
Safety protection function of laser welding
The widespread application of laser welding technology brings efficient and accurate production methods for industrial manufacturing. However, with its strong application potential, it is accompanied by potential security risks. In order to ensure that the operator is not injured during laser welding, modern laser welding equipment is generally equipped with a series of advanced security protection functions. These functions not only ensure the health of the operator but also improve the overall safety of the working environment.
This article will deeply explore the types and functions of these security functions, including understanding the working principles of laser welding technology, the importance of laser safety functions, and how they effectively protect the potential damage of the operator to avoid the laser welding process. Guarantee.
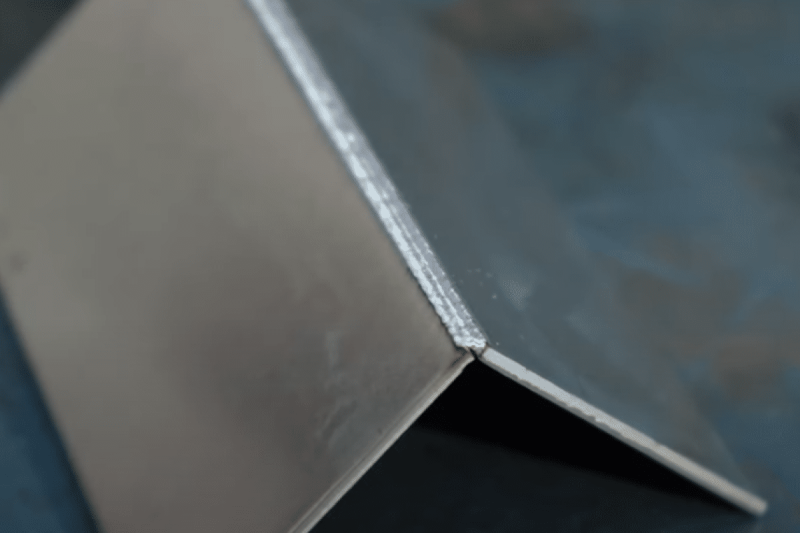
Learn about laser welding technology
Laser welding technology is a highly precise welding method that uses high energy generated by a laser beam to melt and join metal or other materials. This technology is often widely used in manufacturing, electronics, aerospace, and other fields that require highly precise welding. The following is the basic working principle of laser welding technology:
- Laser Source: The first step in laser welding is to generate a high-energy laser beam. The laser generator excites the laser medium in the optical resonant cavity, producing a highly focused laser beam.
- Optical system: Components such as lenses and mirrors concentrate the laser beam onto a very small focus, focusing and guiding it to increase energy density.
- Welding area: The focused laser beam is guided to the area that needs to be welded. The material in this area will be heated to a high enough temperature to melt it and form a molten pool.
- Molten pool formation: When the laser beam hits the surface of the workpiece, the metal locally heats up and melts. The molten pool containing a high degree of thermal energy can quickly melt the metal and then cool it to form a weld.
- Welding alloy: The joining of two or more workpieces through molten metal. Laser welding can be used to weld different types of metals, and due to the highly focused nature of the laser, high-precision welding of small parts can be achieved.
- The advantages of laser welding are its high precision, high efficiency, and non-contact nature. However, it also requires a high degree of control over the laser beam and temperature management during the welding process to ensure optimal welding results.

The importance of laser welding safety features
The reason why laser welding machines have safety functions mainly involves the protection of operators and equipment. These safety functions are crucial to ensuring the safety of the working environment and improving production efficiency.
Prevent operator injury
Laser welding machines use high-energy laser beams to weld, which can cause damage to the operator’s vision, skin, and other body parts. The existence of safety functions can effectively reduce the risk of injuries to operators during the laser welding process and protect their life safety and health.
Reduce laser radiation hazards
Laser radiation is harmful to human tissue, especially the eyes. The safety function of the laser welding machine effectively reduces the wavelength and intensity of laser radiation by using protective covers, filters, and other devices to prevent harm to the operator.
Prevention accidents and losses
Laser welding machines work in high temperature, high pressure, high energy, and other environments, and there is a certain risk of accidents. Through safety functions, laser welding machines can monitor key parameters in real-time, prevent potential problems, take timely response measures, reduce the possibility of accidents, and mitigate the risk of equipment loss and production interruption.
Improve work efficiency
The presence of safety features allows laser welding machines to operate in a safer environment. This not only protects the operator but also helps improve work efficiency. Operators can focus more on monitoring and adjusting the welding process in a safe environment without having to worry too much about their safety.
Composite regulations and standards
Safety compliance is an extremely important aspect of modern manufacturing. Laser welding machines have safety features that can ensure that the equipment complies with relevant regulations and standards and reduce potential legal liability and economic risks.

