Laser Cleaning Oil and Grease
Laser Oil and Grease Cleaning Machines
-
Standard Continuous Laser Cleaning Machine
Rated 4.75 out of 5$3,300.00 – $7,000.00 This product has multiple variants. The options may be chosen on the product page -
Portable Continuous Laser Cleaning Machine
Rated 4.50 out of 5$3,200.00 – $6,900.00 This product has multiple variants. The options may be chosen on the product page -
Double Wobble Pulse Laser Cleaning Machine
Rated 4.75 out of 5$5,600.00 – $7,300.00 This product has multiple variants. The options may be chosen on the product page -
Luggage Pulse Laser Cleaning Machine
Rated 5.00 out of 5$6,300.00 – $8,600.00 This product has multiple variants. The options may be chosen on the product page -
Backpack Pulse Laser Cleaning Machine
Rated 4.75 out of 5$6,300.00 – $8,600.00 This product has multiple variants. The options may be chosen on the product page -
High Power Pulse Laser Cleaning Machine
Rated 4.75 out of 5$9,600.00 – $30,200.00 This product has multiple variants. The options may be chosen on the product page -
Double Wobble Continuous Laser Cleaning Machine
Rated 5.00 out of 5$3,800.00 – $7,500.00 This product has multiple variants. The options may be chosen on the product page
Benefits of Laser Oil and Grease Cleaning
High Efficiency
Laser cleaning swiftly removes oil and grease, offering a rapid solution that reduces downtime and enhances productivity across various industrial applications.
Precision Cleaning
The advanced laser technology targets only contaminants, preserving the integrity and surface quality of the underlying material without causing damage.
Environmentally Friendly
Eliminate oil and grease without harsh chemicals or abrasive materials, reducing environmental impact and minimizing hazardous waste.
Enhanced Safety
With minimal dust and debris, our laser cleaning process improves workplace safety and simplifies cleanup, creating a cleaner and safer work environment.
Cost-Effective
The efficiency and automation of laser cleaning reduce labor costs and maintenance needs, offering a cost-effective solution for ongoing industrial cleaning tasks.
Versatile Application
Suitable for a range of surfaces and materials, laser cleaning adapts to different cleaning needs, making it ideal for automotive, manufacturing, and equipment maintenance.
Factors to Consider Before Buying Laser Oil and Grease Cleaning Machines
Laser Power
Choose a machine with adequate laser power to effectively remove oil and grease. Higher power ensures better performance but may increase energy consumption.
Beam Quality
Ensure the laser system offers high beam quality for precise and consistent cleaning, which is crucial for achieving optimal results on various surfaces.
Surface Compatibility
Verify that the machine is suitable for the types of surfaces you need to clean. Compatibility with different materials ensures versatile and effective cleaning.
Size and Portability
Consider the machine's size and portability to ensure it fits your workspace and meets your needs for maneuverability and ease of use in different settings.
Operating Costs
Evaluate the long-term operating costs, including energy use and maintenance, to ensure the machine is a cost-effective choice for your cleaning needs.
Safety Features
Look for comprehensive safety features, such as protective enclosures and emergency shutoff systems, to protect operators and comply with safety regulations.
Automation Capabilities
Assess the automation features of the machine, such as programmable settings and controls, which can enhance efficiency and reduce manual intervention.
Support and Warranty
Check for reliable customer support and a solid warranty to address any potential issues and ensure the machine’s longevity and reliability.
Comparison with Other Oil and Grease Cleaning Methods
Feature/Method | Laser Cleaning | Sandblasting | Chemical Paint Removal | Mechanical Grinding | Electrolytic Paint Removal | Ultrasonic Rust Removal |
Precision | High, targets only contaminants | Moderate, abrasive effects | Variable, can affect base material | Moderate, abrasive and rough | High, precise on specific contaminants | High, but limited to small parts |
Environmental Impact | Low, no harsh chemicals or abrasives | High, generates dust and waste | High, involves hazardous chemicals | Moderate, creates dust and debris | Low, primarily uses water and electricity | Low, non-toxic cleaning solution |
Safety | High, minimal dust and no chemicals | Moderate, requires protective gear | Low, involves toxic chemicals | Moderate, dust and noise issues | High, generally safe with proper setup | High, safe with non-toxic solutions |
Efficiency | High, fast and effective | Moderate, can be time-consuming | Variable, depends on chemical used | Moderate, can be time-consuming | High, effective for specific cases | Moderate, slower than other methods |
Surface Compatibility | Broad, works on various materials | Limited, may damage some surfaces | Limited, may react with materials | Limited, can damage delicate surfaces | Limited, effective on conductive surfaces | Broad, effective on various surfaces |
Cost of Operation | Moderate, energy-efficient | Low, but requires abrasive materials | Variable, cost of chemicals | Moderate, wear on grinding tools | High, specialized equipment needed | Moderate, requires ultrasonic equipment |
Maintenance | Low, minimal wear and tear | High, frequent maintenance needed | Moderate, cleanup and handling required | Moderate, wear on equipment | High, requires maintenance and setup | Moderate, periodic equipment care needed |
Versatility | High, adaptable to various needs | Moderate, specific to certain tasks | Low, specialized for paint removal | Moderate, specific to rough surfaces | Low, limited to conductive surfaces | Moderate, limited to small parts |
Application of Laser Rust Cleaning
- Automotive Maintenance: Laser cleaning efficiently removes oil and grease from automotive parts, including engines and chassis, ensuring components are clean for inspection, repair, and maintenance.
