Product Introduction
Types of Continuous Laser Cleaning Machines
-
Standard Continuous Laser Cleaning Machine
Rated 5.00 out of 5$3,800.00 – $15,500.00 This product has multiple variants. The options may be chosen on the product page -
Portable Continuous Laser Cleaning Machine
Rated 4.50 out of 5$3,700.00 – $15,500.00 This product has multiple variants. The options may be chosen on the product page -
Double Wobble Continuous Laser Cleaning Machine
Rated 4.75 out of 5$4,300.00 – $16,000.00 This product has multiple variants. The options may be chosen on the product page
Application of Continuous Laser Cleaning Machines
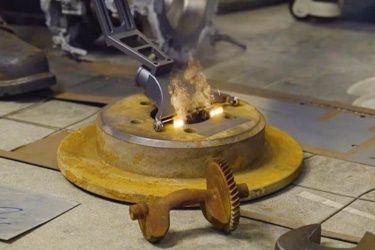
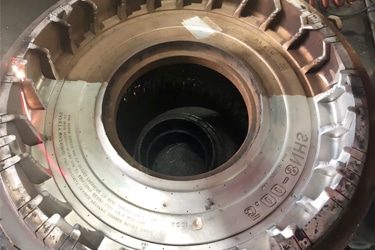

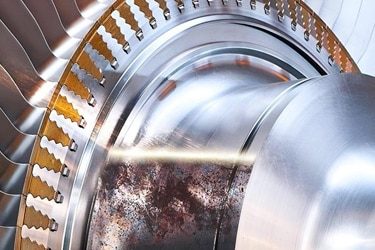
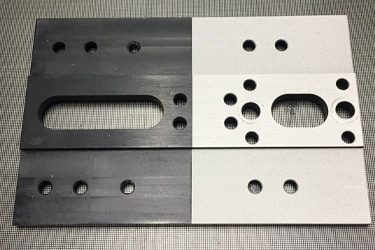
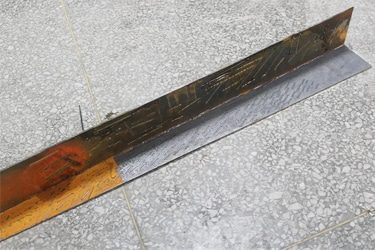
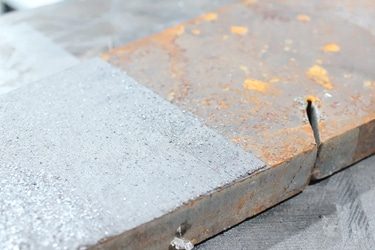
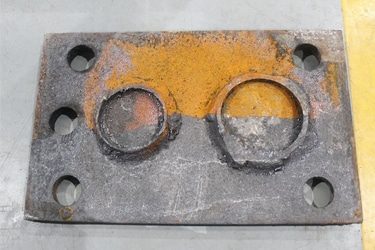
Customer Testimonials
Continuous Laser Cleaning Machine VS Other Cleaning Machines
Comparison Item | Continuous Laser Cleaning Machine | Sandblasting Machine | Ultrasonic Cleaning Machine | High-Pressure Cleaning Machine | Dry Ice Blasting Machine |
Cleaning Method | Continuous wave laser beam | Abrasive blasting | Ultrasonic vibration in liquid | High-pressure water jet | CO₂ ice particles |
Cleaning Speed | Very high, continuous operation | Medium | Low to medium | Medium | Medium |
Surface Contact | Non-contact | Contact-based | Full immersion | Direct contact | Impact-based |
Material Damage Risk | Very low | High | Low | Medium | Low |
Use of Chemicals | None | None | Yes | Sometimes | None |
Waste Production | Minimal (no secondary waste) | High (abrasive residue) | Wastewater and chemical waste | Water runoff | CO₂ gas |
Environmental Impact | Eco-friendly | Dust and debris generation | Waste management required | High water use | Requires CO₂ supply |
Automation Compatibility | Easy to integrate into production | Limited | Moderate | Difficult | Moderate |
Operating Cost | Low after setup | Medium to high | High (chemicals, energy) | Medium | High |
Maintenance Requirements | Low | Frequent abrasive replacement | Regular tank and transducer upkeep | High (pump, nozzle wear) | Frequent maintenance |
Precision Cleaning | High precision | Low precision | Medium precision | Low precision | Medium precision |
Noise Level | Low | High | Low | High | High |
Material Compatibility | Broad (metal, stone, composites) | Mostly metals | Delicate and electronic parts | Hard, durable surfaces | Mostly industrial metals |
Portability | Available in portable & fixed models | Generally bulky | Stationary | Portable, but heavy | Medium portability |
Ideal Use Case | Continuous industrial production | Surface roughening, rust removal | Delicate parts, small items | Heavy-duty surface washing | Medium-duty industrial cleaning |
Why Choose Us
Efficient Cleaning
Our machines offer fast, precise cleaning without chemicals or abrasion, making them ideal for delicate surfaces and complex materials across various industries.
