and battery production.
Ultrafast Lasers (Femtosecond & Picosecond Lasers):
- Generate extremely short pulses to cut with minimal heat impact, reducing material damage.
- Used in high-precision industries like semiconductors, biomedical devices, and scientific research.
Hybrid Laser Cutting Machines:
- Combine laser cutting with mechanical methods (such as waterjets or plasma cutting) for better material adaptability.
- Used in aerospace, military, and high-strength material applications.
Advantages and Disadvantages of Laser Cutting
Advantages of Laser Cutting
High Precision and Accuracy
Faster Cutting Speeds and High Productivity
Minimal Material Waste and Narrow Kerf Width
Versatility Across Multiple Materials
Reduced Heat-Affected Zone (HAZ) and Minimal Distortion
Low Maintenance and Long Service Life (Fiber Lasers)
Disadvantages of Laser Cutting
High Initial Investment Costs
One of the most significant drawbacks of laser cutting technology is the high upfront cost. Industrial-grade laser cutting machines, especially high-power fiber lasers (6000W to 40000W), can range from $30,000 to over $200,000, depending on specifications and additional automation features.
While operating costs may be lower compared to plasma or waterjet cutting, the initial capital expenditure can be a barrier for small businesses or manufacturers with limited budgets.
Limited Cutting Thickness
High Power Consumption in Some Models
Safety Hazards (Laser Radiation, Fumes, and Burns)
Limited Effectiveness on Highly Reflective Metals
Materials and Their Suitability for Laser Cutting
Metal Materials
Stainless Steel
Stainless steel is one of the most commonly laser-cut metals due to its high strength, corrosion resistance, and excellent absorption of fiber laser wavelengths. Fiber lasers provide high-precision cuts with minimal heat-affected zones, making stainless steel ideal for automotive, aerospace, medical, and industrial applications.
- Best Cutting Method: Fiber Laser
- Recommended Assist Gas: Nitrogen (for oxide-free edges) or Oxygen (for increased cutting speed).
- Suitability: Excellent for thin to thick sections (up to 25mm with high-power lasers).
Carbon Steel
Carbon steel is highly responsive to laser cutting, especially when using oxygen-assist gas, which promotes an exothermic reaction that enhances cutting efficiency. It is widely used in construction, machinery, and industrial manufacturing.
- Best Cutting Method: Fiber Laser
- Recommended Assist Gas: Oxygen (for faster cuts) or Nitrogen (for cleaner edges).
- Suitability: Excellent for thicknesses up to 25mm (higher power lasers can cut up to 30mm).
Aluminum
Aluminum is more challenging to cut with lasers due to its high reflectivity and thermal conductivity, which can cause energy loss and inefficient cutting. However, fiber lasers with high power (6kW+) can effectively cut aluminum when proper settings and assist gases are used.
- Best Cutting Method: Fiber Laser
- Recommended Assist Gas: Nitrogen (to prevent oxidation) or Air (for cost-effective cutting).
- Suitability: Good for thicknesses up to 15mm, but requires high power and precise beam settings.
Copper and Brass
Copper and brass pose challenges for laser cutting due to their high reflectivity and thermal conductivity, which can cause beam reflection and heat dissipation. However, high-power fiber lasers (6kW+) with specialized beam absorbers can effectively cut these metals, making them suitable for electronic, decorative, and industrial applications.
- Best Cutting Method: Fiber Laser (with anti-reflection technology).
- Recommended Assist Gas: Nitrogen (to prevent oxidation) or Air (for budget-friendly cuts).
- Suitability: Moderate to Good, with limitations on thick sections.
Titanium
Titanium is widely used in aerospace, medical, and high-performance applications due to its high strength-to-weight ratio and corrosion resistance. Laser cutting provides clean, precise cuts with minimal heat-affected zones, making it one of the best methods for processing titanium.
- Best Cutting Method: Fiber Laser
- Recommended Assist Gas: Argon or Nitrogen (to prevent oxidation).
- Suitability: Excellent, but requires precise control to avoid material embrittlement.
