Laser Welding Titanium
Laser Titanium Welding Machine
-
Handheld Standard Laser Welding Machine
Rated 4.75 out of 5$3,300.00 – $7,000.00 This product has multiple variants. The options may be chosen on the product page -
Handheld Portable Laser Welding Machine
Rated 4.75 out of 5$3,200.00 – $6,900.00 This product has multiple variants. The options may be chosen on the product page -
Handheld 3 in 1 Laser Welding Cleaning Machine
Rated 5.00 out of 5$3,400.00 – $7,100.00 This product has multiple variants. The options may be chosen on the product page -
Handheld Air-Cooled Laser Welding Machine
Rated 4.75 out of 5$4,300.00 – $5,700.00 This product has multiple variants. The options may be chosen on the product page -
Handheld Double Wobble Laser Welding Machine
Rated 4.75 out of 5$3,800.00 – $7,500.00 This product has multiple variants. The options may be chosen on the product page -
Handheld Double Wire Feed Laser Welding Machine
Rated 4.75 out of 5$6,400.00 – $7,300.00 This product has multiple variants. The options may be chosen on the product page -
Portable Air-Cooled Laser Welding Machine
Rated 4.50 out of 5$3,400.00 – $5,300.00 This product has multiple variants. The options may be chosen on the product page -
Handheld Air-Cooled 3 in 1 Laser Welding Machine
Rated 5.00 out of 5$3,600.00 – $5,500.00 This product has multiple variants. The options may be chosen on the product page -
CNC Platform Automatic Fiber Laser Welding Machine
Rated 4.50 out of 5$8,500.00 – $12,200.00 This product has multiple variants. The options may be chosen on the product page -
6-Axis Robotic Automatic Laser Welding Machine
Rated 5.00 out of 5$12,300.00 – $16,000.00 This product has multiple variants. The options may be chosen on the product page
Benefits of Laser Welding Titanium
High Precision
Laser welding allows for exceptional control over the weld area, minimizing heat-affected zones and ensuring precise, clean welds on titanium components.
Reduced Material Distortion
The focused laser beam generates minimal heat, which reduces thermal distortion and ensures that the integrity of thin titanium materials is maintained.
Strong, Durable Welds
Laser welding creates high-quality, defect-free joints that maintain titanium's mechanical properties, resulting in durable welds suitable for demanding applications.
Efficient Welding Process
Laser welding is faster than traditional methods, improving productivity and enabling quick, efficient welding of titanium in both small and large-scale operations.
Minimal Post-Processing
Laser welding produces smooth, clean welds that require little to no post-processing, saving time and reducing costs associated with finishing work.
Oxidation Prevention
Using inert gas shielding with laser welding protects titanium from oxidation during the process, ensuring high weld integrity and avoiding contamination.
Factors to Consider Before Buying Laser Titanium Welding Machines
Cooling System
A reliable cooling system is essential for dissipating heat from the laser generator, ensuring stable performance, and extending the lifespan of the machine.
Laser Power
Select a machine with appropriate laser power to handle the thickness of titanium materials. Higher power increases welding speed but may require more cooling.
Weld Precision
Evaluate the machine's ability to deliver precise, clean welds, particularly on thin or intricate titanium components, to ensure optimal welding quality.
Shielding Gas Compatibility
Titanium welding requires shielding gas to prevent oxidation. Ensure the machine can integrate with an inert gas system to protect the weld zone.
Automation Features
Machines with advanced automation options, such as programmable settings and robotic integration, enhance efficiency, especially in high-volume titanium welding applications.
Material Compatibility
Consider whether the machine is designed specifically for titanium or if it can handle other metals, offering versatility for diverse welding needs.
Ease of Operation
User-friendly controls and intuitive interfaces simplify operation and reduce the learning curve, enabling faster setup and more efficient welding.
After-Sales Support
Look for manufacturers that offer comprehensive after-sales support, including maintenance, training, and troubleshooting, ensuring maximum uptime and productivity.