Safe & Eco-Friendly
Laser cleaning eliminates the need for harsh chemicals and generates no secondary pollution, creating a safer and more environmentally friendly workspace.
Stable Performance
Built with high-quality components and advanced control systems, our machines ensure consistent cleaning results with minimal maintenance and long service life.
Custom Solutions
We provide flexible configurations and tailored options to match different cleaning requirements, helping customers achieve optimal performance for their specific applications.
Related Resources
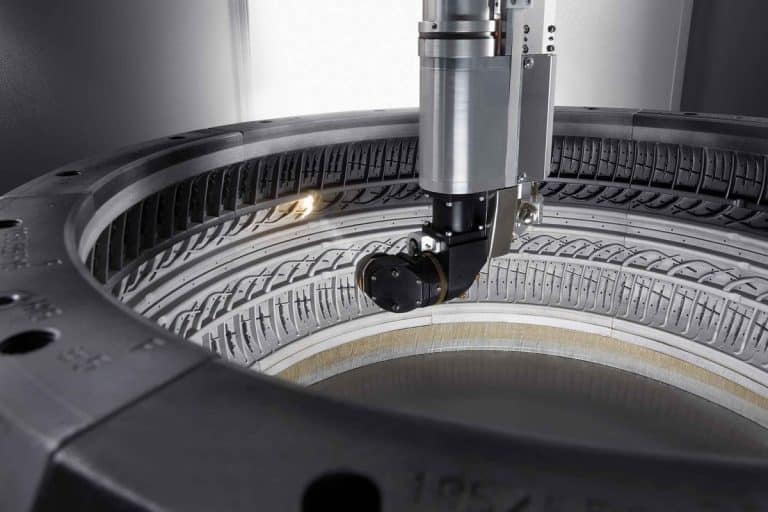
What Is Laser Cleaning?
Discover the power of laser cleaning, an advanced, eco-friendly technology for removing rust, paint, and contaminants with precision. Learn how it works, its benefits, and key applications.
Frequently Asked Questions
What Is Continuous Laser Cleaning?
What Laser Powers Can Be Selected for Continuous Laser Cleaning Machines?
How Do I Determine Which Power Level Will Meet My Cleaning Application?
- Type and Thickness of Contamination
- Light rust, thin paint, or surface dust: Lower power levels (100W-500W, pulse) are usually enough.
- Medium coatings, moderate rust, adhesives: Mid-range power (1000W-2000W) provides a balance of speed and control.
- Heavy rust, thick paint, industrial buildup: High power (3000W-6000W, continuous) is best for fast, deep cleaning.
- Material Sensitivity
- For delicate surfaces (e.g., thin metals, electronic parts), lower-power pulsed lasers are safer.
- For durable surfaces (e.g. steel, iron, tooling), high-power continuous lasers can be used without damage.
- Cleaning Speed Requirements
- High-volume or time-sensitive jobs (factories, production lines) benefit from higher power.
