Product Introduction
Types of Fiber Laser Cutting Machines
-
AKJ-FR Laser Cutting Machine
Rated 5.00 out of 5$32,000.00 – $180,000.00 This product has multiple variants. The options may be chosen on the product page -
AKJ-FCR Laser Cutting Machine
Rated 4.75 out of 5$36,500.00 – $189,000.00 This product has multiple variants. The options may be chosen on the product page -
AKJ-FBCR Laser Cutting Machine
Rated 4.75 out of 5$41,500.00 – $200,000.00 This product has multiple variants. The options may be chosen on the product page
Application of Fiber Laser Cutting Machines
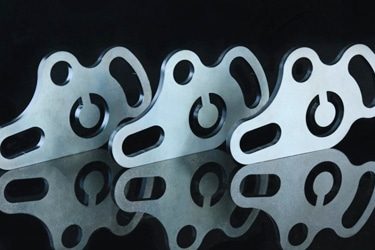
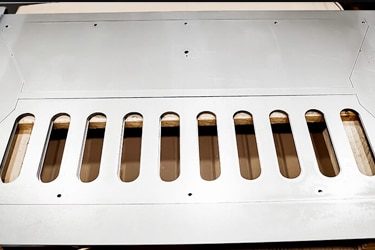
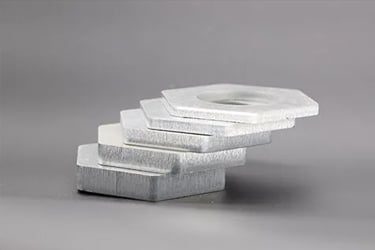
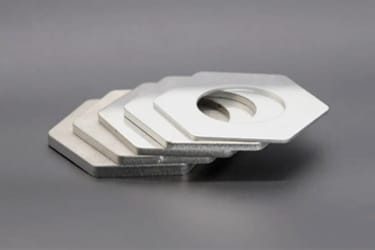
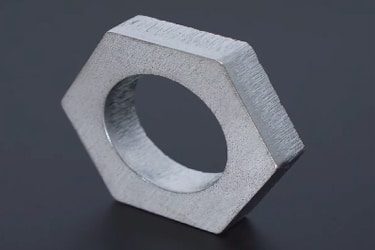
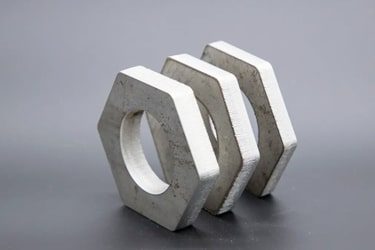
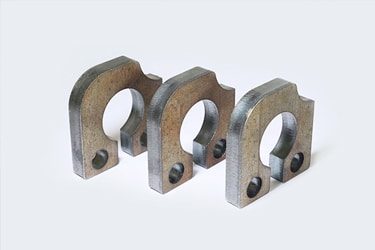
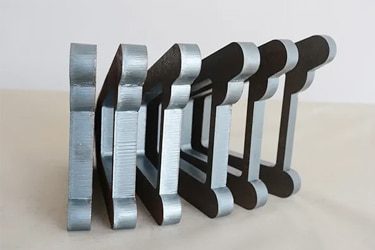
Customer Testimonials
Fiber Laser Cutting Machine VS Other Cutting Machines
Comparison Item | Fiber Laser Cutting Machine | Plasma Cutting Machine | Waterjet Cutting Machine | Mechanical Cutting Machine |
Suitable Materials | Metals (steel, aluminum, brass, copper) | Metals (especially thick plates) | Almost all materials (metal, stone, glass, plastic) | Metals, wood, plastics (depending on tool) |
Cutting Speed | Very fast on thin to medium metal | Fast on thick metals | Slower due to the water pressure process | Moderate, depends on material and tool type |
Edge Quality | Clean, smooth, minimal burr | Rougher edges, needs finishing | Smooth, no heat-affected zone | May require post-processing |
Precision | Very high | Moderate | High | Lower, depends on tool wear |
Thickness Capability | Excellent on thin to medium sheets | Very good for thick metals | Excellent for very thick materials | Limited by tool strength and machine power |
Reflective Material Cutting | Excellent | Good | Excellent | Good |
Operating Cost | Low (efficient and low maintenance) | High (consumables, energy use) | High (abrasives, water use, maintenance) | Low to moderate |
Maintenance Requirements | Low | High (frequent consumable changes) | High (pump, nozzles, filters) | Varies (tools wear out, may need regular replacement) |
Heat-Affected Zone (HAZ) | Very small | Large | None | Medium (friction heat) |
Environmental Impact | Low (no fumes if filtered properly) | High (smoke, fumes) | High (water, abrasive waste) | Low |
Automation Integration | Easy (CNC and software compatible) | Moderate | Moderate | Harder to automate |
Typical Applications | Metal parts, enclosures, precision components | Heavy steel parts, construction components | Stone counters, thick metal parts, fragile materials | Basic cutting, general manufacturing |
Why Choose Us
Advanced Technology
Our laser cutting machines feature high-speed, precision cutting with the latest laser technology, ensuring smooth edges, minimal waste, and superior efficiency across various materials and thicknesses.
