Product Introduction
Types of Sheet Laser Cutting Machines
-
AKJ-F1 Laser Cutting Machine
Rated 4.75 out of 5$12,200.00 – $58,600.00 This product has multiple variants. The options may be chosen on the product page -
AKJ-F2 Laser Cutting Machine
Rated 5.00 out of 5$17,700.00 – $73,500.00 This product has multiple variants. The options may be chosen on the product page -
AKJ-F3 Laser Cutting Machine
Rated 5.00 out of 5$19,000.00 – $166,000.00 This product has multiple variants. The options may be chosen on the product page -
AKJ-FB Laser Cutting Machine
Rated 4.50 out of 5$15,200.00 – $175,500.00 This product has multiple variants. The options may be chosen on the product page -
AKJ-FC Laser Cutting Machine
Rated 4.75 out of 5$23,500.00 – $175,000.00 This product has multiple variants. The options may be chosen on the product page -
AKJ-FBC Laser Cutting Machine
Rated 4.50 out of 5$28,000.00 – $185,000.00 This product has multiple variants. The options may be chosen on the product page
Application of Sheet Laser Cutting Machines
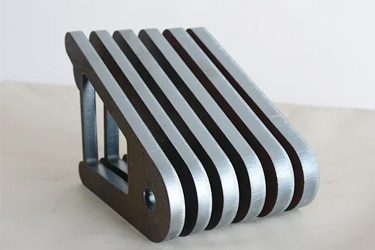
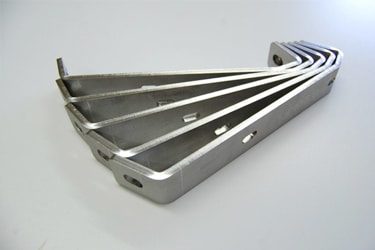
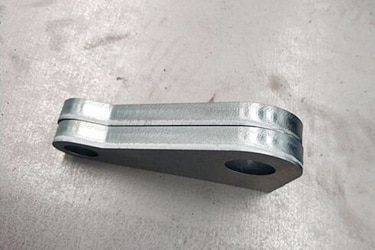

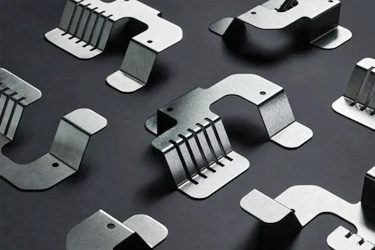
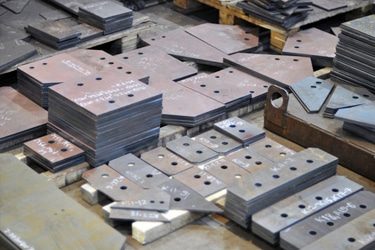
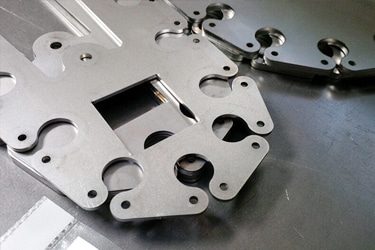
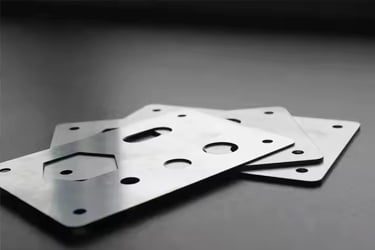
Customer Testimonials
Sheet Laser Cutting Machine VS Other Cutting Machines
Comparison Item | Sheet Laser Cutting Machine | Plasma Cutting Machine | Waterjet Cutting Machine | Mechanical Cutting Machine |
Cutting Method | Laser beam (thermal) | Plasma arc (thermal) | High-pressure water + abrasive | Blades, punches, or saws |
Cutting Precision | Very high | Moderate | High | Low to moderate |
Edge Quality | Clean, smooth edges | Rougher edges | Smooth edges | May require finishing |
Cutting Speed | Fast | Very fast | Slow to moderate | Moderate |
Material Thickness Range | Thin to medium sheets | Medium to thick sheets | Thin to thick | Limited by tool size |
Material Compatibility | Metals (SS, CS, aluminum, etc.) | Conductive metals only | Almost all materials | Limited to softer or specific materials |
Heat-Affected Zone | Minimal | Large | None | None |
Cutting Accuracy | ±0.1 mm or better | ±1 mm | ±0.2 mm | ±0.5 mm or more |
Setup Time | Short | Short | Long | Moderate |
Waste and Kerf | Minimal | Medium | High | Medium |
Operating Cost | Low to moderate | Low | High (abrasives, water, energy) | Low |
Maintenance Requirements | Low | Medium | High | High |
Automation Capability | High (CNC and smart systems) | Moderate | Moderate | Low to moderate |
Environmental Impact | Clean, no consumables | Fumes and dross | Water and abrasive disposal | Noise, debris, and tool wear |
Ideal Use Cases | Precision parts, complex designs | Heavy-duty metal cutting | Non-metal + metal cutting | Basic shapes, high-volume cuts |
Why Choose Us
Advanced Technology
Our laser cutting machines feature high-speed, precision cutting with the latest laser technology, ensuring smooth edges, minimal waste, and superior efficiency across various materials and thicknesses.
