Product Introduction
Types of Pulsed Laser Cleaning Machines
-
Standard Pulse Laser Cleaning Machine
Rated 5.00 out of 5$6,000.00 – $65,400.00 This product has multiple variants. The options may be chosen on the product page -
Luggage Pulse Laser Cleaning Machine
Rated 5.00 out of 5$6,600.00 – $16,900.00 This product has multiple variants. The options may be chosen on the product page -
Backpack Pulse Laser Cleaning Machine
Rated 5.00 out of 5$6,900.00 – $9,200.00 This product has multiple variants. The options may be chosen on the product page
Application of Pulsed Laser Cleaning Machines
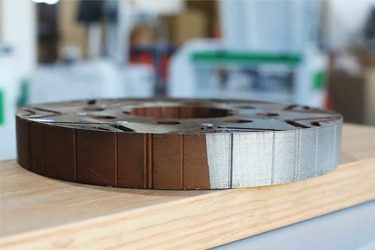

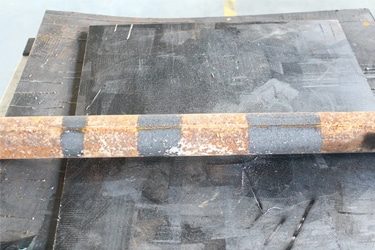

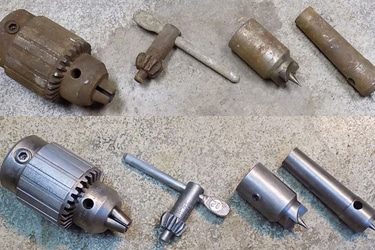
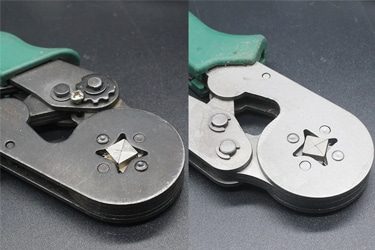
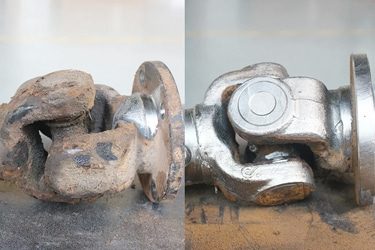
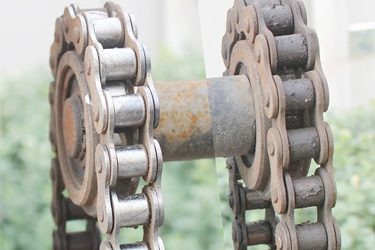
Customer Testimonials
Pulsed Laser Cleaning Machine VS Other Cleaning Machines
Comparison Item | Pulsed Laser Cleaning Machine | Sandblasting Machine | Ultrasonic Cleaning Machine | High-Pressure Cleaning Machine | Dry Ice Blasting Machine |
---|---|---|---|---|---|
Cleaning Method | Short laser pulses | Abrasive media blasting | Ultrasonic waves in liquid | High-pressure water stream | Dry ice particle impact |
Surface Damage Risk | Extremely low | High | Low | Medium to high | Low |
Thermal Impact | Minimal | None | Low | Medium | Low |
Material Compatibility | Delicate and heat-sensitive surfaces | Mostly durable materials | Small, sensitive parts | Hard surfaces only | Industrial surfaces |
Precision Level | Very high | Low | Medium | Low | Medium |
Cleaning Speed | Moderate to high | Medium | Low to medium | Medium | Medium |
Use of Chemicals | No | No | Yes (cleaning solutions) | Sometimes | No |
Waste Generation | None | High (abrasive waste) | Wastewater and chemical residue | Water runoff | CO₂ gas |
Environmental Impact | Eco-friendly | Generates dust and debris | Requires chemical disposal | High water use | Requires dry ice logistics |
Operating Cost | Low (after setup) | Medium to high | High (chemicals, maintenance) | Medium | High |
Maintenance Requirements | Low | High (abrasive part wear) | Medium (tank and fluid upkeep) | Medium | High (nozzle and system wear) |
Automation Capability | High | Difficult | Possible | Limited | Possible |
Portability | Compact, handheld options available | Generally bulky | Stationary | Portable but heavy | Medium portability |
Noise Level | Low | High | Low | High | High |
Ideal Use Cases | Fine detail, sensitive surfaces | Large metal structures | Electronics, small parts | Outdoor or large-surface cleaning | Industrial maintenance |
Why Choose Us
Efficient Cleaning
Our machines offer fast, precise cleaning without chemicals or abrasion, making them ideal for delicate surfaces and complex materials across various industries.
