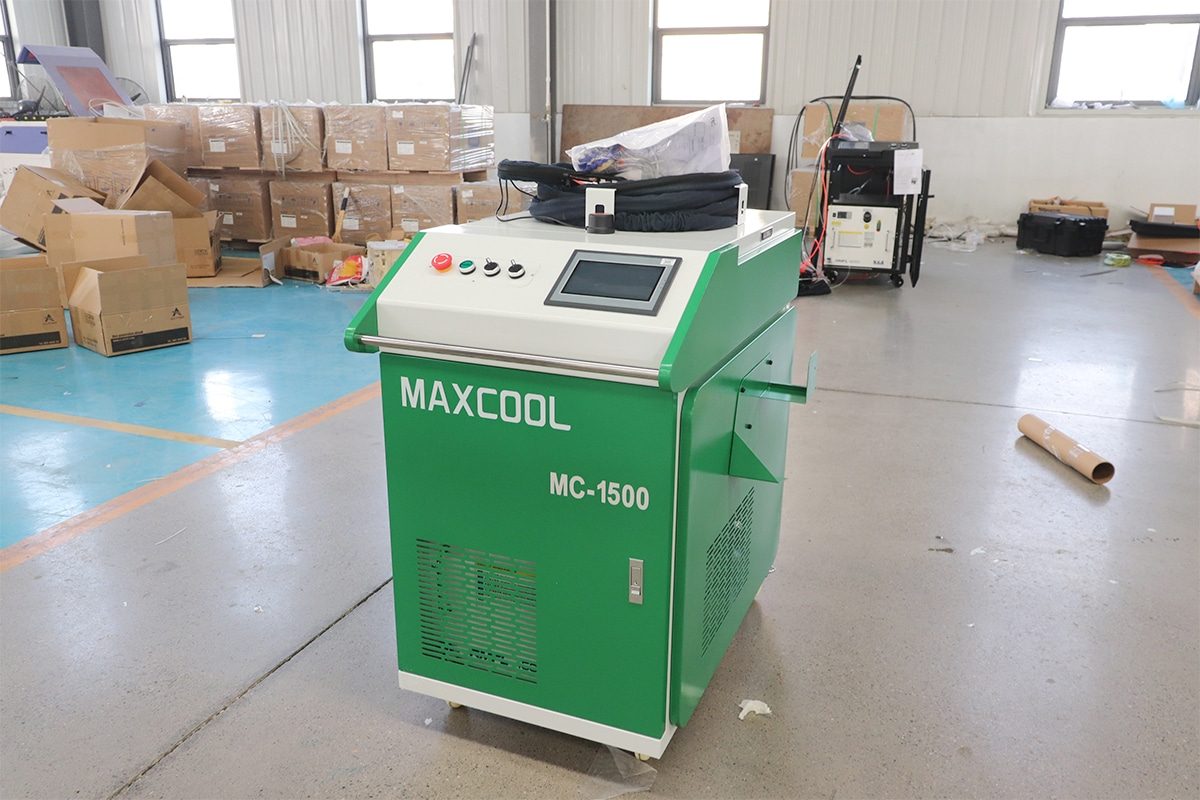
Laser Cleaning Machine Buying Guide
In the rapidly evolving industrial landscape, efficiency and precision are more critical than ever. Traditional cleaning methods like chemical treatments and abrasive blasting are becoming obsolete due to their environmental impact and inefficiency. Laser cleaning technology has emerged as a revolutionary solution, offering a non-contact, eco-friendly, and highly efficient method for surface preparation and contamination removal. Whether you’re in automotive, aerospace, manufacturing, or restoration, understanding the capabilities and benefits of laser cleaning is essential. This buying guide aims to provide comprehensive insights into laser cleaning machines, helping you make an informed decision for your business needs.
Table of Contents
Understanding Laser Cleaning Technology
What is Laser Cleaning?
Laser cleaning is an advanced, non-contact method of removing contaminants, coatings, impurities, or residues from the surface of materials using laser irradiation. This technology utilizes high-energy laser pulses to eliminate unwanted substances such as rust, paint, oxides, oils, and other contaminants without damaging the underlying substrate. Laser cleaning offers a precise and eco-friendly alternative, unlike traditional cleaning methods that rely on chemical solvents, abrasive materials, or mechanical scrubbing. It minimizes waste, reduces environmental impact, and enhances cleaning efficiency across various industrial applications.
How Does Laser Cleaning Work?
Laser cleaning operates on the principle of laser ablation, where focused laser energy interacts with the material’s surface to remove contaminants. Here’s a step-by-step explanation of how the process works:
- Laser Beam Generation: The laser cleaning machine generates a high-intensity laser beam using a laser source. The type of laser (continuous or pulsed) and its parameters (wavelength, pulse duration, energy density) are selected based on the specific cleaning requirements.