- Industrial Equipment: Ideal for cleaning heavy machinery and equipment, our laser technology removes stubborn oil and grease, enhancing performance and reducing downtime in industrial settings.
- Manufacturing Processes: In manufacturing, laser cleaning helps prepare surfaces by removing oil and grease, improving the adhesion and quality of coatings and welds on various parts.
- Aerospace Components: Laser cleaning effectively handles oil and grease on delicate aerospace components, ensuring optimal performance and safety by preparing surfaces for inspections and repairs.
- Marine Industry: In the marine sector, laser cleaning tackles oil and grease on ship parts and marine equipment, preventing corrosion and ensuring reliable operation in harsh environments.
- Metal Fabrication: For metal fabrication, our laser cleaning technology removes contaminants from metal surfaces, improving the quality of finished products and extending equipment life.
- Electronics Manufacturing: Laser cleaning is used to remove oil and grease from electronic components, ensuring the cleanliness and reliability of sensitive parts before assembly and testing.
- Equipment Upkeep: Regular cleaning of industrial equipment with lasers helps maintain performance, prevent buildup, and extend the lifespan of machinery and tools by effectively removing residues.
- Restoration Projects: In restoration work, laser cleaning removes oil and grease from historical artifacts and machinery, preserving the integrity of valuable items while ensuring thorough cleaning.
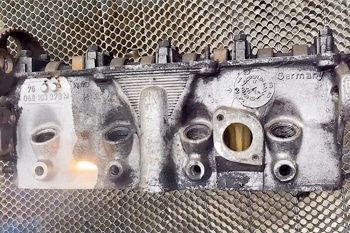
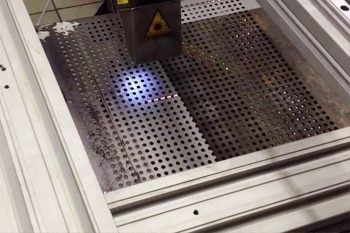
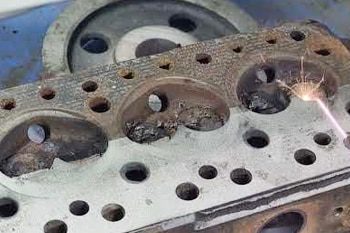
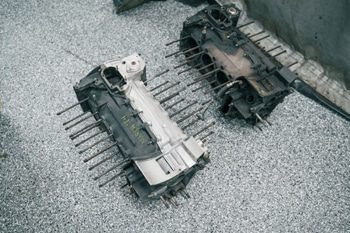
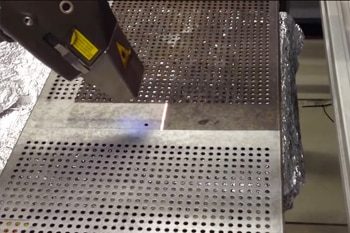
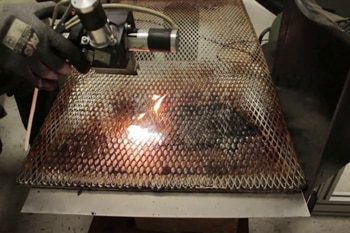
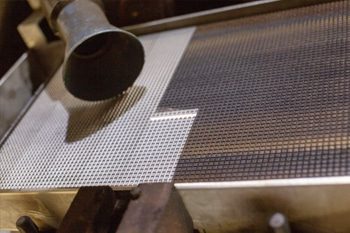
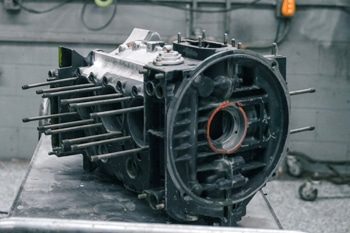