
The maximum cutting thickness of the CO2 laser cutting machine
In the world of complex manufacturing and manufacturing, precision is not just a preference, it’s a necessity. As industries continue to seek cutting-edge technology to meet changing needs, CO2 laser-cutting machines have become indispensable tools, offering unparalleled precision and versatility. Among the countless questions that arise in the pursuit of perfection, one stands out: What is the maximum cut thickness that a CO2 laser-cutting machine can handle?
This question is at the heart of optimizing the performance and functionality of your CO2 laser cutting system. Understanding maximum cutting thickness is critical for fabricators and fabricators looking to efficiently and accurately machine materials of varying thicknesses. In this comprehensive exploration, we take an in-depth look at the factors that influence the maximum cut thickness of a CO2 laser cutting machine, revealing the intricate interplay between technology, materials, and operating parameters.

Learn About CO2 Laser Cutting Technology
Before delving further into the intricacies of maximum cutting thickness, it is important to understand the basic principles of CO2 laser technology. At the heart of CO2 laser cutting machines lies the complex interplay of optics, electronics, and high-energy physics that allow them to transform a beam of light into a precision cutting tool.
CO2 laser generators are named because they use carbon dioxide gas as the laser medium to produce an intense infrared beam through a stimulated emission process. Within the laser resonator, an electric current excites the carbon dioxide molecules, causing them to emit photons, which stimulate further emission when they hit other excited molecules. This cascade of photons amplifies light energy, producing a highly concentrated beam with a wavelength typically around 10.6 microns.
The emitted laser beam then passes through a series of mirrors and lenses that focus it onto a small spot on the workpiece. This focusing process helps achieve high precision and quality cut quality. By tightly focusing the laser beam, CO2 laser cutting machines can produce incredibly high power density at the focal point, enabling rapid heating and vaporization of materials.
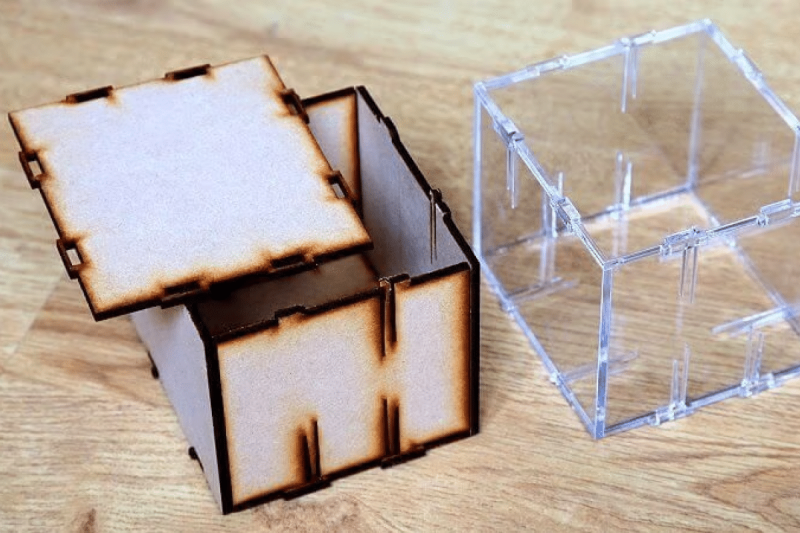
Define The Maximum Cutting Thickness
In the world of CO2 laser cutting machines, the term “maximum cutting thickness” encompasses a key parameter that profoundly affects the range and versatility of these powerful tools. Simply put, the maximum cutting thickness refers to the upper limit of the material thickness that the CO2 laser cutting machine can effectively process.
The concept of maximum cut thickness is inherently related to the functionality and design of a specific CO2 laser-cutting machine. Different machines may have different maximum cutting thickness specifications based on a combination of technical factors, each of which plays a key role in determining a machine’s cutting capabilities. As we delve into the complexity of maximum cut thickness, it is important to consider the factors that influence this critical metric.