- Energy Absorption: When the laser beam is directed onto the contaminated surface, the contaminants absorb the laser energy more readily than the underlying material due to differences in their optical properties.
- Rapid Heating and Vaporization: The absorbed energy causes the contaminants to rapidly heat up, leading to vaporization, sublimation, or thermal expansion. This process effectively breaks the bond between the contaminants and the substrate.
- Micro Explosion Effect: In some cases, the rapid heating results in micro-plasma bursts and shockwaves that further dislodge the contaminants from the surface.
- Removal of Contaminants: The dislodged particles are then removed from the surface, often assisted by an integrated vacuum or ventilation system that captures and filters out the debris.
- Substrate Preservation: The laser parameters are precisely controlled to ensure that the substrate remains unaffected. The underlying material reflects the laser energy or dissipates it without undergoing any significant change.
By understanding how laser cleaning works, industries can leverage this technology to improve product quality, enhance surface preparation, and meet stringent environmental regulations.
Types of Laser Cleaning Machines
When choosing a laser cleaning machine, it’s essential to understand the different types available to select the one that best fits your specific needs. The two primary categories are Pulse Laser Cleaning Machines and Continuous Wave (CW) Laser Cleaning Machines. Each type has unique characteristics, advantages, and ideal applications.
Pulse Laser Cleaning Machines
Pulse Laser Cleaning Machines utilize short, high-energy laser pulses to remove contaminants from surfaces. The laser emits bursts of energy in nanoseconds to microseconds, allowing for precise control over the cleaning process. This pulsed approach minimizes heat input to the substrate, reducing the risk of thermal damage.
Key Features
- Precision Cleaning: Ideal for applications requiring meticulous removal of thin layers of contaminants without affecting the underlying material.
- Low Thermal Impact: Short pulse durations prevent significant heat buildup, protecting sensitive substrates.
- Adjustable Parameters: Ability to fine-tune pulse frequency, energy, and duration for specific cleaning tasks.
- Versatility: Effective on a wide range of materials, including metals, plastics, ceramics, and composites.
Applications
- Cultural Heritage Restoration: Gentle cleaning of historical artifacts, sculptures, and artworks.
- Microelectronics: Removal of oxides and residues from semiconductor components.
- Aerospace and Automotive Industries: Precise cleaning of engine parts, molds, and delicate components.
- Medical Devices: Sterilization and cleaning of surgical instruments without chemical residues.
Advantages
- Selective Removal: Can target specific layers or types of contaminants.
- Minimal Substrate Damage: Reduces the risk of altering or damaging the base material.
- Eco-Friendly: No need for chemicals or abrasive materials.
- High Efficiency: Rapid cleaning speeds with excellent surface quality.
Continuous Wave Laser Cleaning Machines
Continuous wave laser cleaning machines emit a constant, uninterrupted laser beam to remove contaminants. This continuous output delivers sustained energy to the surface, making it effective for removing thicker layers of material, such as heavy rust or coatings.
Key Features
- High Power Output: Generally higher average power compared to pulsed lasers, enabling the removal of more substantial contaminants.
- Deep Penetration: Effective in cleaning deeper layers and more resilient contaminants.
- Steady Energy Delivery: Provides consistent cleaning results over large surface areas.
- Robust Construction: Designed for heavy-duty industrial applications.
Applications
- Industrial Cleaning: Removal of thick rust, paint, and coatings from large metal structures.
- Shipbuilding and Marine Industries: Cleaning of ship hulls, decks, and offshore platforms.
- Manufacturing Lines: Integration into automated systems for continuous surface preparation.
- Oil and Gas Industry: Maintenance of pipelines, tanks, and heavy machinery.
Advantages
- Fast Cleaning Rates: Suitable for large-scale cleaning tasks where speed is crucial.
- Cost-Effective for Heavy Contamination: Reduces labor and time costs for substantial cleaning jobs.
- Durable Performance: Built to withstand demanding industrial environments.
- Simplified Operation: Continuous mode can be easier to operate for uniform cleaning tasks.
Comparison and Selection Guide
Choosing the Right Type for Your Needs
- Material Sensitivity: Pulse Laser Cleaning Machines are preferable for sensitive materials that require minimal thermal impact. Continuous Wave Laser Cleaning Machines are suitable for robust materials where heat input is less of a concern.
- Contaminant Characteristics: Pulse Lasers excel at removing thin layers, delicate residues, or specific layers without affecting underlying materials. Continuous Wave Lasers are ideal for heavy rust, thick paint, and substantial coatings.