Reliable Quality
Each machine undergoes rigorous quality control and durability testing to ensure long-term stability, low maintenance, and consistent high performance, even under demanding industrial conditions.
Comprehensive Support
We provide full technical support, including installation guidance, operator training, and after-sales service, ensuring smooth machine operation and minimal downtime for your business.
Cost-Effective Solutions
Our machines offer high performance at competitive prices, with customizable options to fit different production needs, helping businesses maximize their investment without compromising on quality.
Related Resources
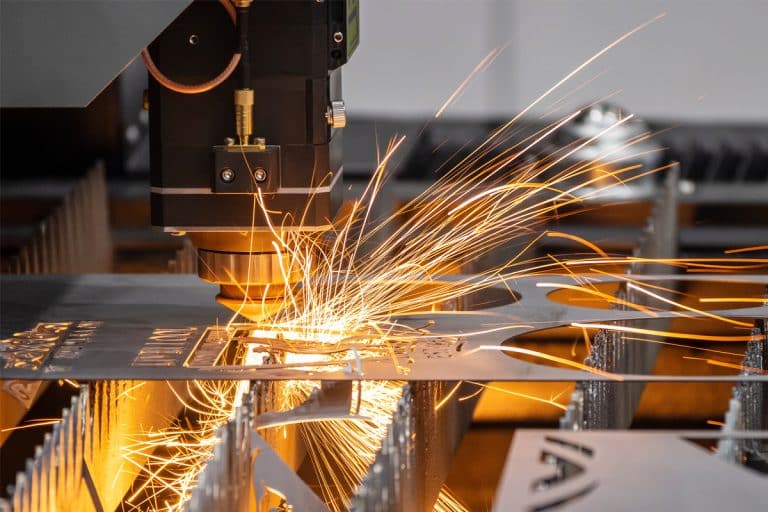
What Is Laser Cutting?
Discover the fundamentals of laser cutting, its process, types, applications, and benefits. Learn how this advanced technology is transforming modern manufacturing.
Frequently Asked Questions
What Power Options Are Available For Fiber Laser Cutting Machines?
- Low to Mid Power
- 1500W: Great for cutting thin metals like carbon steel (up to ~6mm), stainless steel, and aluminum. Ideal for small shops or light production work.
- 2000W – 3000W: A popular range for general metal fabrication. Can cut thicker materials (carbon steel up to ~16mm) while offering faster speeds and better edge quality.
- 4000W: Handles moderate thicknesses with increased speed and stability. Often used in mid-sized production settings.
- High Power
- 6000W: Can cut thick sheets (carbon steel up to ~25mm) efficiently. Useful for medium to heavy industrial workloads.
- 12000W: High-speed cutting of thick materials (up to 30mm+), with clean edges and excellent productivity. Suitable for companies with demanding throughput.
- Ultra-High Power
- 20000W – 30000W – 40000W: Designed for heavy industry. Cuts very thick metal (up to 50mm+), including stainless steel, carbon steel, and aluminum. These machines are used where speed, precision, and volume matter most—like shipbuilding, aerospace, or large-scale manufacturing.
What Auxiliary Equipment Is Required For Fiber Laser Cutting Machines?
- Chiller (Water Cooling System): Fiber laser sources generate heat during operation. A water chiller keeps the laser source and optics at a stable temperature, preventing overheating and extending component life.