- Precision tasks or occasional use can be done with lower power machines.
- Surface Area
- Large surfaces need higher power to maintain speed and efficiency.
- Small or detailed areas are better handled with lower power and finer control.
How Does Continuous Laser Cleaning Remove Surface Contaminants?
- The laser beam hits the contaminated surface with continuous energy.
- The contaminants absorb the laser energy, while the base material reflects most of it (especially if it’s metal).
- This intense, focused heat causes the contaminants to rapidly vaporize, melt, or break apart.
- The result is a clean, bare surface, without the need for chemicals, abrasives, or physical contact.
What Materials Can Be Cleaned With Continuous Laser Cleaning Machines?
- Carbon steel: Removes rust, paint, and scale quickly.
- Stainless steel: Cleans welds, oxidation, and coatings without damage.
- Aluminum: Strips paint, oxides, and residue, though care is needed due to heat sensitivity.
- Iron: Effective for rust and corrosion removal.
- Titanium: Used in aerospace or medical industries for precision cleaning.
- Copper and brass: Removes surface oxides and residues, often in electronics or tooling.
Does Continuous Laser Cleaning Require The Use Of Auxiliary Gas?
- Improved cleaning efficiency: The gas helps blow away debris and vaporized material from the surface, keeping the laser path clear.
- Better surface protection: Inert gases like nitrogen or argon prevent oxidation, especially when cleaning reactive metals like aluminum or titanium.
- Cooler processing: Gas flow can reduce surface heat and minimize thermal damage.
- Cleaner results: Gas reduces residue buildup and leaves a more polished surface.
What Are the Safety Measures for Operating Continuous Laser Cleaning Machines?
- Wear Laser Safety Glasses: Always use laser-specific safety glasses that match the machine’s wavelength and power. This protects your eyes from direct or reflected beams.
- Use Protective Clothing: Wear flame-resistant, non-reflective clothing, gloves, and closed-toe shoes to shield against laser exposure, sparks, and debris.
- Restrict Access to the Work Area: Operate the machine in a designated, enclosed area with clear warning signs. Limit access to trained personnel only.
- Use a Laser Safety Enclosure or Shielding: Use barriers or enclosures to contain the laser beam and prevent accidental exposure.
- Enable Fume Extraction: Install proper ventilation or fume extraction systems to remove harmful smoke, dust, and particles generated during cleaning.
- Train Operators Properly: Ensure all operators are trained in laser safety, machine operation, and emergency procedures.
- Emergency Stop and Interlock Systems: Machines should be equipped with emergency stop buttons and interlocks to shut off the laser immediately if a safety breach occurs.
- Regular Maintenance and Inspection: Check optical components, shielding, and safety systems regularly to ensure proper function and avoid accidental hazards.
How Do I Maintain Continuous Laser Cleaning Machines?
- Clean Optical Components Regularly: Inspect and clean the laser lens, protective window, and scanning head to prevent buildup of dust, debris, or burned-on residue. Dirty optics reduce cleaning power and can overheat.
- Check and Replace Filters: If your system uses a fume extractor or cooling unit, regularly check and replace air and fluid filters to keep airflow and temperature regulation effective.
- Inspect Cables and Connectors: Look for wear, loose connections, or cable damage. Faulty connections can affect performance or cause shutdowns.
- Monitor Cooling Systems: Continuous lasers generate significant heat. Check coolant levels, hose integrity, and radiator cleanliness. If using air cooling, ensure ventilation fans and grills are free of blockages.
- Update Software and Firmware: Keep control software and firmware up to date to benefit from bug fixes, safety patches, and performance improvements.
- Perform System Diagnostics: Run built-in diagnostics or monitoring tools to check laser output, power stability, and system errors. Address issues early before they lead to failure.
- Follow Manufacturer’s Schedule: Always follow the maintenance intervals and checklists provided by the machine manufacturer. Skipping scheduled service can void warranties and reduce reliability.