Product Introduction
Types of Laser Cutting Machines
-
Dual Beam Mixed Laser Cutting Machine
Rated 5.00 out of 5$20,700.00 – $45,500.00 This product has multiple variants. The options may be chosen on the product page
Application of Laser Cutting Machines
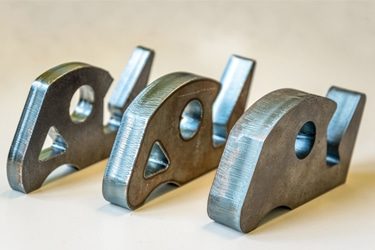
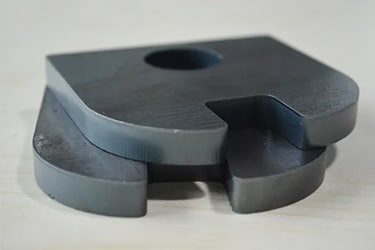
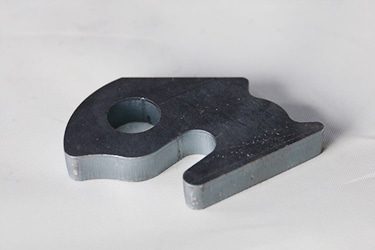
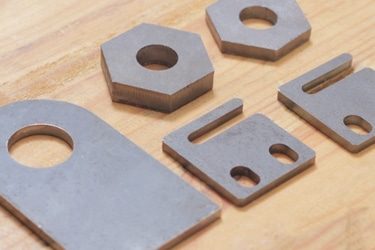
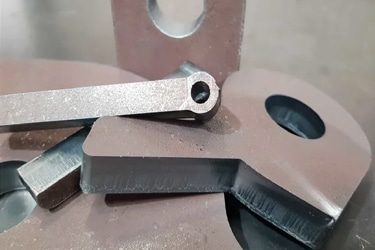
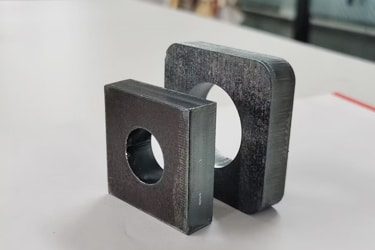
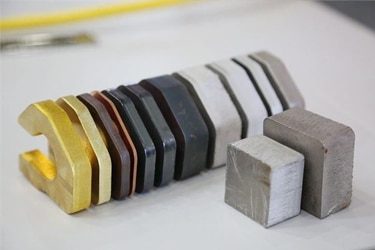
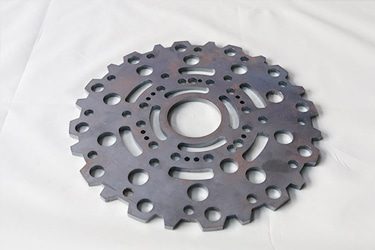
Customer Testimonials
Laser Cutting Machine VS Other Cutting Machines
Comparison Item | Laser Cutting Machine | Plasma Cutting Machine | Waterjet Cutting Machine | Mechanical Cutting Machine |
---|---|---|---|---|
Cutting Precision | Very high, ideal for detailed work | Moderate, good for thicker parts | High, especially for delicate materials | Low to moderate, limited detail |
Edge Quality | Smooth, clean edges, minimal finishing | Rougher, often needs grinding | Excellent, no heat-affected zone | Often rough, requires secondary processing |
Cutting Speed | Fast, especially on thin to medium metals | Fast on thick metals | Slower, especially on thick materials | Moderate, depends on material |
Heat-Affected Zone | Minimal | Large | None | Medium |
Material Compatibility | Metals, plastics, acrylic, wood, leather | Primarily metals | Almost all materials including stone, glass | Mostly metals, some plastics |
Operating Cost | Low (fiber), Medium (CO2, mixed) | Medium – gas & consumables | High – water, abrasive, energy | Low to medium – tool wear |
Maintenance Needs | Low (fiber), Regular (CO2, mixed) | Moderate – electrode and nozzle wear | High – pump, nozzle, abrasive | Moderate – blades or bits wear |
Noise Level | Low | High | High | High |
Cleanliness | Clean process, low dust and debris | Produces sparks and fumes | Creates slurry and wastewater | Chips and dust generated |
Automation Ready | Fully compatible with CNC and smart systems | CNC compatible | CNC compatible | Limited automation options |
Accuracy Over Time | Very stable and consistent | Less consistent due to wear | High but dependent on maintenance | Decreases with mechanical wear |
Ideal Applications | Precision parts, signage, metal & non-metal | Heavy-duty metal fabrication | Heat-sensitive materials, thick materials | Basic metal cutting, low-cost tasks |
Why Choose Us
Advanced Technology
Our laser cutting machines feature high-speed, precision cutting with the latest laser technology, ensuring smooth edges, minimal waste, and superior efficiency across various materials and thicknesses.