For operators and manufacturers seeking to optimize their CO2 laser cutting processes, understanding the interaction of these factors is critical. It is not a single variable, but a synergy of laser power, beam quality, material properties, and other influencing factors that define the ultimate limit of maximum cut thickness for a specific CO2 laser cutting machine.
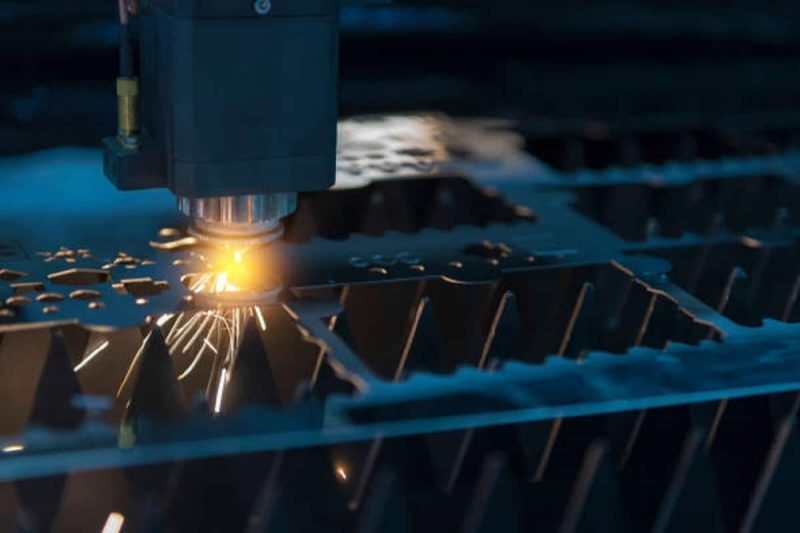
Factors Affecting The Maximum Cutting Thickness
In the field of CO2 laser cutting machines, the maximum cutting thickness is a key parameter that determines the machine’s versatility and applicability to various materials. Achieving precise cuts on thicker substrates requires a detailed understanding of the many factors that affect the maximum cutting thickness of a CO2 laser cutting machine. Let’s delve deeper into these factors to unravel the complexities of this critical dimension of laser cutting technology.
Laser Power
The primary factor affecting maximum cut thickness is laser power. The power of the CO2 laser generator is a direct determinant of the energy delivered to the material. Higher laser power produces a more intense and focused beam that helps penetrate materials deeper, allowing the machine to cut thicker substrates. CO2 laser cutting machines are available in a variety of power levels, from low-power options suitable for delicate materials to high-power systems capable of processing large thicknesses at once.
Beam Quality
The quality of the laser beam emitted by a CO2 laser cutting machine is another key determinant of maximum cut thickness. Beam quality includes properties such as beam divergence, mode stability, and spatial profile. The high-quality beam remains focused over greater distances, allowing for deeper, more precise cuts in thicker materials.
Material Type
The type of material being cut is the basic factor in determining the maximum cutting thickness. CO2 laser generators demonstrate exceptional versatility, capable of processing a wide range of materials, including metals, plastics, wood, and textiles. However, the interaction between the laser beam and the material varies depending on factors such as thermal conductivity, reflectivity, and absorption properties. Metal, for example, often presents greater challenges due to its high reflectivity, affecting the maximum thickness that can be effectively cut.
Auxiliary Gas
The type and pressure of assist gas used during cutting can significantly affect the maximum cut thickness. Common assist gases include oxygen, nitrogen, and air, each of which has a different impact on cutting dynamics. The assist gas helps remove molten material from the cut (cut) and acts to prevent excessive heat build-up. The choice of assist gas and its pressure can be customized to the specific material being cut, affecting the machine’s ability to handle different thicknesses.
Beam Delivery System
The beam delivery system consists of components such as focusing lenses and cutting heads, which help improve the accuracy and efficiency of CO2 laser cutting. A carefully designed beam delivery system ensures the laser beam remains focused and aligned as it interacts with the material, resulting in deeper, more consistent cuts across varying thicknesses. Optimal focusing capability helps achieve deeper cuts and improved cutting performance across a wide range of thicknesses. The design and quality of the beam delivery system directly affect the machine’s ability to maintain cutting accuracy in a variety of applications.
