Laser Welding Aluminum
Laser Aluminum Welding Machine
-
Handheld Standard Laser Welding Machine
Rated 4.75 out of 5$3,300.00 – $7,000.00 This product has multiple variants. The options may be chosen on the product page -
Handheld Portable Laser Welding Machine
Rated 4.75 out of 5$3,200.00 – $6,900.00 This product has multiple variants. The options may be chosen on the product page -
Handheld 3 in 1 Laser Welding Cleaning Machine
Rated 5.00 out of 5$3,400.00 – $7,100.00 This product has multiple variants. The options may be chosen on the product page -
Handheld Air-Cooled Laser Welding Machine
Rated 4.75 out of 5$4,300.00 – $5,700.00 This product has multiple variants. The options may be chosen on the product page -
Handheld Double Wobble Laser Welding Machine
Rated 4.75 out of 5$3,800.00 – $7,500.00 This product has multiple variants. The options may be chosen on the product page -
Handheld Double Wire Feed Laser Welding Machine
Rated 4.75 out of 5$6,400.00 – $7,300.00 This product has multiple variants. The options may be chosen on the product page -
Portable Air-Cooled Laser Welding Machine
Rated 4.50 out of 5$3,400.00 – $5,300.00 This product has multiple variants. The options may be chosen on the product page -
Handheld Air-Cooled 3 in 1 Laser Welding Machine
Rated 5.00 out of 5$3,600.00 – $5,500.00 This product has multiple variants. The options may be chosen on the product page -
CNC Platform Automatic Fiber Laser Welding Machine
Rated 4.50 out of 5$8,500.00 – $12,200.00 This product has multiple variants. The options may be chosen on the product page -
6-Axis Robotic Automatic Laser Welding Machine
Rated 5.00 out of 5$12,300.00 – $16,000.00 This product has multiple variants. The options may be chosen on the product page
Benefits of Laser Welding Aluminum
High Precision
Laser welding provides precise control, ensuring accurate welds with minimal distortion, crucial for applications requiring tight tolerances and high-quality finishes.
Minimal Heat Affected Zone
The focused laser beam limits heat spread, reducing the risk of warping or damaging the surrounding aluminum material, which improves structural integrity.
Increased Welding Speed
Laser welding is faster than traditional methods, enabling quicker production cycles, which reduces overall operational costs and increases manufacturing efficiency.
Strong and Smooth Welds
The concentrated energy of the laser produces deep, consistent welds with smooth surfaces, minimizing post-processing efforts like grinding or polishing.
Flexibility for Complex Geometries
Laser welding machines can handle intricate designs and hard-to-reach areas, making them ideal for aluminum parts with complex shapes or fine details.
Automated and Consistent Results
Maxcool CNC's laser welding systems offer automated features that ensure consistent weld quality, reducing human error and improving productivity in large-scale operations.
Factors to Consider Before Buying Laser Aluminum Welding Machines
Power Output
Ensure the machine's laser power is suitable for the thickness and type of aluminum you plan to weld, affecting depth and speed.
Weld Quality
Evaluate the machine's ability to deliver clean, smooth welds with minimal distortion and porosity, which is crucial for aluminum welding.
Cooling System
Proper cooling is essential for aluminum welding to avoid overheating and ensure consistent performance, especially during long production cycles.
Automation Features
Machines with automated settings and real-time monitoring reduce manual adjustments, improve accuracy, and increase productivity for large-scale aluminum welding projects.
Material Compatibility
Confirm the machine supports different grades of aluminum and allows customization of settings for various alloy compositions to meet specific welding requirements.
Ease of Operation
Consider user-friendly interfaces and control systems that allow operators to quickly adjust settings, ensuring efficient machine operation and reducing downtime.
Maintenance Requirements
Choose a machine with low maintenance needs, which will save time and reduce operational costs, especially when welding highly reflective materials like aluminum.
Warranty and Support
Ensure that the manufacturer offers robust technical support, warranties, and after-sales service to minimize downtime and keep operations running smoothly.