Reliable Quality
Each machine undergoes rigorous quality control and durability testing to ensure long-term stability, low maintenance, and consistent high performance, even under demanding industrial conditions.
Comprehensive Support
We provide full technical support, including installation guidance, operator training, and after-sales service, ensuring smooth machine operation and minimal downtime for your business.
Cost-Effective Solutions
Our machines offer high performance at competitive prices, with customizable options to fit different production needs, helping businesses maximize their investment without compromising on quality.
Related Resources
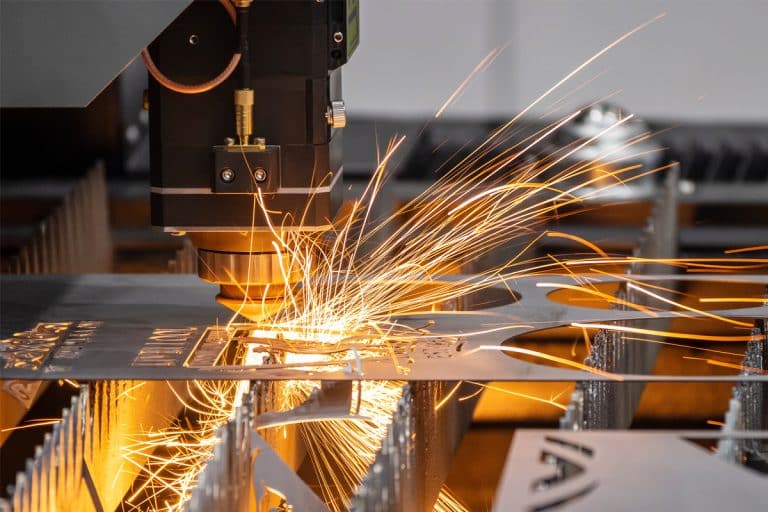
What Is Laser Cutting?
Discover the fundamentals of laser cutting, its process, types, applications, and benefits. Learn how this advanced technology is transforming modern manufacturing.
Frequently Asked Questions
What Is Sheet Laser Cutting?
- Process: A focused laser beam is directed at the sheet, which heats and cuts through it. A computer numerical control (CNC) system guides the laser based on a digital design.
- Precision: Because the laser beam is extremely narrow, it allows for tight tolerances, intricate shapes, and minimal waste.
- Speed & Efficiency: Laser cutting is fast and repeatable, making it ideal for both prototypes and large-scale production.
What Is The Main Disadvantage of Sheet Laser Cutting?
- Equipment Cost: Laser cutting machines are expensive to buy and maintain. Fiber and CO2 lasers require a significant investment, making them less accessible for small shops or low-budget operations.
- Operating Cost: While efficient, they consume a lot of power and may require assist gases like nitrogen or oxygen, adding to the cost.
- Material Limitations: Very thick materials can be hard to cut cleanly. Reflective metals (like copper or brass) can also pose challenges without the right equipment.
- Safety Concerns: High-powered lasers can be dangerous if not handled properly, requiring strict safety protocols.
What Is The Cost of Sheet Laser Cutting Machines?
- Entry-Level Machines ($12,500–$30,000)
- Lower wattage (around 1kW–3kW)
- Suitable for light-duty metal cutting, small workshops, or hobby use
- Limited cutting thickness and slower speeds
- Mid-Range Machines ($30,000–$70,000)
- Medium wattage (4kW–6kW)
- Better cutting quality, speed, and thickness range
- Good for small to mid-size manufacturers
- Industrial Machines ($80,000–$190,000+)
- High power (12kW and above)
- Built for 24/7 production and heavy-duty cutting
- Includes automation, cooling systems, and advanced software
What Thickness Ranges Can Sheet Laser Cutting Machines Effectively Handle?