- Precision vs. Speed: Pulse Lasers offer higher precision, making them suitable for detailed work. Continuous Wave Lasers provide faster cleaning speeds for large areas.
- Industry Application: Pulse Lasers are commonly used in aerospace, electronics, and cultural preservation. Continuous Wave Lasers are favored in heavy industries like shipbuilding, construction, and manufacturing.
- Budget Considerations: Evaluate the cost of the machine relative to the specific requirements of your application. Consider operational costs, including energy consumption and maintenance.
Maxcool CNC's Offerings
Maxcool CNC provides a comprehensive range of both pulse and continuous wave laser cleaning machines:
Pulse Laser Cleaning Machines:
- Models ranging from low to high power.
- Customizable settings for specialized applications.
- Advanced control systems for precise operation.
Continuous Wave Laser Cleaning Machines:
- High-power models designed for industrial use.
- Robust construction for durability.
- Options for integration into existing production lines.
Our team of experts can assist you in assessing your specific needs and recommend the most suitable laser cleaning machine. With our commitment to innovation and customer satisfaction, we ensure that you receive a solution that enhances efficiency and delivers superior cleaning performance.
By understanding the differences between Pulse and Continuous Wave Laser Cleaning Machines, you can make an informed decision that aligns with your operational requirements and business goals. Whether you need precision cleaning for delicate components or rapid removal of heavy contaminants, Maxcool CNC has the right equipment to meet your needs.
Applications of Laser Cleaning Machines
Laser cleaning machines have transformed the way industries approach surface preparation and contaminant removal. By offering a non-contact, eco-friendly, and highly precise cleaning method, laser technology addresses many of the limitations found in traditional cleaning techniques. Below are some of the key areas where laser cleaning machines excel:
Rust and Oxide Removal
Rust and oxides are common issues that affect metal components, leading to degradation, reduced performance, and structural failures. Traditional rust removal methods like sandblasting or chemical treatments can be abrasive, environmentally harmful, and often inefficient.
Laser Cleaning Advantages
- Precision Removal: Targets rust and oxides without damaging the underlying metal substrate.
- Non-Abrasive: Eliminates the risk of surface wear and deformation.
- Eco-Friendly: No chemicals or abrasive materials are required, reducing environmental impact.
- Efficiency: Rapid cleaning speeds and minimal setup time increase productivity.
Industries Benefited
- Automotive: Restoration of car parts, chassis, and frames.
- Aerospace: Maintenance of aircraft components where material integrity is crucial.
- Manufacturing: Preparation of metal surfaces before welding or painting.
- Oil and Gas: Cleaning pipelines, tanks, and drilling equipment.
Paint and Coating Removal
Removing old paint or coatings can aid in the maintenance, inspection, or repainting process. Traditional methods such as chemical stripping or mechanical scraping can be labor-intensive and may damage the substrate or create hazardous waste.
Laser Cleaning Advantages
- Selective Layer Removal: Precisely removes specific layers without affecting underlying materials.
- Surface Preservation: Maintains the integrity and properties of the base material.
- Reduced Waste: Minimizes secondary waste generation compared to abrasive methods.
- Safety: Eliminates the need for hazardous chemicals, improving worker safety.
Industries Benefited
- Shipbuilding and Marine: Stripping paint from ship hulls and offshore structures.
- Infrastructure Maintenance: Cleaning bridges, railways, and large steel structures.
- Manufacturing: Removing coatings from machinery and equipment for refurbishment.
- Art and Decor: Restoring sculptures and installations without damaging the artwork.
Surface Preparation
Proper surface preparation facilitates processes such as welding, bonding, and coating. Contaminants such as oils, greases, and residues can compromise adhesion and lead to product failures.
Laser Cleaning Advantages
- Enhanced Adhesion: Provides a clean surface that improves bonding and coating adherence.
- Consistent Quality: Delivers uniform cleaning results across different surfaces.
- Time-Saving: Faster than manual cleaning methods, reducing production downtime.
- Integration Capability: This can be incorporated into automated production lines for continuous processing.
Industries Benefited
- Automotive and Aerospace: Pre-welding cleaning of components to ensure strong welds.
- Electronics: Preparation of circuit boards and connectors for soldering.
- Medical Devices: Sterilization and preparation of equipment for coating or assembly.
- Energy Sector: Cleaning turbine blades and generator components.
Mold Cleaning
Molds used in manufacturing processes accumulate residues, release agents, and product buildup that can affect the quality and precision of molded parts. Traditional cleaning methods may involve disassembly and abrasive techniques that wear down the mold surfaces.
Laser Cleaning Advantages
- Non-Contact Cleaning: Preserves the mold’s dimensional accuracy and surface finish.