Non-Metallic Materials
Plastics (Acrylic, Polycarbonate, Polyethylene, etc.)
Plastics are widely used in advertising, packaging, medical, and industrial applications. However, not all plastics are equally suited for laser cutting.
- Acrylic (PMMA): Excellent suitability, produces polished edges when cut with a CO2 laser.
- Polycarbonate: Not recommended—produces discolored edges and releases harmful fumes.
- Polyethylene (PE) & Polypropylene (PP): Moderate suitability, can be cut cleanly but may melt if not properly controlled.
- PVC (Polyvinyl Chloride): Not suitable—releases toxic chlorine gas, which is hazardous to health and machine components.
- Best Cutting Method: CO2 Laser
- Recommended Assist Gas: Air (for general cutting), Nitrogen (for flame suppression).
Wood and Plywood
Wood is highly suitable for CO2 laser cutting, making it popular in furniture, signage, decorative, and craft industries. Different wood types behave differently:
- Softwoods (Pine, Cedar, etc.): Easy to cut, minimal charring.
- Hardwoods (Oak, Mahogany, etc.): Good suitability, may require higher power settings.
- Plywood & MDF: Good suitability, but adhesives in the layers may cause uneven cuts.
- Best Cutting Method: CO2 Laser
- Recommended Assist Gas: Air (for clean edges and fire control).
Leather and Fabric
Laser cutting is widely used in fashion, footwear, upholstery, and textile industries due to its ability to create intricate designs without fraying.
- Leather: Excellent suitability, produces smooth edges with minimal burn marks.
- Cotton, Polyester, Silk, Nylon: Highly suitable, prevents fraying compared to mechanical cutting.
- Best Cutting Method: CO2 Laser
- Recommended Assist Gas: Air (to reduce charring and discoloration).
Special Materials
Ceramics and Glass
Ceramics and glass are challenging to cut due to their brittleness and high melting points. However, ultrafast pulsed lasers (femtosecond lasers) can micro-cut and engrave ceramics and glass without causing fractures.
- Best Cutting Method: Ultrafast Laser (Femtosecond/Picosecond Lasers)
- Suitability: Moderate to Good, with limitations on thick sections.
Composites (Carbon Fiber, Fiberglass, etc.)
Composites are widely used in aerospace, automotive, and sports equipment. Laser cutting is suitable for some composites but requires careful control to avoid delamination or excessive heat damage.
- Carbon Fiber: Moderate suitability, requires precise beam control to avoid burning.
- Fiberglass: Not ideal, as burning can cause hazardous fumes and irregular cuts.
- Best Cutting Method: CO2 Laser (for thin composites), Fiber Laser (for precision cuts).
- Recommended Assist Gas: Air or Nitrogen (to prevent oxidation).
Laser cutting offers exceptional versatility, but choosing the right laser type for the material is crucial:
- Fiber lasers excel in metal cutting, offering high precision, speed, and efficiency.
- CO2 lasers are ideal for non-metals such as wood, acrylic, leather, and plastics.
- Ultrafast lasers are suitable for ceramics, glass, and micro-machining applications.
Laser Cutting Process Steps
Design and Preparation
Creating the Design
- Designs are created using CAD (Computer-Aided Design) software such as AutoCAD, SolidWorks, or CorelDRAW.
- The design file is usually saved in formats like DXF, DWG, AI, or SVG, which are compatible with laser cutting software.
- Vector-based designs are preferred for laser cutting as they allow precise and scalable cutting paths.
Material Selection and Preparation
- The choice of material depends on the application (e.g., metals, plastics, wood, acrylic, or composites).
- The material should be properly cleaned and positioned on the laser bed to prevent dust, contaminants, or irregularities from affecting the cutting process.
- For reflective metals like aluminum or copper, special coatings or techniques may be required to reduce beam reflection and improve cutting efficiency.
Nesting Optimization
- Nesting software arranges parts efficiently on the material sheet to minimize waste and reduce production costs.
- Proper nesting also ensures that heat distribution is even, preventing material distortion during cutting.
