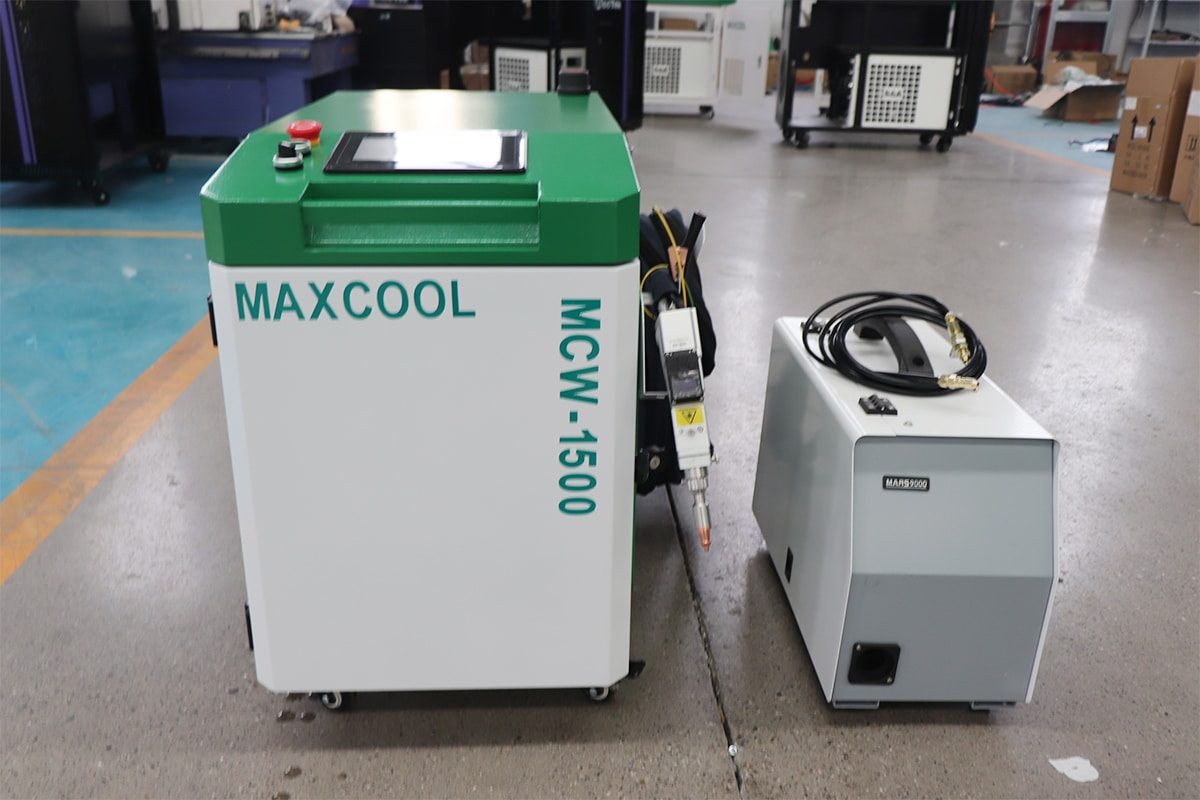
Laser Welding Machine Buying Guide
When considering purchasing a laser welding machine, understanding the intricacies of the technology can help you make an informed decision. Laser welding offers unparalleled precision and speed, making it a preferred choice for industries ranging from automotive to aerospace. This guide aims to delve into the critical factors you should evaluate, including machine specifications, types of lasers, power requirements, and application suitability. Whether you are a seasoned professional or a newcomer to laser technology, this comprehensive overview will help you navigate the various options available in the market. By focusing on essential features and practical considerations, you’ll be better equipped to choose a machine that not only meets your operational needs but also enhances your productivity and profitability. Prepare to unlock the ultimate potential of your manufacturing processes with the right laser welding solution.
Table of Contents
Understanding Laser Welding Technology
Laser welding is a revolutionary technique that employs focused laser beams to join materials, primarily metals, with remarkable precision and efficiency. This method has gained widespread popularity across various industries, owing to its ability to produce high-quality welds with minimal thermal distortion.