Comparison with Other Aluminum Welding Methods
Dimension | Laser Welding | TIG Welding | MIG Welding |
Precision | Extremely high precision with minimal distortion | High precision but slower speed | Moderate precision, suitable for larger parts |
Speed | Fast, high processing speed with minimal heat | Slow, requires manual precision | Faster than TIG, but slower than laser welding |
Heat Affected Zone (HAZ) | Very small HAZ, reducing material warping | Larger HAZ, more risk of warping | Larger HAZ than laser welding, moderate risk |
Automation | Easily automated for high consistency | Difficult to automate, mostly manual | Can be automated but less precise than a laser |
Weld Appearance | Clean, smooth welds with minimal post-processing | Good appearance but requires more post-processing | Less clean, and may need significant post-processing |
Material Thickness Range | Suitable for both thin and thick aluminum | Ideal for thin materials | Ideal for thicker materials |
Ease of Use | Requires training but minimal user input with automation | Requires skilled operators | Easier to learn than TIG but less precision |
Cost Efficiency | Higher initial cost but low operational costs | Lower initial cost but slower process | Moderate cost, higher consumable use |
Application of Laser Rust Cleaning
- Automotive Industry: Laser welding aluminum is widely used in the automotive sector due to the need for lightweight materials that enhance fuel efficiency.
- Aerospace Industry: In aerospace, where weight reduction and strength are critical, laser welding aluminum is a preferred method for manufacturing aircraft components. Laser welding is used for everything from fuselage parts to intricate structural assemblies.
- Electronics Manufacturing: Laser welding is ideal for creating precise, small-scale welds in electronic components like heat sinks, casings, and connectors, where tight tolerances and minimal heat distortion are essential.
- Bicycle and Sporting Goods: In the production of bicycles and sporting goods, laser welding aluminum ensures strong yet lightweight joints, improving the overall durability and performance of products.
- Construction and Architecture: Laser welding is used to join aluminum elements in façades, window frames, and architectural structures, offering a fast, efficient solution that maintains the material’s structural integrity and aesthetic qualities.
- Consumer Electronics: For consumer electronics, such as laptops, smartphones, and home appliances, laser welding aluminum provides precise, high-quality welds that contribute to the sleek designs and durability of these products.
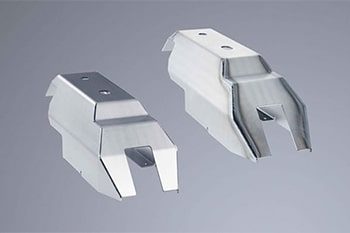
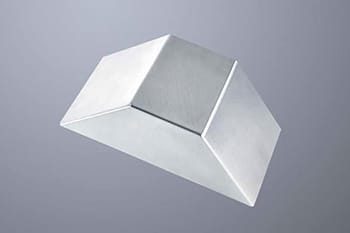
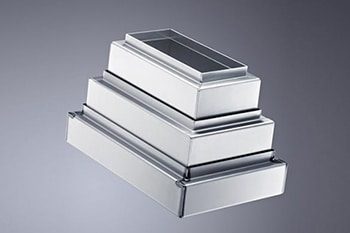
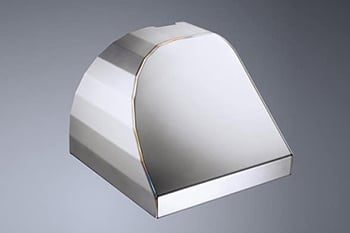
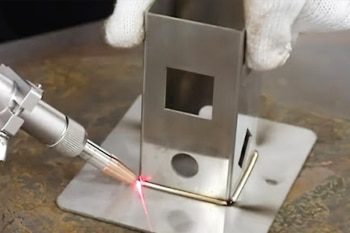

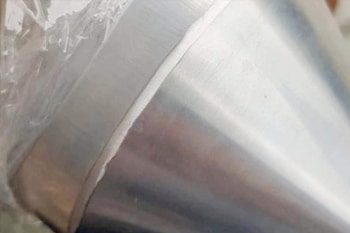
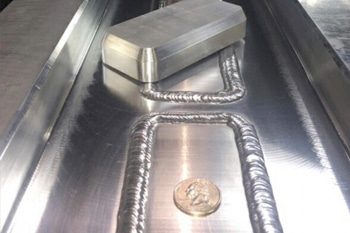
Customer Reviews
Frequently Asked Questions
Is laser welding suitable for aluminum materials?
What are the advantages of laser welding aluminum over traditional methods?
Can laser welding be used on all aluminum alloys?
What challenges are associated with laser welding aluminum?
The main challenges with laser welding aluminum are its high reflectivity and thermal conductivity. Aluminum reflects a significant amount of laser energy, making it harder for the laser to penetrate the surface. Additionally, aluminum’s high thermal conductivity can cause rapid heat dissipation, potentially leading to weaker welds. However, modern laser welding systems are equipped to handle these challenges by using higher-power lasers and precise control systems.