Machine Setup and Calibration
Laser Focus Adjustment
- The laser beam must be precisely focused on the material surface to achieve a small, concentrated spot size, ensuring clean and sharp cuts.
- Auto-focusing mechanisms or manual adjustments are used to set the correct focal length based on material thickness.
Workpiece Positioning and Clamping
- The material is placed on the laser cutting bed, and in some cases, clamps or vacuum tables are used to hold it in place.
- Proper alignment ensures that the laser follows the exact cutting path without deviations.
Assist Gas Connection and Pressure Check
- Assist gases (oxygen, nitrogen, or air) help improve cutting quality by blowing away molten material, preventing oxidation, and reducing heat-affected zones.
- Gas flow and pressure settings must be adjusted based on material type (e.g., oxygen for carbon steel, nitrogen for stainless steel and aluminum).
Cutting Speed, Power, and Gas Selection
Laser Power Selection
- Power levels depend on material thickness and type.
- Lower power (e.g., 1500W – 2000W) is used for thin metals and non-metals.
- Higher power (e.g., 3000W – 40000W) is required for thicker materials (e.g., stainless steel, aluminum).
Cutting Speed Optimization
- Fast cutting speeds minimize heat buildup but may cause incomplete cuts.
- Slow cutting speeds improve precision but can lead to excessive heat-affected zones and burning.
- Fine-tuning the balance between speed and power ensures optimal edge quality and minimal material waste.
Assist Gas Selection
- Oxygen (O2) – Used for carbon steel, enhances oxidation for faster cutting speeds but may leave oxide edges.
- Nitrogen (N2) – Preferred for stainless steel, aluminum, and titanium, prevents oxidation for clean and bright edges.
- Compressed Air (Air) – Cost-effective for plastics, wood, and acrylic, but may not be ideal for high-quality metal cutting.
Cutting Parameters and Quality Control
Key Cutting Parameters
- Beam Diameter: Affects cut width and precision. Smaller diameters improve fine detailing.
- Pulse Frequency: Higher frequencies are used for engraving and fine cutting, while lower frequencies are used for thicker materials.
- Kerf Compensation: Ensures the laser follows the correct cutting path to compensate for material removal width.
Quality Inspection
Once the cutting process is complete, the quality of the cut is inspected for defects such as:
- Rough or jagged edges (indicates incorrect speed or gas selection).
- Excessive burrs or dross (suggests improper power settings).
- Burn marks or discoloration (caused by excessive heat or oxidation).
Post-Cutting Cleaning and Finishing
- For metals: Deburring or polishing may be required to remove sharp edges.
- For acrylic and plastics: A flame-polishing technique can enhance edge clarity.
- For industrial applications: Additional surface treatments or coatings may be applied to prevent corrosion.
Industrial Applications of Laser Cutting
Automotive Industry
Applications in Automotive Manufacturing
- Chassis and Body Panels: Laser cutting shapes steel and aluminum car frames with high accuracy.
- Exhaust Systems and Heat Shields: Precise cutting ensures efficient exhaust flow and thermal management.
- Interior and Exterior Components: Laser processing is used for dashboard panels, trim parts, and seat frames.
- Airbags and Safety Features: Laser cutting is used for fabricating airbag materials with pre-designed tear patterns for controlled deployment.
Aerospace and Defense Industry
Applications in Aerospace and Defense
- Aircraft Fuselage and Wing Components: Laser cutting ensures lightweight yet strong aerospace structures.
- Turbine Blades and Engine Components: Complex heat-resistant alloys are precisely cut to improve efficiency.
- Satellite Components and Spacecraft Structures: Fiber laser cutting is used for intricate micro-components in satellites.
- Military Equipment and Weapons Manufacturing: Laser cutting produces firearm parts, armor plating, and radar components with high precision.
Aerospace and Defense Industry
Applications in Aerospace and Defense
The aerospace and defense industries require extremely high precision and quality standards, making laser cutting a preferred manufacturing method. Materials used in this sector, such as titanium, aluminum, stainless steel, and advanced composites, demand cutting processes that ensure structural integrity and minimal heat distortion.