- Air Compressor: Compressed air is used as an assist gas for cutting, especially with thin metals. It helps blow away molten material and improves edge quality. It’s also useful for purging and cleaning inside the machine.
- Air Dryer and Filter: Moisture and oil in compressed air can damage the laser head and optics. An air dryer and filtration system remove contaminants, ensuring clean, dry air reaches the machine.
- Dust and Fume Extractor: Cutting metals releases smoke, fine dust, and sometimes harmful particles. A fume extraction system or dust collector is critical for maintaining air quality and protecting both operators and machine components.
- Voltage Stabilizer or UPS: Stable voltage is crucial for fiber laser machines. A voltage stabilizer or uninterruptible power supply (UPS) protects against power fluctuations that could damage sensitive electronics.
- Gas Supply System: Depending on the material, you will need a tank or centralized system to supply nitrogen, oxygen, or compressed air. You will also need the appropriate regulators, valves, and hoses to ensure safe, steady gas flow.
- Computer and Software: A dedicated control computer and compatible CAD/CAM software are essential for preparing and sending cutting files to the machine. Often, this includes nesting software for efficient layout planning.
- Material Handling Tools: Optional but useful—loading/unloading tables, conveyors, or automatic pallet changers can improve workflow, especially in high-volume operations.
What Gases Are Required For Fiber Laser Cutting?
- Nitrogen (N2)
- Used for: Stainless steel, aluminum, galvanized steel, and other non-ferrous metals.
- Purpose: Creates clean, oxidation-free cuts.
- How it works: Nitrogen is inert, so it doesn’t react with the material. This results in smooth edges without discoloration.
- Common in: High-precision or cosmetic parts, like electronics, signage, or food-grade components.
- Oxygen (O2)
- Used for: Mild steel, carbon steel.
- Purpose: Boosts cutting speed and helps cut thicker steel.
- How it works: Oxygen reacts with the metal (oxidation), adding heat to the cutting zone. This speeds up cutting but leaves an oxidized edge.
- Common in: Structural parts, industrial applications where edge quality isn’t a top priority.
- Compressed Air
- Used for: Mild steel, stainless steel, aluminum (mostly thin sheets).
- Purpose: A cost-effective option for general cutting.
- How it works: Blows away molten material. It’s not as clean as nitrogen but cheaper and sufficient for many tasks.
- Common in: Budget-friendly operations, light fabrication, and shops cutting thinner metals.
What Are The Working Environment Requirements For Fiber Laser Cutting Machines?
- Temperature and Humidity
- Temperature Range: Ideally 15℃ to 30℃ (59℉ to 86℉). Avoid extreme cold or heat, as it can affect the laser source and electronics.
- Humidity: Keep it below 70% and avoid condensation. Moisture can damage optics, electronics, and internal components.
- Clean, Dust-Free Space
- Dust and metal particles can interfere with the laser optics and cause wear on mechanical parts.
- Use the machine in a well-ventilated, clean room, ideally with dust control or air filtration systems.
- Stable Power Supply
- Fiber lasers are sensitive to voltage fluctuations. Use a voltage stabilizer or uninterruptible power supply (UPS) to protect the machine from power surges or outages.
- Good Ventilation and Fume Extraction
- Cutting produces smoke, fumes, and fine particles, especially from metals or coated materials.
- A proper fume extraction system is critical to maintain air quality and protect operators.
- Flat, Vibration-Free Floor
- The machine should sit on a stable, level surface to ensure precision and prevent misalignment.
- Avoid areas with heavy vibrations from nearby equipment or vehicles.
- Space Around the Machine
- Leave enough clearance on all sides for loading materials, maintenance, and airflow.
- This also improves safety and accessibility.
- Restricted Access and Safety Measures
- Only trained personnel should operate the machine.
- Install safety guards, emergency stop buttons, and warning signs around the work area.
What Are The Site Requirements For Fiber Laser Cutting Machines?
- Sufficient Space
- Ensure there’s ample room around the machine for loading/unloading materials, maintenance access, and operator movement.
- Space is also needed for auxiliary equipment like chillers, gas tanks, air compressors, and fume extractors.
- For larger machines, allow at least 1–2 meters of clearance on all sides.
- Stable, Level Floor
- The floor must be flat, vibration-free, and able to support the weight of the machine and its components (often several tons).