Cutting Speed
The speed at which the laser travels through the material (called the cutting speed) is a factor closely related to the maximum cut thickness. Slower cutting speeds allow the material to be exposed to the laser beam for longer, allowing deeper penetration into thicker substrates. However, the relationship between cutting speed and maximum thickness involves a delicate balance, as speeds that are too slow can cause undesirable thermal effects and reduce overall efficiency. Optimizing cutting speed parameters helps achieve the ideal balance between depth of cut, edge quality, and productivity.
By fully understanding and optimizing these factors, operators, and manufacturers can realize the full potential of CO2 laser cutting machines and achieve precise, efficient cuts across a wide range of material thicknesses. Experimentation, combined with a thorough understanding of the interaction between these variables, is the key to pushing the boundaries of maximum cut thickness and realizing the full capabilities of CO2 laser technology.
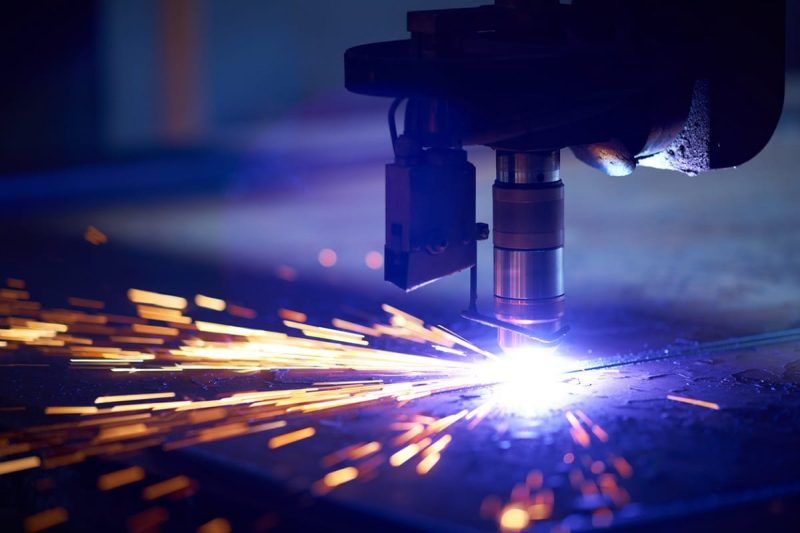
Practical Considerations And Applications
In the field of manufacturing and manufacturing, the maximum cutting thickness that a CO2 laser cutting machine can handle has a significant impact on practical applications in different industries. Understanding the practical considerations and applications of a CO2 laser cutting machine can help you achieve effective utilization of its capabilities. Let’s dive into the various industries and scenarios where CO2 laser cutting technology plays a key role:
Automobile Industry
The automotive industry relies heavily on CO2 laser cutting machines to accurately manufacture car parts. From cutting intricate patterns in automotive interiors to precisely forming metal parts, CO2 lasers offer unparalleled versatility. In the production of chassis components, exhaust systems, and interior panels, CO2 laser cutting machines excel at processing a variety of materials, including steel, aluminum, and plastic, to meet strict quality and performance standards.
Aerospace Industry
Unlike the automotive industry, the aerospace industry typically uses thinner materials such as aluminum alloys and composites. CO2 laser cutting machines have good beam quality and accuracy and can be used for precision cutting of these materials in aircraft component production. Factors such as beam quality and cutting speed help ensure the intricate details and tight tolerances required for aerospace applications.
Signage And Advertising
CO2 laser cutting is widely used in the signage and advertising industry to produce complex and detailed designs. Whether cutting letters and logos from acrylic, wood, or metal, CO2 lasers deliver unparalleled precision and detail. In addition, CO2 lasers can produce complex patterns and decorative elements for architectural signage, interior design, and promotional materials, providing businesses with innovative ways to engage customers and communicate their brand image.