- In-Place Cleaning: Often allows for cleaning molds without disassembly, saving time.
- Reduced Wear: Extends the lifespan of molds by eliminating abrasive cleaning methods.
- Minimal Downtime: A faster cleaning process enables a quicker return to production.
Industries Benefited
- Plastics and Rubber Manufacturing: Maintenance of injection molds and extrusion dies.
- Metal Casting: Cleaning of molds used in die-casting and forging.
- Food and Beverage: Sanitation of molds used in food processing without contamination risk.
- Pharmaceuticals: Cleaning molds for tablet pressing and capsule forming.
Restoration and Conservation
Preserving cultural heritage objects and artworks requires delicate cleaning methods that do not harm the original materials. Laser cleaning offers a controlled approach to remove pollutants, biological growth, and previous restoration materials.
Laser Cleaning Advantages
- Gentle Cleaning: Adjustable parameters allow for the safe removal of contaminants from sensitive surfaces.
- Selective Removal: Targets unwanted layers without affecting underlying patinas or finishes.
- Non-Toxic Process: Eliminates the use of chemicals that could damage artifacts or pose health risks.
- Documentation and Control: Provides precise control over the cleaning process, important for conservation records.
Industries Benefited
- Museums and Galleries: Restoration of paintings, sculptures, and historical artifacts.
- Architectural Conservation: Cleaning of historic buildings, monuments, and facades.
- Archaeology: Preservation of findings without altering or damaging them.
- Religious Sites: Maintenance of temples, churches, and other sacred structures.
By leveraging the capabilities of laser cleaning machines, businesses can achieve higher efficiency, better quality outcomes, and a reduction in operational costs. Whether it’s enhancing the lifespan of molds, preparing surfaces for critical processes, or preserving priceless artifacts, laser cleaning stands out as a superior solution.
Factors to Consider When Buying
Purchasing a laser cleaning machine is a significant investment that can greatly enhance your operational efficiency, product quality, and environmental compliance. However, selecting the right machine requires careful consideration of several critical factors to ensure it meets your specific needs. Below are the key aspects you should evaluate when making your decision.
Assessing Your Cleaning Needs
Understanding the Scope of Your Applications
- Type of Contaminants: Identify the specific contaminants you need to remove, such as rust, paint, oils, oxides, or residues. Different contaminants may require different laser parameters.
- Surface Material: Determine the substrates you will be working with—metals, plastics, ceramics, or composites—as material properties affect laser interaction.
- Precision Requirements: Assess whether you need high-precision cleaning for delicate components or if bulk cleaning suffices for larger surfaces.
- Volume and Frequency: Estimate the workload in terms of cleaning frequency and the size of items to be cleaned to choose a machine that can handle your operational demands.
Questions to Ask
- What are the primary applications for the laser cleaning machine?
- Do I require portability for on-site cleaning tasks?
- Will the machine be integrated into an existing production line?
Material Compatibility
Ensuring Effective and Safe Cleaning
- Laser Wavelength and Material Interaction: Different materials absorb laser energy differently. Ensure the machine’s laser wavelength is compatible with your substrate to avoid damage.
- Reflectivity Considerations: Highly reflective materials like copper or aluminum may require specialized lasers to achieve effective cleaning.
- Heat Sensitivity: For heat-sensitive materials, consider pulse laser cleaning machines that minimize thermal impact.
- Testing and Validation: Whenever possible, conduct sample tests on your materials to verify cleaning effectiveness and substrate preservation.
Questions to Ask
- Is the laser cleaning machine suitable for all the materials I intend to clean?
- Does the manufacturer provide material compatibility data or testing services?
Required Power and Efficiency
Matching Machine Capabilities with Cleaning Tasks
- Laser Power Selection: High power (1000W – 3000W) is suitable for heavy-duty cleaning, such as thick rust or paint removal, while low to medium power (100W – 500W) is ideal for precision cleaning and washing delicate surfaces.
- Cleaning Speed: Higher power generally translates to faster cleaning speeds, increasing productivity.
- Beam Quality: Better beam quality allows for more precise cleaning and efficiency.
- Adjustability: Look for machines with adjustable parameters (power, pulse frequency) for versatility across different tasks.
Questions to Ask
- What laser power level is appropriate for my cleaning requirements?
- Do I need the flexibility to adjust laser parameters for different applications?
Budget Considerations and ROI
Balancing Cost with Long-Term Benefits
- Initial Investment: Determine your budget range while considering the quality and features required.
- Operational Costs: Factor in energy consumption, maintenance, and potential consumables.
Return on Investment (ROI)
- Increased Productivity: Faster cleaning times reduce labor costs.
- Reduced Downtime: Improved efficiency leads to higher operational uptime.