Safe & Eco-Friendly
Laser cleaning eliminates the need for harsh chemicals and generates no secondary pollution, creating a safer and more environmentally friendly workspace.
Stable Performance
Built with high-quality components and advanced control systems, our machines ensure consistent cleaning results with minimal maintenance and long service life.
Custom Solutions
We provide flexible configurations and tailored options to match different cleaning requirements, helping customers achieve optimal performance for their specific applications.
Related Resources
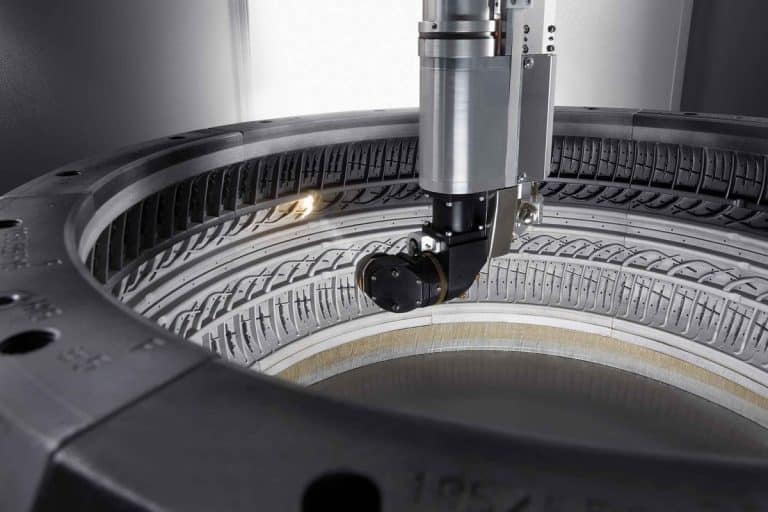
What Is Laser Cleaning?
Discover the power of laser cleaning, an advanced, eco-friendly technology for removing rust, paint, and contaminants with precision. Learn how it works, its benefits, and key applications.
Frequently Asked Questions
What Is Pulsed Laser Cleaning?
How Much Do Pulsed Laser Cleaning Machines Cost?
What Are the Main Factors Affecting the Price of Pulsed Laser Cleaning Machines?
- Laser Power Output: Higher power (e.g., 1000W or 2000W) allows faster, deeper cleaning and comes with a higher price tag. Lower power (100W–300W) is cheaper but suited for lighter tasks.
- Pulsed Type and Frequency: Machines with advanced pulsed control (like high repetition rates or ultrashort pulses) offer more precision and surface protection but are more expensive.
- Cooling System: Air-cooled systems are generally more affordable. Water-cooled systems support higher power levels and longer operating times but add to the cost.
- Machine Configuration: Portable, handheld units are often more affordable. Larger, automated, or integrated systems for production lines cost more.
- Optical and Control Components: Higher-end scanning heads, lenses, and control software contribute to precision and reliability, and raise the price.
- Brand and Country of Origin: Machines from well-known manufacturers or countries with stricter quality standards (e.g., Germany, Japan, USA) tend to cost more than those from lower-cost regions.
- Safety Features: Built-in shielding, sensors, interlocks, and certifications add to cost but are essential for compliance and operator safety.
What Contaminants Can Be Removed by Pulsed Lasers?