What is Laser Welding?
Laser welding utilizes a concentrated beam of light generated by a laser source, typically a fiber, CO2, or solid-state laser. The energy produced by the laser is directed onto the material, where it generates intense heat, allowing for the melting and fusion of the workpieces. This process is known for its speed and precision, making it ideal for applications that demand clean, strong joints with minimal surface imperfections. Laser welding is particularly effective for welding thin materials, complex geometries, and dissimilar metals, which are often challenging with traditional welding methods.
How Does Laser Welding Work?
The laser welding process begins with the generation of a focused laser beam that is directed through optical fibers or lenses to concentrate the energy onto the welding joint. When the beam hits the material, it rapidly heats the area to the melting point, creating a molten pool. As the laser moves along the seam, the molten pool solidifies upon cooling, forming a strong bond between the pieces.
Key parameters that influence the welding process include laser power, speed, and focus. Adjusting these parameters allows for customization based on the materials and thicknesses being welded. For example, higher power settings can increase the welding speed, while finer focus can improve penetration depth.
In addition to its efficiency, laser welding boasts benefits such as reduced heat-affected zones, lower energy consumption, and improved aesthetic quality of welds. As technology advances, laser welding continues to evolve, integrating features like real-time monitoring and automated control systems, making it an ultimate choice for modern manufacturing.
Types of Laser Welding Machines
Selecting the right type of laser welding machine can help optimize your production process and meet specific application requirements. Below are detailed descriptions of the three primary types of laser welding machines: handheld, automatic, and robotic.
Handheld Laser Welding Machines
Handheld laser welding machines offer unmatched flexibility and portability, making them ideal for a wide range of applications. These machines are designed for operators to maneuver the laser source manually, allowing for welding in tight spaces or on irregularly shaped components. Handheld systems are typically lightweight and easy to operate, enabling quick setups and adjustments on the fly. They are well-suited for small-scale production, maintenance, and repair work, where access to certain areas may be restricted. Additionally, their versatility makes them popular in industries such as automotive repair, metal fabrication, and artistic metalworking.
Automatic Laser Welding Machines
Automatic laser welding machines are engineered for high-speed, high-volume production environments. These machines utilize advanced automation to perform welding tasks with minimal human intervention. They are equipped with sophisticated software that controls the welding parameters, ensuring consistent quality and precision across multiple parts. Automatic systems are ideal for mass production, where uniformity and efficiency are critical. They often feature integrated conveyor systems for seamless part handling, enabling continuous operation and reduced cycle times. Industries that benefit from automatic laser welding include electronics manufacturing, automotive assembly, and aerospace component production.
Robotic Laser Welding Machines
Robotic laser welding machines combine the capabilities of robotic automation with advanced laser welding technology. These systems feature articulated robotic arms that can navigate complex welding paths with high precision, making them suitable for intricate assemblies and components. The integration of robotics allows for flexible production lines, where the same machine can be programmed to handle various welding tasks with ease. Robotic systems excel in applications requiring high repeatability and accuracy, such as in the automotive and aerospace industries. Furthermore, they can operate in challenging environments and manage heavy workloads, significantly increasing productivity while minimizing labor costs.
Each type of laser welding machine offers distinct advantages, and the choice will depend on your specific production needs, operational scale, and the materials being welded. Understanding these options will help you make an informed decision, ultimately enhancing the efficiency and quality of your welding processes.
Laser Welding Machine Features and Customizations
When selecting a laser welding machine, understanding the available features and customizations can significantly enhance productivity and efficiency in your operations. Below are key features that can elevate your welding capabilities:
4-in-1 Laser Welding Heads
The versatility of a 4-in-1 laser welding head allows operators to seamlessly transition between different welding techniques—spot, seam, stitch, and more—without the need for multiple machines. This feature is particularly beneficial for manufacturers handling diverse materials and varying thicknesses. With a single machine capable of performing various welding styles, you can optimize production workflows, reduce setup times, and minimize costs associated with maintaining multiple equipment types. The ability to adjust settings easily also helps ensure consistent quality across different projects.