- Longevity: High-quality machines may have a higher upfront cost but offer longer service life.
- Financing Options: Explore leasing, financing plans, or government incentives for adopting eco-friendly technologies.
Questions to Ask
- What is the total cost of ownership over the machine’s lifespan?
- How quickly can I expect to see a return on my investment?
Safety Features and Compliance
Ensuring Operator Safety and Regulatory Adherence
- Safety Mechanisms: An interlock system prevents accidental laser firing when the access panel is open. An emergency stop button allows for immediate shutdown in an emergency, while a protective cover protects the operator from laser exposure and contains debris.
- Certification: The machine needs to comply with European safety standards and for certain applications in the United States, FDA standards are required. ISO certification indicates compliance with quality and safety management systems. In addition, the machine should comply with environmental regulations regarding emissions and waste.
Questions to Ask
- Does the machine meet all relevant safety standards and certifications?
- What safety features are included to protect operators?
- Is training provided for my staff?
Investing in a laser cleaning machine is a strategic decision that can significantly enhance your operational capabilities. With the right machine, you can achieve superior cleaning results, improve efficiency, and gain a competitive edge in your industry.
Key Factors to Consider When Buying a Laser Cleaning Machine
Investing in a laser cleaning machine is a strategic decision that can significantly enhance your cleaning processes across various industrial applications. To make an informed choice, it’s essential to evaluate several critical factors that influence the machine’s performance, suitability, and return on investment. Below are the key considerations to keep in mind when selecting a laser cleaning machine from a reputable manufacturer.
Laser Power
Understanding the Importance of Laser Power
Power Range
- Laser cleaning machines are available in various power levels, typically ranging from 100W to over 3000W.
Application Suitability
- Low Power (100W – 300W): Ideal for delicate tasks such as removing thin coatings, cleaning sensitive surfaces, and precision applications.
- Medium Power (500W – 1000W): Suitable for general-purpose cleaning, including rust removal, paint stripping, and oxide layer elimination.
- High Power (1500W – 3000W): Designed for heavy-duty industrial applications like thick rust removal, extensive paint stripping, and large-scale surface preparation.
Considerations
- Material Thickness: Thicker contaminants require higher laser power for effective removal.
- Cleaning Speed: Higher power levels generally offer faster cleaning rates, increasing productivity.
- Energy Consumption: Balance the need for power with energy efficiency to manage operational costs.
Laser Type
Choosing Between Continuous Wave and Pulsed LasersChoosing Between Continuous Wave and Pulsed Lasers
Continuous Wave (CW) Lasers
- Emit a constant, uninterrupted laser beam.
- Provide steady energy input suitable for removing heavy contaminants.
- Ideal for applications where speed is prioritized over precision.
Pulsed Lasers
- Emit laser energy in short bursts or pulses.
- Offer precise control over energy delivery, reducing thermal impact on substrates.
- Suitable for delicate surfaces and applications requiring high precision.
Considerations
- Thermal Sensitivity: Pulsed lasers minimize heat buildup, protecting sensitive materials.
- Application Needs: Choose CW lasers for heavy-duty tasks and pulsed lasers for precision work.
- Cost Implications: Pulsed lasers may be more expensive due to their advanced technology.
Pulse Duration and Frequency
Fine-Tuning Laser Performance
Pulse Duration
- Refers to the length of each laser pulse.
- Shorter durations (nanoseconds, picoseconds) allow for precise cleaning with minimal thermal impact.
Pulse Frequency
- The number of pulses emitted per second.
- Higher frequencies can increase cleaning speed but may affect the depth of penetration.
Considerations
- Material and Contaminant Type: Adjust pulse settings based on the substrate and contaminant characteristics.
- Desired Outcome: Balance frequency and duration to achieve optimal cleaning without damaging the material.
Material Compatibility
Ensuring Effective Cleaning Across Various Materials
Substrate Types
- Metals: Steel, aluminum, copper, brass.
- Non-Metals: Plastics, composites, stone, glass.
Contaminant Types
- Rust, oxides, paints, coatings, oils, residues.
Considerations
- Absorption Rates: Different materials absorb laser energy differently, ensuring the laser wavelength is compatible.
- Testing: Conduct sample cleaning tests to verify effectiveness and avoid substrate damage.
Cleaning Speed and Efficiency
Maximizing Productivity
Cleaning Rate
- Measured in square meters per hour.
- Dependent on laser power, type, and machine configuration.
Beam Quality and Spot Size
- High beam quality allows for finer spot sizes and greater precision.
- Adjustable spot sizes offer flexibility for various cleaning tasks.
Considerations
- Operational Requirements: Match the machine’s capabilities with your production volume and timelines.