Electronics and Semiconductors Industry
Applications in Electronics and Semiconductors
- PCB (Printed Circuit Board) Fabrication: Laser cutting ensures high-speed, high-precision production of circuit boards.
- Microchip Manufacturing: Precision laser micromachining allows for ultra-fine detailing of semiconductor components.
- Battery and Energy Storage Components: Laser cutting optimizes copper and aluminum foils used in lithium-ion batteries.
- Flexible Electronics and Displays: OLED and flexible screen panels are laser-cut with micron-level accuracy.
Medical Device Industry
Applications in Medical Device Manufacturing
- Surgical Instruments and Tools: Laser cutting ensures sharp edges and smooth finishes for scalpels and forceps.
- Stents and Implants: Microscopic laser cutting allows for biocompatible implants with high precision.
- Prosthetics and Orthopedic Devices: Laser cutting is used for titanium and carbon fiber components in prosthetics.
- Dental Equipment and Orthodontics: Laser-cut titanium brackets and orthodontic tools improve patient outcomes.
Signage and Advertising Industry
Applications in Signage and Advertising
- Acrylic and LED Signage: Laser cutting ensures smooth, polished edges for illuminated signs.
- Metal Lettering and Logos: Stainless steel, brass, and aluminum are cut for custom signage and branding.
- Wood and Plastic Displays: Retail stores use laser-cut displays and advertising panels for visual impact.
- Event and Exhibition Stands: Laser cutting is used to create intricate event backdrops and trade show displays.
Jewelry and Decorative Arts
Applications in Jewelry and Decorative Arts
- Gold and Silver Jewelry Cutting: Laser cutting enables intricate filigree designs in precious metals.
- Engraving and Personalization: Custom engravings on rings, watches, and luxury goods.
- Decorative Panels and Sculptures: Wood, acrylic, and metal are laser-cut into artistic patterns for home decor.
- Wedding and Event Accessories: Laser-cut acrylic and wood designs for wedding invitations, gifts, and decorations.
Safety Considerations in Laser Cutting
Laser Safety Classifications
Laser Safety Classes:
- Class 1: Completely safe during normal operation. The laser is fully enclosed, preventing exposure (e.g., fiber laser machines with enclosed workspaces).
- Class 2: Low-power visible lasers (≤1mW). Safe under normal use but can cause eye irritation if viewed directly for long periods (e.g., laser pointers).
- Class 3: Medium-power lasers (1mW – 500mW). Can cause eye damage if directly viewed and may pose a fire risk.
- Class 4: High-power lasers (>500mW). Used in industrial laser cutting machines, these lasers can cause severe eye and skin injuries, start fires, and produce hazardous fumes if not handled correctly.
Personal Protective Equipment (PPE)
Essential PPE for Laser Cutting Operators:
- Laser Safety Glasses: Must match the laser wavelength and optical density (OD) rating to block harmful radiation (e.g., fiber lasers require OD 6+ rated eyewear for 1064nm wavelengths).
- Heat-Resistant Gloves: Protect hands from hot metal, sparks, and sharp edges.
- Flame-Resistant Clothing: Prevents burns caused by sparks or molten metal splatter. Cotton or fire-retardant fabrics are recommended.
- Closed-Toe Safety Shoes: Protect feet from falling metal parts and high temperatures.
- Hearing Protection: Some laser cutting machines produce high noise levels due to compressed air assist gases, requiring earplugs or earmuffs.
Fume Extraction and Ventilation
Key Fume Extraction and Ventilation Measures:
- Dedicated Exhaust Systems: Industrial laser cutting machines must be equipped with high-efficiency fume extraction systems to remove harmful particulates and gases.
- HEPA and Activated Carbon Filters: These filters capture ultrafine dust and neutralize toxic fumes from materials like acrylic, PVC, and coated metals.
- Enclosed Workspaces: Fully enclosed laser cutting machines prevent fumes from spreading into the surrounding work environment.
- Proper Airflow Design: Ventilation ducts should be positioned to maximize air movement and prevent smoke accumulation.