Wobble Welding Mode
Wobble welding mode introduces an innovative approach to enhance weld quality, especially for thin materials prone to distortion. By oscillating the laser beam during the welding process, this mode distributes heat more evenly across the joint. This controlled movement creates a wider weld seam, reducing the risk of burn-through while improving joint strength and integrity. The result is cleaner, more robust welds, making this feature invaluable for applications where precision and aesthetics are crucial.
Remote Monitoring Systems
In today’s fast-paced manufacturing environment, remote monitoring systems provide a significant advantage by allowing operators to keep tabs on the welding process in real-time. These systems monitor crucial parameters such as temperature, welding speed, and laser power, offering instant alerts for any deviations from set conditions. This capability not only enhances operational efficiency but also facilitates preventive maintenance, helping to identify issues before they lead to costly downtime. With remote access, operators can troubleshoot and adjust settings from a distance, streamlining the production process.
Rotary Axis
For projects involving cylindrical components, the addition of a rotary axis is a game-changer. This feature enables the machine to rotate workpieces during the welding process, ensuring uniform heat application and consistent weld quality around the entire circumference of the part. The rotary axis is particularly beneficial for applications like pipe welding, where precision and evenness are essential. By integrating this customization, manufacturers can expand their capabilities to include a wider range of products, ultimately increasing their market competitiveness.
Incorporating these features and customizations into your laser welding machine can significantly improve performance, quality, and flexibility, making it easier to meet the demands of various industries and applications.
Applications of Laser Welding Machines
Laser welding machines are versatile tools used across various industries, thanks to their precision, efficiency, and ability to handle diverse materials. Below are detailed descriptions of key applications in different sectors:
Automotive Industry
In the automotive sector, laser welding plays a crucial role in the fabrication of lightweight and high-strength components. The technology is used for welding critical parts, including chassis, body panels, and exhaust systems. Laser welding’s speed and accuracy allow for the mass production of vehicles while maintaining stringent quality standards. Additionally, the ability to weld dissimilar materials, such as aluminum and steel, is essential for modern automotive design, enhancing fuel efficiency without compromising structural integrity.
Aerospace
The aerospace industry demands the highest levels of precision and reliability, making laser welding an ideal choice for manufacturing aircraft components. This technology is used for welding fuel tanks, structural frames, and various internal systems, where the strength and quality of welds are paramount. Laser welding minimizes thermal distortion, which is critical for maintaining the integrity of lightweight materials used in aerospace applications. Moreover, the ability to perform complex welds in hard-to-reach areas enhances production capabilities and safety.
Medical Device Manufacturing
In medical device manufacturing, laser welding is employed to create precise, clean, and biocompatible joints. Applications include welding components for surgical instruments, implants, and diagnostic equipment. The non-contact nature of laser welding reduces the risk of contamination, which is vital in the medical field. Furthermore, the ability to weld delicate and intricate components ensures the reliability and performance of medical devices, adhering to strict regulatory standards.
Electronics Industry
The electronics sector relies heavily on laser welding for assembling components such as circuit boards, connectors, and enclosures. Laser welding enables the precise joining of small, delicate parts without causing damage to sensitive electronics. Its capability to produce hermetic seals is particularly valuable in protecting electronic components from moisture and dust. The speed and efficiency of laser welding processes also help manufacturers keep pace with the rapid innovation cycles typical in the electronics market.
Jewelry Industry
In the jewelry industry, laser welding is used to create intricate designs and join precious metals with high precision. This technique allows artisans to work with small components, such as chains and settings, without compromising the aesthetics or structural integrity of the pieces. Laser welding also facilitates the repair of jewelry by providing strong, clean joints that preserve the original design. As consumer demand for customized jewelry increases, laser welding technology offers the flexibility needed for unique creations.