- Efficiency vs. Precision: Higher speeds may reduce precision, so find the right balance for your application.
Portability and Design
Selecting the Right Configuration for Your Needs
Portable Machines
- Lightweight and compact.
- Ideal for on-site cleaning or hard-to-reach areas.
- Examples include handheld units and backpack designs.
Stationary Machines
- Fixed installations suitable for production lines.
- Offer higher power and integration capabilities.
- May include robotic arms or automation features.
Considerations
- Workspace Constraints: Evaluate the physical space and mobility requirements.
- Ergonomics: User-friendly designs enhance operator comfort and reduce fatigue.
Cooling System
Maintaining Optimal Operating Temperatures
Air Cooling
- Suitable for lower-power lasers.
- Simpler and more cost-effective.
Water Cooling
- Necessary for high-power lasers to dissipate heat effectively.
- Ensures consistent performance and prolongs laser life.
Considerations
- Environmental Conditions: High ambient temperatures may necessitate more robust cooling solutions.
- Maintenance: Water-cooled systems require regular checks to prevent leaks and contamination.
Control Systems and Software
Enhancing Usability and Integration
User Interface
- Intuitive controls with touchscreen panels.
- Easy adjustment of laser parameters and cleaning modes.
Software Capabilities
- Preset programs for common cleaning tasks.
- Customizable settings for specific applications.
- Connectivity options for remote monitoring and diagnostics.
Considerations
- Operator Training: Ensure the system is user-friendly or that training is provided.
- Compatibility: Ability to integrate with existing systems or automation setups.
Safety Features
Protecting Operators and Equipment
- Interlock Systems: Prevent laser emission when safety conditions are not met.
- Emergency Stop Buttons: Immediate shutdown in case of an emergency.
- Protective Enclosures: Shielding to contain laser radiation and debris.
- Warning Indicators: Visual and auditory alerts for operational status and hazards.
Considerations
- Regulatory Compliance: Machines should meet safety standards such as CE marking or FDA regulations.
- Personal Protective Equipment (PPE): Assess the need for laser safety glasses or other PPE.
Maintenance Requirements
Ensuring Longevity and Reliability
Routine Maintenance
- Regular cleaning of optics and laser components.
- Inspection of electrical and mechanical parts.
Service Support
- Availability of technical assistance and spare parts.
- Warranty terms and conditions.
Considerations
- Downtime Minimization: Efficient maintenance procedures reduce operational interruptions.
- Cost of Ownership: Factor in maintenance costs over the machine’s lifespan.
Cost and Budget Considerations
Balancing Investment with Performance
- Initial Purchase Price: Assess the cost of the machine’s features and capabilities.
Operational Costs
- Energy consumption.
- Maintenance and consumables.
Return on Investment (ROI)
- Increased productivity and efficiency.
- Reduction in labor and material costs.
Considerations
- Financing Options: Explore leasing, financing plans, or grants that may be available.
- Total Cost of Ownership: Consider long-term costs, not just the initial investment.
Brand Reputation and After-Sales Support
Choosing a Reliable Partner
- Manufacturer Expertise: Opt for companies with a proven track record like Maxcool CNC.
- Customer Testimonials: Positive reviews and case studies indicate reliability.
After-Sales Services
- Installation assistance.
- Training programs.
- Technical support and troubleshooting.
Considerations
- Global Presence: Manufacturers with a worldwide network can offer better support.
- Customization: The ability to tailor machines to specific needs enhances value.
Invest in a laser cleaning machine that not only meets your current requirements but also adapts to future challenges.
Comparison with Traditional Cleaning Methods
When considering laser cleaning technology, it is important to fully understand how it compares to traditional cleaning methods. Conventional techniques like chemical cleaning, sandblasting, and mechanical buffing have been used for decades across various industries. Below is a detailed comparison of these traditional methods with laser cleaning.
Chemical Cleaning
Chemical cleaning involves the use of solvents, acids, alkalis, or other chemical agents to dissolve or loosen contaminants from surfaces. It’s commonly used for removing rust, scale, oils, and other residues from metals and other materials.
Advantages
- Effectiveness on Specific Contaminants: This can be highly effective for certain types of deposits.
- Ease of Application: Chemicals can be applied in situ without the need for specialized equipment.
- Cost: Initial investment is generally low compared to advanced machinery.
Disadvantages
- Environmental Impact: Generates hazardous waste that requires proper disposal, contributing to environmental pollution.
- Health and Safety Risks: Exposure to toxic chemicals poses risks to workers, necessitating strict safety protocols.
- Surface Damage: Chemicals can corrode or weaken the substrate material if not used carefully.
- Process Time: Often involves lengthy soaking periods and multiple steps, reducing efficiency.