- Reinforced concrete floors are ideal, especially for industrial models.
- Power Supply
- Fiber lasers require a stable, high-capacity power source.
- Typical setups use three-phase power (e.g., 380V, 50/60Hz), depending on machine size.
- Install a voltage stabilizer or UPS to protect electronics from fluctuations.
- Ventilation and Exhaust
- A proper fume extraction and ventilation system is mandatory.
- Ducting should lead fumes and dust out of the building or through a filtration system.
- This protects air quality and complies with workplace safety standards.
- Gas Supply System
- Set up safe storage for nitrogen, oxygen, or compressed air, depending on your cutting needs.
- Install regulators, hoses, and shut-off valves in line with local gas safety codes.
- Store gas cylinders in a well-ventilated, secure area—ideally outside the cutting room.
- Cooling System Setup
- Make room for a water chiller near the machine.
- It should be easy to access for refilling, maintenance, and temperature monitoring.
- Environmental Controls
- Ideal ambient temperature: 15°C–30°C (59°F–86°F)
- Humidity: <70%, with no condensation
- Avoid direct sunlight, dust-heavy areas, or locations near other high-vibration machinery.
- Network and Computer Access
- You’ll need a computer workstation nearby for design files and machine control.
- Reliable network or USB connections help with file transfers and software updates.
How To Maintain Fiber Laser Cutting Machines?
- Clean the Lens and Nozzle Regularly: These parts are directly exposed to sparks, smoke, and metal particles. A dirty or damaged lens can reduce cutting accuracy, and a clogged nozzle can mess with gas flow. Wipe them down daily using proper lens cleaner and replace them when worn.
- Keep the Cutting Bed and Work Area Clean: After each job, clear out slag, scraps, and dust. Debris can affect sheet alignment and reduce cutting precision. A tidy workspace also makes spotting problems easier.
- Check the Cooling System: Fiber lasers use water chillers to stay at safe operating temperatures. Make sure the chiller has enough clean, distilled water. Flush and refill it on a regular schedule, and clean the filters to avoid buildup that can block flow.
- Lubricate Mechanical Components: Moving parts like guide rails and bearings need proper lubrication. Use the recommended grease, and clean the surfaces before applying it. This helps prevent wear and keeps the motion system running smoothly.
- Inspect Gas Supply and Filters: Whether you’re using nitrogen, oxygen, or compressed air, make sure your gas lines are leak-free and your regulators and filters are clean. Contaminated or low-pressure gas can lead to poor cut quality.
- Check Alignment and Focus: Over time, vibrations or daily use can throw off the alignment of the cutting head or the focus point of the laser. Run test cuts and make adjustments if accuracy seems off.
- Maintain Electrical Components: Turn off the machine and inspect wiring, connectors, and control panels for wear, corrosion, or loose parts. Catching small issues early helps prevent bigger failures later.
- Update Software and Firmware: Manufacturers often release updates that fix bugs or improve cutting performance. Keep your machine’s software up to date and back up important settings before making changes.
What Is The Service Life Of Fiber Laser Cutting Machines?
How To Handle Fumes During Fiber Laser Cutting?
- Install Fume Extraction Systems: This is your first line of defense. A proper system captures smoke, metal dust, and harmful gases right at the source—usually near the cutting head. It then filters the air through HEPA and carbon filters or vents it safely outside the building.
- Make Sure Your Workspace is Well-Ventilated: Even with extraction, fresh air flow helps keep the environment safe. If you’re in a closed room, ensure there’s intake ventilation bringing clean air in and not just exhaust pulling air out.
- Use Safe Materials: Some materials release highly toxic fumes when cut, like PVC (which emits chlorine gas) or painted/coated metals with unknown chemicals. Always check the material’s data sheet before cutting and avoid anything that could emit dangerous gases.
- Maintain the Filters: Fume extractors work only if the filters are clean. Replace them as needed—especially carbon filters, which lose effectiveness over time even if they don’t look dirty.
- Clean Your Machine Regularly: Dust, soot, and metal residue can build up inside the machine and recirculate harmful particles if left unchecked. Wipe down surfaces and vacuum the cutting bed after use.
- Train Your Operators: Everyone using the machine should know how to turn on the exhaust system, recognize when it’s underperforming, and understand the risks of improper ventilation.