Laser welding machines are integral to various industries, providing the ultimate combination of speed, quality, and versatility that modern manufacturing demands.
Factors to Consider When Buying
When investing in a laser welding machine, careful consideration of various factors can ensure that the equipment selected meets your specific needs and operational goals. Below are critical aspects to evaluate before making a purchase:
Assessing Your Welding Needs
Understanding your specific welding requirements is the first step in selecting the right machine. Consider the types of projects you will undertake, including the size, complexity, and frequency of production runs. Identify whether you need a machine for small-scale, precision tasks or high-volume manufacturing. This assessment will help determine the necessary features, such as welding speed, versatility, and automation capabilities, guiding you toward a machine that aligns with your operational demands.
Material Compatibility
Different laser welding machines are designed to work with various materials, including steel, aluminum, titanium, and plastics. Assessing the types of materials you intend to weld is crucial, as compatibility affects both the quality of the weld and the machine’s performance. Ensure that the selected laser welding machine can handle the thickness and type of materials in your applications, including any potential need for welding dissimilar materials.
Required Power and Efficiency
The power of a laser welding machine directly impacts its performance and efficiency. Higher-wattage machines typically allow for faster welding speeds and deeper penetration, making them suitable for thicker materials. Consider the required power level based on your specific welding applications, and balance this with the need for energy efficiency. An efficient machine not only reduces operational costs but also minimizes environmental impact.
Budget Considerations and ROI
Establishing a budget for your laser welding machine purchase is vital. While it may be tempting to opt for the cheapest option, it’s important to weigh initial costs against long-term value. Consider factors such as maintenance costs, energy consumption, and potential downtime. Calculate the return on investment (ROI) by estimating how the new machine will enhance productivity, reduce labor costs, and improve product quality. A higher upfront investment in a reliable and efficient machine can lead to significant savings and improved profits over time.
Safety Features and Compliance
Safety should always be a top priority when selecting a laser welding machine. Look for machines equipped with safety features such as protective enclosures, emergency shut-off systems, and advanced cooling mechanisms. Additionally, ensure that the equipment complies with relevant industry standards and regulations to minimize risks to operators and the working environment. Investing in safety not only protects personnel but also contributes to a more efficient and compliant operation.
By carefully considering these factors, you can make an informed decision when purchasing a laser welding machine that meets your needs, enhances productivity, and ensures a safe working environment.
Key Factors to Consider When Buying a Laser Welding Machine
When investing in a laser welding machine, it’s essential to evaluate several key factors that will influence both the performance and suitability of the equipment for your specific applications. Below are the critical considerations to help guide your decision-making process:
Welding Speed Requirements
The speed at which a laser welding machine can operate is crucial, particularly for high-volume production environments. Assess your welding speed requirements based on the types of projects you will be handling. Faster machines can significantly improve productivity, but ensure that increased speed does not compromise weld quality. Evaluate the trade-offs between speed and precision to find a machine that meets your operational demands.
Power Output
The power output of a laser welding machine is a vital factor that affects its welding capabilities. Higher wattage generally allows for deeper penetration and the ability to weld thicker materials. Consider the power output needed based on the materials you plan to work with and the complexity of the welding tasks. Machines with adjustable power settings offer flexibility to accommodate a range of applications.
Precision and Accuracy
Laser welding is valued for its precision, which is especially important for intricate designs and critical components. Look for machines that provide consistent accuracy in weld placement and depth. Features such as advanced optics and control systems can enhance precision, making them essential for industries like aerospace and medical device manufacturing, where even minor discrepancies can lead to significant issues.
Material Compatibility
Not all laser welding machines are compatible with every type of material. Evaluate the range of materials you intend to weld, including various metals and composites. Ensure that the machine you select can handle the specific materials and thicknesses required for your projects, including any special considerations for dissimilar metal welding.
Automation Level
The level of automation in a laser welding machine can significantly impact efficiency and ease of use. Fully automated systems can enhance production rates and reduce labor costs, while semi-automated options may provide more flexibility for smaller runs or varied projects. Assess your production environment and determine the level of automation that aligns with your operational needs and workforce capabilities.