Laser Cleaning Advantages Over Chemical Cleaning
- Eco-Friendly: Eliminates the need for harmful chemicals, reducing environmental contamination.
- Non-Destructive: Precisely removes contaminants without damaging the substrate.
- Safety: Minimizes exposure to hazardous substances for operators.
- Efficiency: Faster cleaning times increase productivity and reduce downtime.
Sandblasting
Sandblasting, also known as abrasive blasting, uses a high-pressure stream of abrasive material to remove surface contaminants. Common abrasives include sand, glass beads, and steel grit.
Advantages
- Effective Cleaning: Removes rust, paint, and scale efficiently.
- Surface Profiling: This creates a rough surface ideal for coating adhesion.
- Versatility: Can be used on a variety of materials and surface sizes.
Disadvantages
- Surface Erosion: Can damage the substrate material by removing some of it along with the contaminants.
- Dust Generation: Produces a significant amount of dust and debris, requiring containment measures.
- Health Risks: Inhalation of fine abrasive particles poses serious health risks like silicosis.
- Equipment Wear: Abrasive materials cause wear and tear on equipment, increasing maintenance costs.
Laser Cleaning Advantages Over Sandblasting
- Precision: Targets only the contaminants without affecting the substrate.
- Clean Process: Generates minimal secondary waste, simplifying cleanup.
- Safety: Reduces airborne particulates, enhancing workplace safety.
- Lower Maintenance: The non-contact process reduces wear on equipment components.
Mechanical Buffing
Mechanical buffing involves using abrasive tools like brushes, pads, or wheels to physically scrub contaminants from surfaces. It’s often used for polishing metals and removing minor surface imperfections.
Advantages
- Surface Enhancement: This can improve surface finish and aesthetics.
- Simple Equipment: Requires basic tools that are relatively inexpensive.
- Accessibility: Suitable for small-scale operations and spot treatments.
Disadvantages
- Labor-Intensive: Requires manual effort, leading to higher labor costs and potential inconsistencies.
- Surface Damage Risk: This can introduce scratches, grooves, or uneven wear on the substrate.
- Consumable Costs: Abrasive tools wear out and need frequent replacement.
- Inefficiency on Heavy Contaminants: Not effective for thick rust layers or hard coatings.
Laser Cleaning Advantages Over Mechanical Buffing
- Non-Abrasive: Eliminates physical contact, preventing scratches and preserving the substrate’s integrity.
- Consistency: Provides uniform cleaning results with programmable settings.
- Efficiency: Faster processing times reduce labor costs and increase throughput.
- Versatility: Capable of handling a wide range of contaminants and materials.
Summary Comparison Table
Criteria | Chemical Cleaning | Sandblasting | Mechanical Buffing | Laser Cleaning |
Environmental Impact | High | Moderate to High | Moderate | Low |
Health and Safety Risks | High | High | Moderate | Low |
Surface Damage Risk | High | Moderate to High | High | Low |
Efficiency | Low | Moderate | Low | High |
Precision | Low | Low | Moderate | High |
Operational Costs | Moderate | High | Moderate | Moderate (Lower over time) |
Waste Generation | High | High | Moderate | Low |
Equipment Wear | Low | High | High | Low |
While traditional cleaning methods like chemical cleaning, sandblasting, and mechanical buffing have their place, they come with significant drawbacks in terms of environmental impact, safety risks, and potential damage to the substrates. Laser cleaning technology offers a superior alternative that addresses these issues effectively. Choosing laser cleaning not only modernizes your cleaning processes but also positions your business as a leader in adopting sustainable and advanced technologies.
Steps to Purchasing the Right Laser Cleaning Machine
Investing in a laser cleaning machine is a strategic decision that can significantly enhance your operational efficiency and product quality. To ensure you select the most suitable machine for your specific needs, it’s essential to follow a systematic approach. Below are the key steps to guide you through the purchasing process.
Assessing Your Cleaning Needs
Understanding the Scope and Requirements
- Identify Contaminants: Determine the types of contaminants you need to remove, such as rust, paint, oils, oxides, or residues. Different contaminants may require specific laser parameters for effective removal.
- Material Types: Consider the substrates you’ll be cleaning—metals, plastics, composites, or ceramics. Material properties influence the choice of laser wavelength, power, and type.
- Precision vs. Speed: Decide whether your applications require high precision (e.g., delicate components) or if cleaning speed is the priority (e.g., large surfaces with heavy contamination).
- Work Environment: Assess whether you need a portable machine for on-site tasks or a stationary unit integrated into a production line.
- Volume and Frequency: Estimate the workload in terms of cleaning frequency and the size and number of items to be cleaned.
Action Steps
- Create a detailed list of your cleaning requirements.