Reliable Quality
Each machine undergoes rigorous quality control and durability testing to ensure long-term stability, low maintenance, and consistent high performance, even under demanding industrial conditions.
Comprehensive Support
We provide full technical support, including installation guidance, operator training, and after-sales service, ensuring smooth machine operation and minimal downtime for your business.
Cost-Effective Solutions
Our machines offer high performance at competitive prices, with customizable options to fit different production needs, helping businesses maximize their investment without compromising on quality.
Related Resources
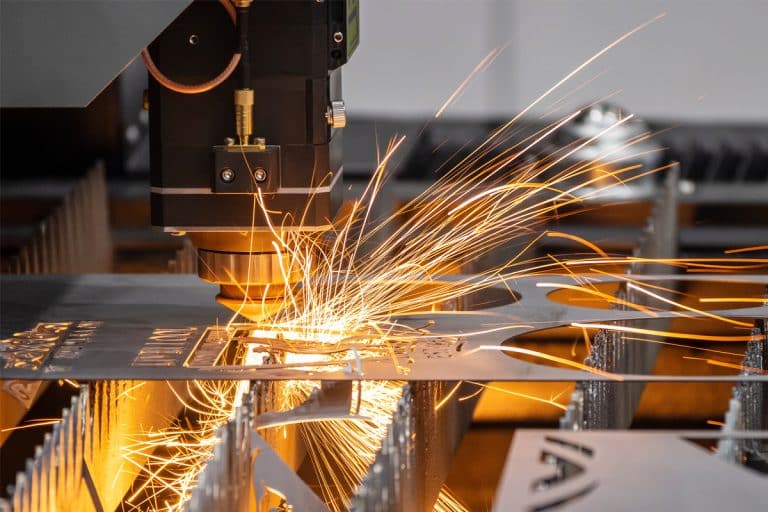
What Is Laser Cutting?
Discover the fundamentals of laser cutting, its process, types, applications, and benefits. Learn how this advanced technology is transforming modern manufacturing.
Frequently Asked Questions
How Much Does Laser-Cutting Machines Cost?
- Fiber Laser Cutting Machines (for metals): $15,000 -$500,000+. These are the most expensive due to their precision, speed, and ability to cut thick metals like stainless steel and aluminum.
- CO2 Laser Cutting Machines (for non-metals): $3,000 -$50,000. Ideal for cutting and engraving wood, acrylic, leather, and plastics. More affordable, especially for small businesses or hobby use.
- Mixed Laser Cutting Machines (for metal and non-metal): $17,000 -$50,000. Versatile but generally not as powerful or efficient as specialized machines. Best for shops that need flexibility on a budget.
What Should I Know Before Buying Laser-Cutting Machines?
- Material Type and Thickness: Know what materials you’ll be cutting—metal, non-metal, or both. CO2 lasers are ideal for wood, acrylic, plastic, and leather. Fiber lasers are best for metals. Mixed machines handle both but are limited in metal thickness. Match the machine type and power to your materials.
- Laser Power: Higher wattage means faster cuts and the ability to cut thicker materials. For example, 150W CO2 can cut thick acrylic, while 3000W fiber can handle moderate-thickness metals. Don’t overpay for power you won’t use—but don’t go underpowered either.
- Bed Size and Work Area: Choose a machine with a bed large enough to fit your typical workpieces. A bigger bed means more flexibility, but takes up more space and increases cost. Also, check whether it supports pass-through for oversized materials.
- Budget and Total Cost: Look beyond the machine price. Factor in installation, training, maintenance, replacement parts (like lenses or tubes), gas supply (for metal cutting), software licenses, and energy consumption. Buying too cheaply can lead to limited performance and more repairs.
- Software and Compatibility: Make sure the machine includes or supports software that’s compatible with your design workflow (like CorelDRAW, AutoCAD, or LightBurn). Easy-to-use software can speed up production and reduce mistakes.