Portability
If your welding projects require movement between different locations or workstations, consider the portability of the laser welding machine. Handheld options offer excellent mobility, while larger, stationary machines may require dedicated space. Assess your workflow to determine whether a portable or stationary system would be more beneficial for your operations.
Cooling System
A reliable cooling system helps maintain optimal operating temperature and prevent overheating during extended use. Look for machines with efficient cooling mechanisms, such as water or air cooling, which can prolong the lifespan of the laser generator and enhance overall performance. Ensure that the cooling system aligns with your intended usage and production volume.
Safety Features
Safety is paramount when working with laser technology. Evaluate the safety features included in the machine, such as protective enclosures, emergency shut-off systems, and safety interlocks. Compliance with industry standards and regulations should also be a consideration, as these features help protect operators and prevent accidents in the workplace.
Maintenance Requirements
Regular maintenance is essential for keeping a laser welding machine in optimal condition. Consider the maintenance requirements of the machine, including the ease of access to components for cleaning and servicing. Machines designed for minimal maintenance may reduce downtime and operational costs in the long run.
Cost and Budget Considerations
Establish a clear budget for your laser welding machine purchase. While it may be tempting to opt for the lowest-cost option, consider the long-term value of the machine. Evaluate costs associated with maintenance, energy consumption, and potential downtime. A slightly higher investment in a reliable and efficient machine can yield substantial returns through improved productivity and reduced operational costs.
Brand Reputation and After-Sales Support
The reputation of the manufacturer and the availability of after-sales support can greatly influence your satisfaction with a laser welding machine. Research the brand’s history, customer reviews, and reputation for quality. Additionally, consider the level of technical support, warranty options, and availability of spare parts. Strong after-sales support ensures that you have assistance when needed, maximizing your investment and minimizing disruptions to your operations.
By carefully evaluating these factors, you can make an informed decision when purchasing a laser welding machine, ultimately enhancing your manufacturing processes and product quality.
Comparison with Traditional Welding Methods
When evaluating laser welding, it’s essential to compare it with traditional welding methods, such as MIG (Metal Inert Gas) welding, TIG (Tungsten Inert Gas) welding, and arc welding. Each method has its advantages and applications, but laser welding offers distinct benefits that can make it a superior choice for specific projects.
MIG Welding
MIG welding is a widely used process that employs a continuous wire feed as an electrode, which is melted to join materials. This method is known for its speed and efficiency, making it suitable for high-volume production. MIG welding can effectively handle thicker materials and is commonly used in automotive and manufacturing industries. However, it requires a shielding gas to protect the weld area, which can lead to additional costs and complexities. While MIG welding is versatile, it may not achieve the same level of precision as laser welding, especially for intricate designs or thin materials. Additionally, the heat-affected zone (HAZ) is larger in MIG welding, which can result in greater warping and distortion of the base materials.
TIG Welding
TIG welding is a process that uses a non-consumable tungsten electrode to produce a weld. This method is celebrated for its ability to create high-quality, precise welds on a variety of materials, including thin metals and exotic alloys. TIG welding offers excellent control over the weld pool and can produce aesthetically pleasing results. However, it is generally slower than MIG welding and requires more skill and experience from the operator. While TIG welding can achieve high levels of accuracy, it may struggle with production rates in high-volume environments compared to laser welding, which excels in both speed and precision.
Arc Welding
Arc welding encompasses several techniques, including shielded metal arc welding (SMAW) and gas metal arc welding (GMAW). This method uses an electric arc to melt and fuse materials, making it suitable for heavy-duty applications and thick materials. Arc welding is known for its robustness and versatility, but it often results in a larger heat-affected zone, which can lead to warping and structural integrity issues in sensitive applications. Additionally, arc welding can create more spatter and requires post-weld cleaning, which can increase overall project time and labor costs.