Medical Device Manufacturing
In medical device manufacturing, there is a prominent need for micromachining capabilities. CO2 lasers are known for their precision and are used to cut thin materials to create complex medical components. Practical considerations include fine-tuning cutting parameters to achieve the required level of accuracy without causing thermal damage to sensitive materials. The CO2 laser’s ability to cut a variety of medical-grade materials, including polymers and alloys, makes it indispensable in this field.
Electronics And Consumer Products
CO2 laser cutting machines are widely used in the electronics and consumer goods industries to manufacture a variety of products, including electronic casings, smartphone components, and consumer electronics. CO2 lasers provide precise, burr-free cuts with minimal heat-affected zones, making them suitable for cutting delicate materials such as plastics, glass, and ceramics. In addition, CO2 lasers can produce custom-designed components and prototypes, allowing manufacturers to quickly innovate and adapt to changing consumer needs.
Fabric And Textile Industry
CO2 laser cutting machines are widely used in the fabric and textile industry due to their ability to accurately cut complex patterns, but there is a balance between cutting speed and accuracy that needs to be considered. Whether cutting delicate fabrics or thick textile materials, manufacturers need to optimize cutting parameters to avoid abrasion or burning while ensuring efficient production. CO2 lasers can flexibly process a wide range of textiles, making them suitable for a variety of applications from fashion to industrial textiles.
Architecture And Interior Design
In architecture and interior design applications, CO2 laser cutting machines are used to create custom-designed elements for buildings, interiors, and decorative installations. Whether cutting complex patterns in metal, acrylic, or wood, CO2 lasers offer architects and designers the flexibility to realize their creative visions with precision and accuracy. From architectural facades and decorative screens to custom furniture and lighting fixtures, CO2 laser-cutting machines enable designers to push the boundaries of creativity and craftsmanship.
Manufacturing And Prototyping
CO2 laser cutting machines are valuable tools for manufacturers looking to create custom-designed parts and prototypes with precision and efficiency. Whether cutting sheet metal, plastics, or composites, CO2 lasers provide a fast, cost-effective solution to produce high-quality parts with complex geometries. In addition, CO2 lasers enable rapid prototyping and iteration, allowing designers and engineers to quickly test and refine their designs before moving into full production.
Practical considerations in CO2 laser cutting machine applications go far beyond theoretical limitations. Various industries utilize the capabilities of these machines to cut a variety of materials, each with its unique challenges and requirements. Whether enabling precision in aerospace components, versatility in custom manufacturing, or adaptability in the medical field, CO2 lasers continue to revolutionize manufacturing processes. As technology advances, practical innovations, and practical applications will further push the boundaries of what CO2 laser-cutting machines can achieve, solidifying their status as an indispensable tool in modern industry.

Optimize Maximum Cutting Thickness
As manufacturers seek to push the boundaries of CO2 laser cutting machines, optimizing maximum cut thickness becomes critical. Achieving the highest levels of performance and efficiency requires a strategic approach that encompasses a variety of factors, from machine configuration to laser parameters and cutting conditions. Next, we’ll dive into strategies and considerations for optimizing maximum cut thickness, allowing users to leverage the full potential of CO2 laser cutting technology.
Choose The Right Machine Configuration
The first step in optimizing maximum cut thickness is choosing the right machine configuration. CO2 laser cutting machines come in a variety of models with varying power levels, beam quality, and cutting capabilities. Consider the specific requirements of your application, such as the thickness and type of material you want to cut, and choose a machine that meets those needs. Higher-powered machines are generally capable of cutting thicker materials, while machines with advanced beam delivery systems and optics can increase cutting accuracy and efficiency.
Optimize Laser Parameters
- Laser Power: Laser power is the cornerstone of determining maximum cut thickness, but the right balance needs to be struck between laser power and cut thickness. Too little power may result in incomplete cuts, while too much power may result in undesirable thermal effects. Regularly evaluate the material being processed and adjust laser power accordingly to optimize the depth of cut.