- Rust and Oxidation: From steel, aluminum, and other metals
- Paint and Coatings: Including old paint layers, powder coating, or surface treatments
- Oil, Grease, and Lubricants: From machinery parts, molds, and tools
- Adhesive Residues: Left from tapes, glues, or labels
- Carbon Deposits: On engine parts, turbines, or injection molds
- Oxide Layers: After welding or heat treatment
- Dirt and Dust: Including fine surface contamination or embedded particles
- Corrosion Products: On industrial equipment, pipes, or structures
- Biological Residue: In applications like cultural heritage restoration or medical tool cleaning
How Does the Pulsed Duration Affect the Cleaning Results?
- Shorter pulsed durations (e.g., picoseconds or femtoseconds)
- Deliver energy extremely fast, causing ablation with minimal heat transfer.
- Ideal for sensitive or high-precision applications like electronics, semiconductors, or heritage conservation.
- Minimize the risk of thermal damage or material deformation.
- Produce cleaner edges and more precise removal.
- Longer pulsed durations (e.g., nanoseconds)
- Generate more heat during cleaning.
- Better suited for heavier-duty jobs like removing thick rust, paint, or industrial coatings.
- May cause slight surface heating or discoloration if not properly controlled.
What Are the Hazards of Pulsed Laser Cleaning?
- Eye Injuries: Pulsed lasers emit high-energy light that can permanently damage the retina, even from reflected beams. Laser safety glasses are essential.
- Skin Burns: Direct or reflected exposure to the laser can cause serious burns. High-energy pulses, even for short durations, carry enough power to harm unprotected skin.
- Toxic Fumes and Particles: The laser vaporizes contaminants, which can release harmful fumes, gases, and fine particles, especially when removing paint, rust, or coatings. Without proper fume extraction, these pose respiratory risks.
- Fire Risk: Pulsed lasers can ignite flammable materials or dust nearby. Work areas should be free of combustible items, and fire safety measures should be in place.
- Noise: Some high-power pulsedsystems generate sharp, loud bursts of sound that may require hearing protection in enclosed or prolonged use scenarios.
- Equipment Damage: Incorrect settings or improper use can damage sensitive surfaces, optics, or the machine itself, especially in high-precision work.
- Electrical Hazards: Like all industrial equipment, pulsedlaser systems operate on high-voltage circuits and cooling systems, posing shock or short-circuit risks if not maintained properly.
What Are the Disadvantages of Pulsed Laser Cleaning Machines?
- Higher Cost for Precision Models: Machines with ultra-short pulsed durations (like picosecond or femtosecond lasers) are more expensive due to advanced technology and tighter tolerances.
- Slower Cleaning Speed: Compared to continuous lasers, pulsed systems generally clean slower, especially when dealing with thick rust, heavy coatings, or large surfaces.
- Limited Power for Heavy-Duty Tasks: Lower-power pulsed lasers may struggle with deeply embedded contaminants or thick industrial coatings, making them less suitable for heavy-duty applications.
- Requires Technical Knowledge: Proper setup, parameter tuning, and surface matching require skilled operators to get optimal results and avoid surface damage.
- Maintenance of Precision Optics: Pulsedlaser systems often use high-end optical components that must be kept clean and aligned. This adds to upkeep and potential downtime.
- Not Ideal for Large-Area Cleaning: Cleaning large surfaces with a pulsedlaser can be time-consuming and less cost-effective compared to other methods like continuous lasers or abrasive blasting.
What Is the Service Life of Pulsed Laser Cleaning Machines?
- Laser Source Quality: High-end fiber lasers (like IPG, JPT) tend to last longer and perform more consistently over time.
- Usage Conditions: Frequent high-power use, poor ventilation, or harsh environments can shorten lifespan.
- Maintenance: Regular cleaning of optics, cooling systems, and filters helps extend the machine’s life.
- Component Quality: The durability of parts like scanners, lenses, and power supplies also impacts longevity.