While traditional welding methods like MIG, TIG, and arc welding have proven effective for various applications, laser welding stands out for its precision, speed, and ability to weld delicate and thin materials with minimal distortion. The choice between these methods ultimately depends on the specific requirements of your project, including material type, thickness, desired weld quality, and production volume. Understanding these differences can help you make an informed decision when selecting a welding solution that best fits your needs.
Steps to Purchasing the Right Laser Welding Machine
Purchasing a laser welding machine is a significant investment that requires careful consideration and planning. Following a structured approach can help ensure that you select the right machine to meet your operational needs. Here are the essential steps to guide you through the purchasing process:
Assessing Your Welding Needs
Begin by thoroughly evaluating your specific welding requirements. Consider the types of materials you will be working with, the thickness of those materials, and the complexity of the welds needed for your applications. Additionally, assess the production volume you anticipate and any specific quality standards that must be met. This initial assessment will help you identify the features and capabilities that are essential for your laser welding machine.
Consulting with Manufacturers
Once you have a clear understanding of your needs, reach out to manufacturers and suppliers of laser welding machines. Engaging in discussions with experts can provide valuable insights into the latest technologies and trends in the market. Inquire about different models, specifications, and any relevant industry applications. Manufacturers can also help you understand the advantages of their machines and how they align with your operational goals.
Testing and Demonstrations
Before making a final decision, it is crucial to test the machines you are considering. Request demonstrations from manufacturers to see the equipment in action. This hands-on experience allows you to evaluate the machine’s performance, ease of use, and how well it meets your specific welding requirements. Pay attention to factors such as welding speed, precision, and the quality of the welds produced. If possible, bring your materials for testing to gauge the machine’s compatibility with your typical workload.
Evaluating the Total Cost of Ownership
When considering the purchase, look beyond the initial price tag to evaluate the total cost of ownership (TCO). This includes not only the purchase price but also factors such as energy consumption, maintenance costs, and potential downtime. Assess the warranty and support services offered by the manufacturer, as these can significantly affect long-term expenses. A more expensive machine may offer greater efficiency and lower operating costs over time, making it a more economical choice in the long run.
Considering Customization Options
Finally, explore the customization options available for the laser welding machine. Depending on your specific needs, you may require certain features, such as additional welding heads, automation capabilities, or specialized software. Discuss these options with manufacturers to ensure that the machine you choose can be tailored to suit your operational requirements. Customization can enhance productivity and efficiency, ensuring that the machine aligns perfectly with your processes.
By following these steps, you can make a well-informed decision when purchasing a laser welding machine, ultimately leading to improved performance and productivity in your operations.
Summary
Selecting the right laser welding machine is a critical decision that can significantly impact your manufacturing processes and overall productivity. By thoroughly assessing your welding needs, consulting with manufacturers, and understanding the various types of machines available, you can make an informed choice that aligns with your operational goals. Consider essential factors such as welding speed, power output, material compatibility, and automation levels to ensure the equipment meets your specific requirements. Testing and evaluating the total cost of ownership will further enhance your decision-making process, helping you identify the best value for your investment. With the right laser welding machine, you can achieve superior precision, efficiency, and flexibility in your operations, ultimately driving better outcomes and enhanced profitability for your business. Embracing advanced laser technology positions you to meet the demands of a competitive market while ensuring high-quality results across diverse applications.
Get Laser Solutions
When it comes to optimizing your welding operations, choosing the right laser solution is paramount. At Maxcool CNC, we specialize in providing cutting-edge laser welding machines tailored to meet diverse industrial needs. Our range of machines offers unparalleled precision, speed, and versatility, allowing you to handle everything from intricate designs to high-volume production. Our team of experts is dedicated to understanding your specific requirements and guiding you through the selection process to ensure you find the perfect fit for your applications. We also offer customization options to enhance the capabilities of our machines, ensuring they align perfectly with your operational goals. Additionally, our comprehensive after-sales support ensures that you can maximize the performance and longevity of your investment. Discover the advantages of laser technology with Maxcool CNC and elevate your manufacturing processes to new heights of efficiency and quality. Contact us today to explore our innovative laser solutions!