- Prioritize features based on your operational needs.
- Consider future scalability to accommodate potential growth or new applications.
Consulting with Manufacturers
Leveraging Expertise for Informed Decisions
- Research Reputable Manufacturers: Look for companies with a proven track record in laser cleaning technology, like Maxcool CNC.
- Initiate Contact: Reach out to manufacturers to discuss your specific requirements in detail.
Ask Relevant Questions
- What models do you recommend for my applications?
- How do your machines handle specific contaminants and materials?
- What customization options are available?
Evaluate Responsiveness
- A manufacturer’s willingness to provide detailed information and support is a good indicator of their reliability.
Action Steps
- Prepare a list of questions and concerns to address with the manufacturer.
- Request brochures, technical specifications, and case studies.
- Inquire about after-sales support, training, and warranty terms.
Testing and Demonstrations
Validating Performance and Compatibility
- Request Sample Testing: Provide the manufacturer with samples of your materials for cleaning trials.
Attend Live Demonstrations
- Observe the machine’s performance on your specific applications.
- Evaluate the quality of cleaning, speed, and ease of operation.
Assess User Experience
- Check the intuitiveness of the control system and software.
- Ensure the machine’s ergonomics suit your operators’ needs.
Gather Feedback
- Involve your technical team to provide insights on the machine’s compatibility with your processes.
Action Steps
- Schedule demonstrations at the manufacturer’s facility or request on-site demos.
- Analyze the results of sample tests carefully.
- Ask for references or testimonials from existing customers.
Evaluating the Total Cost of Ownership
Understanding Long-Term Financial Implications
- Initial Investment: Consider the purchase price relative to your budget constraints and the machine’s capabilities.
Operational Costs
- Energy Consumption: Higher-powered machines may consume more electricity.
- Maintenance: Factor in routine maintenance, potential repairs, and the availability of spare parts.
- Consumables: Although laser cleaning minimizes consumable use, some components may require periodic replacement.
Return on Investment (ROI)
- Productivity Gains: Faster cleaning times can reduce labor costs and increase throughput.
- Quality Improvements: Enhanced cleaning quality may lead to better product performance and customer satisfaction.
- Financing Options: Explore leasing arrangements, financing plans, or potential grants for adopting eco-friendly technologies.
Action Steps
- Conduct a cost-benefit analysis comparing different models and manufacturers.
- Consider the machine’s lifespan and how quickly it will pay for itself through operational savings.
- Discuss financing options with the manufacturer.
Considering Customization Options
Tailoring the Machine to Your Specific Needs
Technical Customizations
- Laser Power and Type: Adjustments to power levels, pulse duration, and frequency to suit your applications.
- Optics and Beam Delivery: Customizable to handle specific cleaning tasks or materials.
Design Modifications
- Portability Features: Options like handheld units, backpack designs, or trolley systems.
- Integration Capabilities: Ability to integrate with existing automation systems or production lines.
Software Customizations
- User Interface: Tailored control panels and software features for ease of use.
- Preset Programs: Custom cleaning modes for recurring tasks.
Additional Accessories
- Safety Enclosures: Customized shielding or protective barriers.
- Dust Extraction Systems: Enhanced systems for specific environments or contaminants.
Action Steps
- Discuss customization needs during consultations with the manufacturer.
- Evaluate the cost implications and lead times for custom options.
- Ensure that customizations comply with safety regulations and standards.
Purchasing the right laser cleaning machine involves a thorough assessment of your needs, engaging with knowledgeable manufacturers, validating machine performance through testing, understanding the financial aspects, and considering customization options. By following these steps, you can make an informed decision that enhances your operations and provides a solid return on investment.
Summary
Investing in a laser cleaning machine is a strategic move that can significantly enhance your operational efficiency, product quality, and environmental compliance. By understanding the different types of laser cleaning machines—such as pulsed and continuous wave lasers—and their applications in rust and oxide removal, paint stripping, surface preparation, mold cleaning, and restoration, you can select a machine that best fits your needs. Key factors to consider include laser power, laser type, pulse duration and frequency, material compatibility, cleaning speed, portability, cooling systems, control software, safety features, maintenance requirements, cost, and after-sales support. Comparing laser cleaning with traditional methods like chemical cleaning, sandblasting, and mechanical buffing highlights its superior efficiency, precision, and eco-friendliness. By thoroughly assessing your cleaning needs, consulting with reputable manufacturers, testing equipment, evaluating the total cost of ownership, and considering customization options, you can make an informed purchasing decision. Maxcool CNC, as a professional manufacturer of laser welding machines and laser cleaning machines, is dedicated to providing advanced, reliable solutions tailored to your specific requirements.