Comparison with Other Titanium Welding Methods
Feature | Laser Welding | TIG Welding | MIG Welding | Plasma Arc Welding |
Precision | High precision, minimal heat-affected zones | Moderate precision with potential for larger heat-affected areas | Moderate precision, larger heat-affected zone | High precision, similar to laser welding |
Welding Speed | Fast, especially for thin materials | Slower, requires more time for setup and operation | Moderate speed, faster than TIG but slower than laser | Fast, but can be slower than laser in certain applications |
Heat Input | Low, reducing thermal distortion | Higher heat input, greater risk of distortion | Moderate heat input, more than laser, less than TIG | Moderate heat input, greater than laser |
Post-Processing | Minimal to no post-processing required | Often requires additional post-processing to remove oxidation | Requires post-processing for a better finish | Minimal post-processing, similar to laser |
Suitability for Thin Titanium | Ideal for thin and delicate components | More challenging, higher risk of burn-through | Works well but requires careful heat management | Suitable for thin materials, but with a higher skill requirement |
Equipment Cost | Higher initial investment, lower operational costs | Lower cost of entry, higher operational costs | Moderate cost, but consumables can increase expenses | Higher cost, closer to laser welding |
Shielding Gas Requirements | Requires shielding gas to prevent oxidation | Requires continuous shielding gas flow | Requires shielding gas but uses more than laser | Requires inert gas, similar to TIG |
Application Versatility | Excellent for precision and high-tech industries | Suitable for a wide range of applications | Good for general welding applications | Primarily used in aerospace and precision industries |
Application of Laser Welding Titanium
- Aerospace Industry: Laser welding offers precise, strong joints that withstand extreme conditions, making it ideal for components like airframes, turbine blades, and engine parts.
- Medical Devices: In the medical field, titanium is favored for its biocompatibility, especially for implants and surgical instruments.
- Automotive Industry: Laser welding is essential for creating precise, durable joints in parts such as exhaust systems, engine components, and structural parts, improving overall vehicle performance and lifespan.
- Consumer Electronics: Laser welding allows for the precise assembly of small titanium components, such as in smartphones, laptops, and wearable devices, ensuring seamless design and durability in compact spaces.
- Marine Industry: Laser welding is used to create durable, watertight joints in components such as propeller shafts, hulls, and deep-sea exploration equipment.
- Energy Sector: Laser welding ensures the integrity of titanium joints in harsh environments, particularly in components exposed to corrosive substances or extreme pressures.
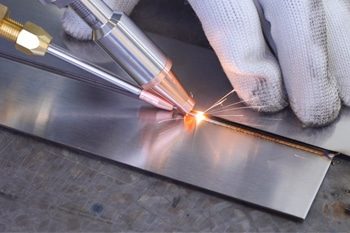
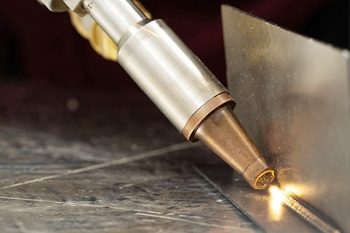
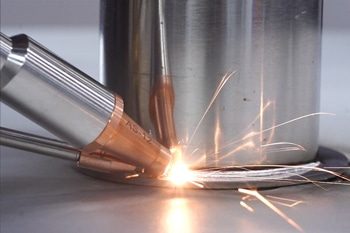
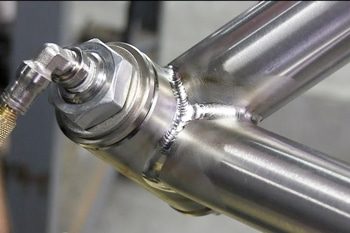
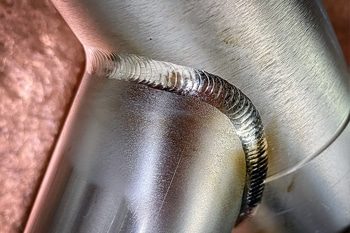
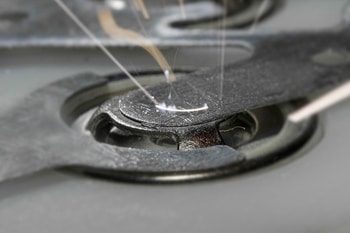
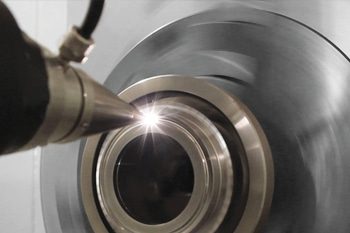
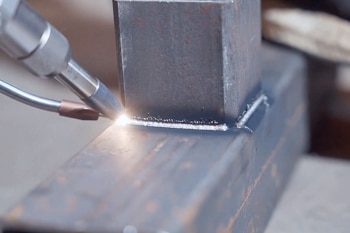