- Beam Quality: The quality of the laser beam directly affects cutting performance. Fine-tuning beam quality involves minimizing beam divergence, ensuring mode stability, and optimizing spatial profiles. The high-quality beam enhances the focus and enables deeper penetration into materials of varying thicknesses.
Optimize Cutting Conditions
- Cutting Speed: The speed at which the laser travels through the material (called the cutting speed) is a critical parameter. Adjust the cutting speed to optimize based on material thickness. Slower speeds are effective for cutting deeper into thicker materials, while faster speeds maintain efficiency when working with thinner substrates.
- Auxiliary Gas: The selection and application of auxiliary gas significantly affects cutting efficiency. For thicker materials, using gases such as oxygen or nitrogen at the appropriate pressure can help remove molten material and enhance the cutting process. However, air pressure needs to be balanced to avoid excessive turbulence or thermal effects.
Material Considerations
- Material Type: Different materials have unique properties that affect the best cutting method. For example, metals may require higher laser power, while non-metallic materials may require adjustments to cutting parameters to avoid poor results. Settings need to be checked and adjusted regularly based on the material being processed.
- Material Density: Denser materials present special challenges. To optimize cut thickness in these materials, consider using higher laser power, adjusting assist gas parameters, or implementing multiple passes to achieve the desired depth of cut.
Advanced Features And Innovation
Explore the advanced capabilities and innovations of CO2 laser cutting technology. Some machines are equipped with adaptive control systems that can automatically adjust cutting parameters in real-time based on the characteristics of the material. Additionally, the multifunctional cutting head provides versatility, allowing users to switch between different configurations for optimal results in a variety of thicknesses.
Regular Maintenance And Calibration
Maintaining the optimal performance of your CO2 laser cutting machine requires regular maintenance and calibration. Make sure all components, including focusing lenses and mirrors, are clean and in good condition. Regular calibration checks help maintain accuracy and consistency in cutting performance.
Continuous Monitoring And Iterative Improvement
Continuous monitoring of the cutting process and results enables iterative improvements. Regularly analyze cut quality, edge finish and overall efficiency. Based on this analysis, parameters are gradually adjusted, always striving for a good balance between accuracy and productivity.
Optimizing the maximum cutting thickness of a CO2 laser cutting machine requires a comprehensive approach that considers machine configuration, laser parameters, cutting conditions, advanced technology, and adaptive control systems. By fine-tuning these factors and trying different settings and strategies, manufacturers can unleash the full potential of their CO2 laser cutting machines, pushing the boundaries of what’s possible in terms of cut thickness and accuracy.
Summarize
The maximum cutting thickness that a CO2 laser cutting machine can handle is influenced by a multitude of factors, each playing a crucial role in determining cutting capabilities. From laser power and beam quality to material type and cutting conditions, these factors interact in complex ways to define the upper limits of cutting thickness.
CO2 laser cutting technology offers unparalleled precision and versatility, allowing for the efficient processing of a wide range of materials across various thicknesses. High-powered laser, combined with advanced beam delivery systems and optimized cutting parameters, enable manufacturers and fabricators to achieve precise cuts with minimal waste and maximum efficiency.
However, achieving optimal cutting thickness requires a strategic approach that involves selecting the right machine configuration, fine-tuning laser parameters, optimizing cutting conditions, and considering material characteristics. Continuous monitoring, maintenance, and iterative improvement further ensure consistent and reliable cutting performance.
As technology continues to advance and innovations emerge, the potential of CO2 laser cutting machines to handle thicker materials and push the boundaries of precision cutting will only continue to grow. By understanding and optimizing the factors related to maximum cutting thickness, manufacturers can unlock new possibilities and achieve unprecedented levels of precision and efficiency in their cutting operations.
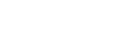
Contact information
- Email:[email protected]
- Skype:[email protected]
- Wechat: +86-19963414011
Address to send the proofing materials
- No. 3 Zone A, Lunzhen Industrial Zone,Yucheng City , Shandong Province.
Related Blog