- Maintenance and Support: Ask about the maintenance requirements and what support the manufacturer or reseller provides. A good supplier should offer training, tech support, and quick parts replacement. Fiber lasers require less frequent maintenance than CO2 systems, but both need care.
- Safety Features: Check for safety options like protective enclosures, emergency stop buttons, fume extraction, and laser-rated viewing windows. Cutting materials like plastics or metals can release harmful fumes, so proper ventilation is a must.
- Space and Power Requirements: Make sure your workspace can handle the machine’s size, weight, ventilation needs, and electrical load. Some machines require 3-phase power and dedicated cooling systems.
- Intended Use and Production Volume: For hobby use, a lower-cost machine might work fine. For business or industrial use, invest in something durable, reliable, and fast enough to meet demand without constant downtime.
- Reputation and Reviews: Research the brand, read user reviews, and ask other users in your industry. A proven track record is a good indicator of reliability and post-sale support.
What Are The Disadvantages of Laser-Cutting Machines?
- High Initial Cost: Especially for industrial-grade or high-powered fiber lasers.
- Material Limitations: Not all lasers can cut all materials; each type has its range.
- Ongoing Maintenance: Regular cleaning, part replacement, and system checks are essential.
- Toxic Fumes: Certain materials release hazardous gases when cut, requiring proper ventilation.
- Energy Consumption: Higher-powered machines draw significant power.
- Safety Risks: Improper use can lead to injuries or fire hazards.
- Training required: Operators must be skilled in both software and hardware use.
- Space and Infrastructure Needs: Larger machines require more room and sometimes special electrical setups.
- Slower Cutting for Thick Materials: Not ideal for very thick metal compared to plasma or flame cutting.
- Learning Curve: Choosing, setting up, and running the machine effectively takes time and experience.
How Thick Can Laser-Cutting Machines Cut?
- Fiber Laser Cutting Machines (for metals)
- Mild Steel: Up to 25-50 mm, depending on power (e.g., 12kW-40kW machines)
- Stainless Steel: Up to 30 mm with high-power lasers
- Aluminum: Up to 30 mm, though cutting quality may decrease with thickness
- Brass/Copper: Up to 10-15 mm, with powerful machines and proper gas assist
- CO2 Laser Cutting Machines (for non-metals)
- Acrylic: Up to 30-40 mm (with high power like 300W+)
- Wood/MDF: Up to 20-25 mm, depending on density and moisture
- Leather/Fabric/Paper: Thin materials, usually under 10 mm, cut very easily
- Plastic (non-toxic types): Up to 20-25 mm, depending on type
- Mixed Laser Cutting Machines (metal + non-metal)
- Thin Metal (carbon or stainless steel): Typically up to 1.5-3 mm
- Non-Metals: Similar to CO2 laser capabilities—up to 20-30 mm, depending on power
What Is The Power Consumption of Laser-Cutting Machines?
- Fiber Laser Cutting Machine
- More energy-efficient than CO2 lasers.
- 1kW Fiber Laser: 4-6 kW per hour
- 3kW Fiber Laser: 10-12 kW per hour
- 6kW Fiber Laser: 18-22 kW per hour
- 12kW+ Fiber Laser: 36-180 kW per hour
- Efficiency: 30-40%, meaning more power is converted into cutting energy.
- CO2 Laser Cutting Machine
- Higher power consumption due to lower efficiency.
- 100W CO2 Laser: 1-1.5 kW per hour
- 200W CO2 Laser: 2-3 kW per hour
- 300W CO2 Laser: 3-4.5 kW per hour
- Efficiency: 10-15%, requiring more electricity to achieve the same cutting results.
- Additional cooling systems increase power usage.
- Mixed Laser Cutting Machine
- Consumes moderate power compared to fiber and CO2 lasers.
- Medium Power Systems: 5-10 kW per hour
- High Power Models: 15-20 kW per hour
- Additional Power Consumption Factors
- Cooling Systems (Chillers): 2-10 kW per hour
- Exhaust and Air Filtration Systems: 5-10 kW per hour
- CNC and Motion Control Systems: 1-10 kW per hour
- Total Estimated Power Consumption Per Hour (Including Additional Systems)
- 1kW Fiber Laser: 8-10 kW
- 3kW Fiber Laser: 18-20 kW
- 6kW Fiber Laser: 32-35 kW
- 12kW+ Fiber Laser: 60-260 kW
- 100W CO2 Laser: 3-5 kW
- 200W CO2 Laser: 6-8 kW
- 300W CO2 Laser: 10-15 kW
Why Are Laser-Cutting Machines So Expensive?