- Carbon Steel
- 1KW-2KW: 6-10 mm
- 3KW–6KW: 12-20 mm
- 12KW+: up to 30 mm
- Stainless Steel
- 1KW–2KW: 4–6 mm
- 3KW–6KW: 10–20 mm
- 12KW+: up to 30 mm
- Aluminum
- 1KW–2KW: 3–6 mm
- 3KW–6KW: 10–16 mm
- 12KW+: up to 20 mm
- Copper & Brass
- 1KW–2KW: 2–4 mm
- 3KW–6KW: 6–10 mm
- 12KW+: up to 12 mm
How To Choose The Correct Sheet Laser Cutting Machine Bed Size?
- Material Size Compatibility: Pick a bed size that fits your most commonly used sheet sizes (e.g., 4′ x 8′ or 5′ x 10′). Avoid having to cut down materials before use—it wastes time and adds inconsistency.
- Part Size and Nesting: Smaller parts benefit from larger beds due to better nesting and material use. If cutting large parts, make sure the bed fits the biggest piece in one go to avoid misalignment.
- Production Volume: Low-volume jobs can work with smaller beds. High-volume or industrial production needs larger beds for better efficiency, fewer material changes, and support for automation.
- Workshop Space: Bigger machines need more floor space. Ensure your shop can accommodate the machine, plus room for loading, maintenance, and ventilation.
- Cost vs. Long-Term Value: Smaller machines cost less upfront, but larger beds may save more over time through higher output and reduced waste. If you’re planning to grow, consider sizing up now.
What Is The Service Life of Sheet Laser Cutting Machines?
- Typical Service Life: Most well-maintained fiber laser cutting machines last 8 to 10 years or more. If the machine is not properly maintained, its lifespan may be shortened.
- Usage Intensity: Machines running multiple shifts daily will wear faster than those used occasionally. High-volume industrial use might reduce effective service life to around 6–8 years without proper care.
- Maintenance Practices: Regular maintenance is critical. Replacing worn parts, keeping optics clean, and ensuring proper cooling and alignment can extend lifespan significantly.
- Laser Source Lifespan: Fiber lasers typically last 100,000+ hours of operation. However, parts like lenses, nozzles, and motion systems will need periodic replacement regardless of the laser source’s lifespan.
- Build Quality and Brand: Machines from reputable manufacturers with solid construction and components tend to last longer and hold up better under stress.
What Are The Main Dangers of Sheet Laser Cutting Machines?
- Laser Radiation: The laser beam can cause serious eye and skin injuries. Fiber lasers operate at high power, and direct or reflected exposure can be harmful. Always use proper safety enclosures and wear eye protection rated for the laser wavelength.
- Fire Hazard: Laser cutting generates intense heat, which can ignite flammable materials, dust, or nearby debris. Poor ventilation, improper materials, or leaving the machine unattended increases the risk of fire.
- Fumes and Gases: Cutting certain materials—especially plastics or coated metals—releases toxic fumes. Without proper fume extraction or filtration systems, these can pose respiratory hazards and contaminate the workspace.
- Mechanical Injuries: Moving parts like the gantry, cutting head, or sheet loader can crush or trap fingers and hands if safety protocols aren’t followed. Auto-loading systems require extra caution.
- Electrical Hazards: Laser cutting machines run on high-voltage systems. Faulty wiring, poor grounding, or unauthorized repairs can lead to electric shock or equipment failure.
- Noise Exposure: Some machines, especially high-power models or those used in industrial settings, can generate excessive noise, which may require hearing protection in continuous-use environments.
How To Maintain Sheet Laser Cutting Machines?
- Daily Cleaning and Inspection: Clean the machine bed, lenses, and nozzles at the start or end of each shift. Remove metal dust, slag, and debris. Inspect the optical path (if applicable) and check for any loose bolts or abnormal noises.
- Lens and Nozzle Maintenance: Dirty or damaged lenses and nozzles reduce cutting quality. Clean them regularly with appropriate solvents and replace them when worn. A clogged nozzle can cause inconsistent cuts or material damage.
- Lubrication and Moving Parts: Lubricate guide rails, gears, and bearings according to the manufacturer’s schedule. Keeping the motion system smooth reduces wear and keeps precision high.
- Cooling System Care: For machines with water-cooled lasers, monitor coolant levels and clean filters. Replace water or coolant periodically to avoid overheating or scale buildup in the laser source.
- Check Alignment and Focus: Verify beam alignment and focus regularly. Misalignment can cause poor cutting results and unnecessary wear on components.
- Software and Firmware Updates: Keep the machine’s software and firmware up to date. Manufacturers often release updates that improve performance, fix bugs, or enhance safety features.
- Scheduled Maintenance: Follow the manufacturer’s recommended service intervals. This includes checking belts, air filters, vacuum systems, and electrical connections. Keeping a maintenance log helps track issues and stay on schedule.