What are the safety challenges brought by laser welding
Although laser welding technology has significant advantages in improving efficiency and accuracy, its application also brings some potential safety challenges. Here are some safety issues you may face with laser welding:
Laser radiation
Laser radiation is one of the major safety hazards of laser welding. Laser beams are capable of delivering high-intensity light energy, and operators may suffer eye and skin damage if not properly protected. Therefore, protective glasses and protective clothing are essential safety equipment.
Smoke and gas emissions
The fumes and gases generated during laser welding may contain harmful substances such as metal vapors and oxides. These substances may cause harm to the operator’s respiratory system. Effective ventilation systems and wearing filtered respirators are important means of mitigating this safety challenge.
Heat and fire risk
Laser welding produces a high-temperature weld zone, which can lead to heat radiation and fire risks. Measures need to be taken to ensure safety around the welding area to prevent accidental injuries and fires.
Risk of electric shock
Laser welding equipment often requires high currents and voltages, so there is a risk of electric shock. Proper equipment maintenance, grounding, and operator training can reduce the risk of electrical shock.
Material rebound
In laser welding, the melting and evaporation of material can cause small particles to rebound. These particles may cause damage to the operator’s eyes and skin. This risk can be mitigated by using appropriate protective equipment, such as face masks and gowns.
Equipment failure
Failure of laser welding equipment can cause unexpected situations, such as deviation or instability of the laser beam. Regular equipment maintenance and inspections are key to ensuring safe equipment operation.
To deal with these potential safety challenges, laser welding workplaces need to strictly follow safety standards and procedures and provide necessary training and protective equipment to ensure the safety of operators and the environment.

What are the safety features of laser welding
As a high -precision, high -efficiency welding technology, laser welding has brought significant progress to the industrial manufacturing field. However, there are still some potential security risks during laser welding. In order to minimize these potential dangers, modern laser welding equipment is equipped with a number of security functions.
Laser Beam Monitoring System
Laser welding equipment is often equipped with a laser beam monitoring system, a critical safety feature. The system can monitor the position and intensity of the laser beam in real-time as well as any abnormalities during the welding process. By constantly monitoring the status of the laser beam, the system can respond quickly to potential problems. Once it is detected that the laser radiation exceeds the safe range, the system will immediately interrupt the laser emission to prevent the laser radiation from causing damage to the operator’s eyes and skin. This timely response mechanism is the first line of defense to protect operators from the hazards of laser radiation.
Protective Covers and Enclosure Systems
To prevent laser radiation from leaking into the surrounding environment, laser welding equipment is equipped with protective covers and closure systems. These facilities enclose the welding area, reducing the impact on the external environment and reducing the risk of laser radiation. Protective covers are usually made of special materials that can effectively absorb and isolate laser radiation and prevent it from directly irradiating surrounding people. The closed system provides a closed working space, further reducing the impact of laser radiation on the environment and ensuring a safe working environment.
Filtration system
Smoke and harmful gases generated during the welding process are another key issue in laser welding safety. To solve this problem, laser welding equipment is equipped with a filtration system. These systems use high-efficiency filters to filter out harmful particles and gases, reducing their impact on the operator’s respiratory system. By providing a clean working environment, filtration systems reduce the risk of respiratory problems and ensure operator respiratory health.
Emergency stop button
In an emergency, it is crucial to interrupt the laser welding process in time. For this purpose, laser welding equipment is equipped with an emergency stop button. The operator can quickly press the button to immediately cut off the laser emission and prevent further accidents. This button is usually easily accessible, ensuring operators can take quick action when needed, improving safety in emergencies.
Temperature control and cooling system
Laser welding produces a high-temperature welding area, so the equipment is usually equipped with temperature control and cooling systems. These systems reduce the risk of fire and thermal injury by monitoring and regulating the temperature of equipment to prevent it from overheating. At the same time, they ensure that the equipment operates within a stable operating temperature range, improving the overall safety of the equipment.
Safety training and logo
In addition to the safety function of the equipment itself, laser welding operators usually receive relevant safety training. This includes training in laser radiation, equipment operation and emergency treatment to improve the operator’s ability to understand and respond to laser welding safety. In addition, there are clear safety signs on the equipment, reminding operators to pay attention to potential hazards and use protective equipment correctly.
Summarize
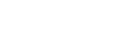
Contact information
- Email:[email protected]
- Skype:[email protected]
- Wechat: +86-19963414011
Address to send the proofing materials
- No. 3 Zone A, Lunzhen Industrial Zone,Yucheng City , Shandong Province.
Related Blog