- Advanced Laser Sources: The laser generator (especially fiber or high-powered CO₂ lasers) is one of the most costly parts. It requires precise engineering, stable performance, and long service life, which drives up cost.
- High-Precision Components: Laser cutters include motion control systems, cutting heads, lenses, and mirrors that must operate with extreme accuracy. These parts are built for speed and precision, and their quality directly impacts performance.
- Automation and Software: Modern laser machines use advanced CNC controllers and software for nesting, design, and real-time adjustments. This software is critical for maximizing efficiency and minimizing waste, but it adds to the cost.
- Structural Build Quality: The machine frame, gantry, and working bed must be extremely stable to avoid vibration and distortion during cutting. Industrial-grade construction increases durability but also cost.
- Support Systems: Laser machines often require water chillers, air compressors, fume extractors, and voltage stabilizers. These add both functionality and price to the overall setup.
- Safety and Compliance: Built-in safety systems—like enclosures, emergency stops, interlocks, and fume control—are required to meet international safety standards, and they increase manufacturing complexity and cost.
- Research and Development: Manufacturers invest heavily in R&D to improve cutting speed, reduce energy use, and extend machine life. This development cost is factored into the price.
- Brand and Service Support: Well-known brands charge more because they offer proven performance, better customer service, warranties, and global support networks.
What Are The Hazards of Laser-Cutting Machines?
- Eye and Skin Damage: Laser beams can cause serious eye injuries, including permanent vision loss, if viewed directly or through reflections. High-powered lasers can also burn skin on contact. Proper protective gear and enclosures are essential.
- Fire Risk: The laser beam generates intense heat, making flammable materials (like wood, acrylic, or paper) a fire hazard. Improper ventilation, residue buildup, or unattended operation increases the risk.
- Toxic Fumes and Gases: Cutting certain materials—especially plastics like PVC, coated metals, or synthetic fabrics—can release harmful fumes such as chlorine, formaldehyde, or other volatile organic compounds (VOCs). Inhalation is dangerous without proper fume extraction.
- Electrical Hazards: Laser machines use high-voltage power supplies. Faulty wiring, poor grounding, or improper maintenance can lead to electric shock or fire.
- Mechanical Injuries: Moving parts, such as the gantry or auto-feed systems, can cause crush injuries or lacerations if safety guards or sensors are bypassed.
- Gas Cylinder Risks: If you’re using assist gases like oxygen or nitrogen, improper handling or storage of gas cylinders can lead to leaks, explosions, or asphyxiation in enclosed spaces.
- Noise and Vibration: High-speed cutting or compressed air systems can generate noise levels that may damage hearing over time. Vibrations can also lead to fatigue or operational errors if the machine isn’t securely installed.
- UV and Infrared Radiation: In some cases, especially with high-powered lasers, secondary radiation exposure can pose health risks over time if proper shielding isn’t used.
What Is The Operating Cost of Laser-Cutting Machines?
- Electricity
- Fiber lasers are more energy-efficient than CO2 lasers.
- A mid-range fiber laser (e.g. 3kW–6kW) typically consumes 6–15 kWh, costing $1–$3 per hour (depending on local rates).
- CO2 lasers, especially higher-power models, use more electricity due to less efficient power conversion and cooling needs, costing $2–$5 per hour.
- Assist Gas
- Nitrogen and oxygen are commonly used for metal cutting.
- Nitrogen is more expensive and used in higher volumes for clean, oxidation-free cuts.
- Typical gas costs range from $1 to $10+ per hour, depending on material thickness and flow rate.
- Compressed air is a cheaper alternative for some applications.
- Consumables
- Includes nozzles, lenses, protective windows, and filters.
- Wear and replacement frequency depend on cutting intensity and maintenance.
- Average cost: $0.50 to $2 per hour.
- Maintenance
- Regular maintenance is needed for moving parts, cooling systems, optics, and dust collection.
- Estimated cost: $0.50 to $1.50 per hour, averaged over time.
- Labor
- Operator wages vary by region and skill level.
- In many workshops, labor costs are a major factor, ranging from $15 to $50 per hour if included.